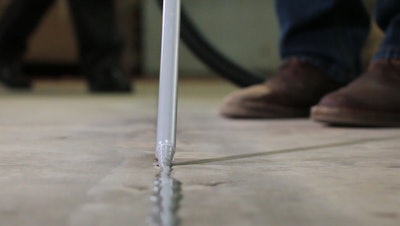
A control joint (or contraction joint) is intended to induce cracking in a concrete slab. Think of it as a “planned” crack; a joint cut into a slab to ensure that as the concrete slab continues to shrink, cracks occurring will do so in a straight, maintainable line at the joint, below the finished concrete surface, as opposed to randomly throughout the slab. In indoor construction, crack fillers have evolved to transfer floor loads between slabs and protect the slab edges from spalling.
Random cracking results in a slab that is not only unattractive, but challenging to maintain. And while most shrinkage occurs within the first year, a concrete slab can continue to shrink and move for years.
Any interior concrete, anything from residential slabs to decorative applications to commercial and industrial floors will utilize control joints.
Control joint fillers - evolution
Control joint fillers are flowable and easy to apply with consistency.SpecChem
In the early days of control joints, various soft or very flexible materials were used to fill control joints, if the joint was even to be filled at all, primarily to keep debris and contaminants out of the joint. As decades passed, improvements in equipment and machinery produced hard wheels on pallet jacks and fork lifts, which started impinging on the exposed joint edges, causing spalling to occur.
The industry then over compensated with rigid, high-strength epoxy-based products that’ while offering outstanding joint edge protection, welded the slab panels together. As the slab continued to shrink, the “welding” would prevent the joint from opening, causing random stress cracking to occur in the slab.
Modern control joint fillers
After the application pictured here is what a control joint on warehouse floor should look like.SpecChem
Durometer, or hardness, has become one of the key parameters in considering a proper control joint filler. A Shore A durometer of 80-85 offers the optimal hardness for transferring wheel loads across the joint while maintaining the flexibility that prevents the slabs from being welded together.
Another key physical property is that if the joint movement exceeds the capability of the joint filler, the product, not the concrete, will tear cohesively or adhesively rather than delaminating the concrete itself. This tear is by design and does not constitute a failure of the joint filler. Other than appearance, this tear, does not inhibit the joint filler from functioning and can be refilled with proper preparation later.
Today, there are two basic types of control joint filler products that meet today’s ACI and PCA standards for a semi-rigid control joint filler. Semi-rigid epoxy-based and semi-rigid polyurea control joint fillers both offer the ability to meet the above durometer range while providing additional advantages to applicators, contractors, and project owners.
Epoxy Control Joint Fillers
Semi-rigid, epoxy-based control joint filler products can have several advantages over the rigid, structural epoxy fillers used previously.
These epoxies incorporate the proper 80-85 durometer hardness but also the flexibility to help prevent welding the slabs together, which can result in delamination of the concrete slab. Semi-rigid epoxy joint fillers, when mixed properly, provide a smooth, flowable easy to pour consistency.
And convenience. Epoxy-based control joint fillers are typically available in one-to-one ratio, easy-to-use options that, due to their long pot life, can be poured, manually applied with a bulk gun, or pumped with a dual component pump.
Epoxy control joint fillers are usually shaved the next day, and may require heat to facilitate cutting to get a smooth shave.
Although not as prevalent as polyureas, epoxies can be formulated in colors.
Polyurea Control Joint Fillers
Once filled, the filler is often shaved for an even fill. Pictured here is a polyurea joint filler.SpecChem
They are also generally found in one-to-one ratio, easy-to-use options, often in cartridges for manual application or pumped with a dual component pump.
Semi-rigid, polyurea control joint fillers, however, have several unique advantages of their own.
Polyurea joint fillers are fast-setting - there are products on the market that can be shaved and open to traffic within thirty minutes. The fast-setting and quick shaving capabilities of polyureas also make them ideal for re-caulking or repairing existing joints and cracks in existing floors where a long shutdown is unacceptable.
Polyurea material also allows for application and curing down to very low temperatures, sometimes as low as -20° F, opening it up to unique applications such as commercial cold storage spaces.
Polyurea joint fillers can also be produced in a variety of color options.
Conclusion & Key Takeaways
Concrete control joints and the products used to fill them have come a long way in meeting the diverse needs of today’s industrial and commercial warehousing and distribution industries. As these technologies continue to evolve to meet growing and ever-changing demands, keep a few key points in mind:
The key to choosing the proper control joint filler is maintaining the proper hardness, the Shore A durometer of 80-85, to transfer loads, easy to apply consistency while still maintaining the flexibility to move with the floor as shrinkage occurs over time.
Pictured here is a typical warehouse floor with control joints.SpecChem
The key to a successful, long-term control joint application in today’s warehousing/distribution center floors is to give the slab enough time – generally 60-90-120 days – to maximize shrinkage, allowing joints to open, which minimizes the long-term potential for tearing.
Finally, project owners need to consider the cost of filling their control joints for new construction. On average, filling control joints costs approximately $2.00 per linear foot. Instead of comparing this to not filling the joints at all, consider the repair costs involved with not filling the joints initially. The repair costs involved with repairing damaged or spalled control joints can range from $5.00 to $10.00 per linear foot.