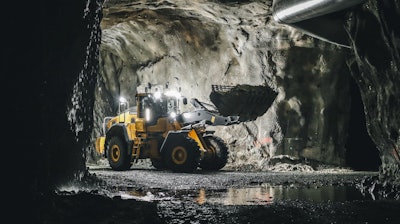
Volvo Construction Equipment (Volvo CE) has been involved in a Swedish research project which demonstrated that, by applying the latest technology within communication and automation, underground mines could become more efficient and safer.
In the Pilot for Industrial Mobile Communication in Mining (PIMM) project, Volvo CE developed and tested "super remote control" of a standard 25-ton L180H wheel loader located 1,300+ ft. (400 meters) underground, while the operator commanded the machine from a comfortable office on the surface. This non-line-of-sight operation meant the distance between the loader and the machine was "arbitrary" - meaning the machine could be operated from virtually anywhere in the world.
The research project was conducted from 2015 to 2018. It was made possible with the help of other companies and organizations, including Boliden, Ericsson, Telia, ABB, RISE SICS and LTU, which joined forces on the project to explore what the next generation of mobile communication technology, 5G, could mean for business models and communications in a mine.
Testing technology in a real environment
The PIMM project installed the latest technology for mobile communications in Boliden’s Kankberg underground mine in Sweden to test how it performed in a challenging application under tough industrial conditions. In a mine, network delays could have major consequences for safety and productivity.
“Volvo CE’s mission statement for the project was to prove that the technology we’re developing internally is applicable in a customer environment,” says Erik Uhlin, Advanced Engineering Program Leader. “We wanted to highlight that industrial applications in mobile networks aren’t just something out of science fiction – they’re real."
By collaborating with partners, Volvo CE gained knowledge and experience of data links via mobile networks for real-time control. The mobile network that Ericsson built for the Kankberg mine featured the latest in wireless technology. The system was so fast and reliable that it enabled the wheel loader to be controlled from above ground.
Volvo CE pilots pioneering 5G technology
“The benefit of working with other technology-based companies is huge,” said Uhlin. “There was a great openness and willingness to collaborate that further increased what everyone got out of the project. All the partners openly shared their advanced technology and knowledge within digitalization and automation and it was because of this collaboration that the project was a success.”
Establishing customer goals
"Testing was carried out while production was taking place and that was demanding – but it meant that we were working with real problems, in a real environment," Uhlin noted. "The collaboration between all the partners resulted in us showcasing that a future underground mine could not only be more efficient, but also safer.”
Boliden set a goal to eliminate accidents in its mining operation areas and have no human exposure at the production face by the year 2030. “The best way to avoid accidents is to take the operator away from a dangerous environment where accidents can occur," said Uhlin. "Remote control is a natural method to improve your safety situation.”
One of the benefits Boliden hoped to see from the research project was increased personal quality of life. “The mine is a pretty rough environment. It’s dark; it’s damp. If you can move the operator out of the wheel loader and put them in an office environment on the surface, it’s a big change in quality for the operator," said Fredrik Kauma, project manager, mine automation. Boliden also saw potential to increase production. For example, prior to blasting in the mine, all personnel must be removed and the area vented following the blast before restarting operations. With remote control, operations could be resumed more quickly.
However, there was concern about maintaining flexibility. Remote control has been around since about the late 1980s, but has typically been used for pre-programmed, dedicated tasks. Boliden's wheel loaders, however, are used for a range of tasks, which aren’t always preplanned. “It’s like a Swiss army knife; we use it for almost anything,” said Kauma. The loaders are used for operations including loading ore onto trucks, moving it to storage areas and dumping it down shafts, as well as moving heavy equipment and other support-related tasks. “It’s crucial for us that remote control cannot hamper this flexibility.”
“For this project, we had to limit the scope in terms of what we wanted to demonstrate,” said Uhlin. As such, three goals were set:
- demonstrate the ability to load ore into trucks – a typical production task for the machine;
- move ore through the mining tunnels;
- and navigate the machine in a productive way in this environment.
A big step beyond simulation
The loader was also equipped with a motion sensor that could translate machine motion to the control station. The motion or force feedback data gives the operator a better feel of what’s going on. “The vibrations and the rocking are severely tuned down, of course, so it’s nothing near what you would experience sitting in the machine, but it still helps to give a connection to the machine," Uhlin indicated. A graphic user interface provides information that may be hard to sense, such as articulation and oscillation of the machine, bucket angle and lift cylinder pressure.
“Measurements that we have done have shown that with about an hour’s training, we reach roughly 80% or greater efficiency compared to if you’re sitting in the cab,” Uhlin said. “The operator environment and control system are very, very similar to what you would have if you were sitting in the machine.”
Throughout the project, a human operator remained in the cab for safety reasons. “Since we were testing in a production area, we need to have a safety driver in the wheel loader at all times in case of an accident," said Kauma. "But we never needed to use the safety driver. Everything went really well.”
Potential to move autonomous systems forward
At this stage, the remotely-controlled wheel loader is not commercially available. But Boliden is hopeful it will be soon.
There are improvements he would like to see, but the project proved a success and Kauma already foresees remote control as part of mining operations in future. “We believe absolutely that this will be commercially viable,” he stated. “Less than a month ago, I spoke to the mine manager of the mine site in which we performed these tests and he asked me when these remote control wheel loaders will be available for sale. That says a lot about how much we believe in this technology.”
Both Kauma and Uhlin believe remote control will help facilitate autonomous operations, as well. “Even if you have full automation or an autonomous vehicle, remote control will still be needed," Kauma said. "If you run an automated vehicle fleet, at some point, they will run into a problem and an autonomous vehicle or machine will stop. At that point, you would like a human operator to be able to take control over the machine and move it from an unsafe area to a safe area, or just out of the way from production traffic. So remote control will be a necessity even if you have full automation.”
“We think that remote control might speed up the introduction of autonomous hauling systems," said Uhlin. "If you’re sitting in a wheel loader loading autonomous trucks, you’re exposed if anything should go wrong with the haul trucks… If you can take the operator out of the cab of the wheel loader, you basically solve the safety problem.”