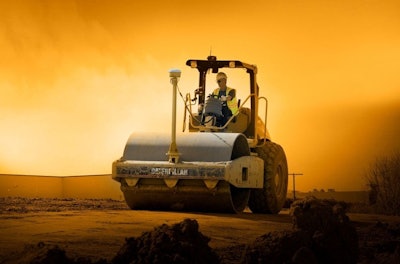
Trimble announced in mid-January the general availability of its Horizontal Steering Control functionality for the Trimble Earthworks Grade Control Platform for Soil Compactors.
This is a first for the compactor equipment class, and steering an articulated piece of equipment like a soil compactor is challenging for even a skilled human operator. Other vendors may not follow in the immediate term. Like the compactor grade control capabilities launched in April of last year, the steering control is not meant to eliminate the need for a human operator as much as perform the repetitive functions of multiple passes over a project with greater accuracy than a human operator while giving the operator override control.
This latest product launch came after decades of work in steering automation, and is only one waypoint on a journey towards heavy construction that is completely autonomous in terms of both steering navigation and productive operation including earthworks disciplines like compaction and grading.
A Mechanical Approach
Trimble’s grade control option typically connects digitally through a machine’s hydraulic electronic control module (ECM), but on older machines not equipped with ECM Trimble dealer technicians will install valves that tap into the hydraulics directly, which then in turn control the system.
“A lot of the equipment these days are electronic hydraulic machines, but on some we still install hydraulic kits,” Trimble Earthmoving Industry Director Cameron Clark said in a phone interview with ForConstructionPros.
Trimble’s compaction steering automation control however is strictly mechanical, attaching to and turning the steering wheel. This would seem to help the operator take control of the machine if necessary.
Mature Technology, Modernized and Ruggedized
Trimble GPS machine control for civilian applications got its start in the mid-1990s, when Trimble and Caterpillar first attached GPS machine control to earthmoving equipment for mining and first equipped agricultural equipment with differential global position system capabilities by using a Coast Guard radio beacon. By 1999, the company launched its first grade control system for construction. In 2000, the company released its first AgGPS Autopilot steering system, accurate within a centimeter.
In the twenty-plus years since steering control came to market, Trimble has invested in additional research and development for both steering and level control components, paving the way for broader application across equipment types. Paving was one of the earliest applications for Trimble’s steering automation, in part due to the predictable and linear nature of the site. Before commercializing the technology for broader applications like dozers, compactors and excavators, the technology had to become more robust.
“We have been doing steering for paving for a long time,” Clark said. “But we found that the previous generation did not have the scalability we needed for the future. We had a big effort to create the earthworks platform—and with so much opportunity in construction, there was a lot of focus on the performance of the system, quality, usability and getting different models to work blade to grade to increase productivity.”
Trimble’s current earthworks products may leverage the mature and proven technology pioneered on the agriculture side of the business, but that navigation module is only part of a client-server architecture. The heart of the entire Trimble earthworks line is an ECM that acts as a server to the other components including a new, improved Nav3 controller for steering and grade control.
The agricultural steering control module went through a transformation on the outside as well as the inside so it could withstand the rigors of the job site.
“For the product we supplied for construction, we specifically designed it for construction sites,” Clark said. “It can work in mud and the rain. The display and interface are also ruggedized.”
Together with Trimble compaction control, this system not only steers articulated compactors more accurately than even an expert operator, but can control and monitor compaction and capture actionable insights that could even be repurposed to document progress against project deliverables.
The color display provides the operator with real-time insights on compaction progress, the number of passes and even compacted soil stiffness. Grade accuracy and compaction are measured together, so equipment can more rapidly deliver a targeted and reliable load-bearing capacity. Compaction measurement values (CMV), the number of passes and other operational metrics can later be analyzed or presented as part of application for payment on the job.
Installs in About a day so Retrofits Popular
A Trimble dealer can install automated steering in a few hours, but will require some additional time to get the steering calibrated. The relatively fast and simple installation of automated steering makes this a viable technology to retrofit existing compactors.
“We do find that for a lot of people with grade control, they get a system when they get a new machine,” Clark said. “But with steering for compactors, they will add functionality to current machines. With compactors, the steering support is generic—if you have a steering wheel, we can provide the solution.”
Aftermarket automation solutions will remain Trimble’s focus according to Clark, but the company does have an OEM agreement to embed their technology as a standard feature on Dynapac soil rollers. And many OEMs offer equipment identified as “Trimble-ready” with brackets to hold the aftermarket components to eliminate the need for welding. Trimble automated steering is widely available across equipment from multiple manufacturers, while support for dozers is currently limited to select Deere, Cat and Komatsu machines.
Clark said their network of dealers were already trained and prepared to install the steering technology, which is not always a given when a new product is launched.
Rapid ROI Potential
Contractors can recover the cost of the aftermarket steering automation equipment and installation quickly, according to Clark.
“With compactors in general, a lot of the time, the operators are the lesser skilled people working on site,” Clark said. “It is a very repetitive task … if you are going up and back repeatedly, it is boring. They might not know the value they are trying to deliver, but it is critical. And it is very hard to steer an articulated machine.”
Enabling a lesser-skilled operator to perform even better than an expert, more expensive one has a measurable upside. Back-of-a-napkin math suggests that during a 10-hour day, an operator may run a compactor over 4,000 square meters, in six passes. In order to avoid missing spots, an operator may run a 30 to 40 percent overlap.
More precise steering may enable a 10 percent overlap, delivering the same compaction results two hours faster. Extrapolating that over a compactor that is run 100 days a year, and a contractor saves 20 days or 200 hours which eliminates cost for the operator, machine wear and fuel. And it can deliver a project faster for an owner.
Additional return can be realized by eliminating manual processes to document the work that has been done, as the passes made and the degree of compaction achieved can be relayed directly into Trimble WorksManager software. The software can also relay construction models to the compactor to automate performance against the latest revision.
Towards Automated Workflows and Autonomy
With automated steering added to perhaps one of the most challenging pieces of equipment, and connected equipment integrated with WorksManager, Trimble can now focus on helping their customers optimize their operations.
“We are really focused on workflows, coordination and optimization,” Clark said. “We launched steering automation, grading and compaction control, so now we are working on the connected workflow."
Enabling optimized sequencing and execution of earthworks projects with technology to assist human operators, though, will soon give way to full autonomy.
“The construction industry has a real problem with a skilled labor shortage, and we want to be able to solve that with increasing the degree of automation the equipment is capable of,” Clark said. “We can automate the blade to grade—adding more value—and then steering gives the operator a defined path where the machine will go. It is just contingent on us now to put more intelligence into the product to further optimize project delivery and productivity.”
Construction equipment automation today functions primarily as a guide-on-the-side rather than as a self-operating technology. Reasons for that include the need to ensure safety, the need to create a machine learning engine that can be taught through ingestion of large amounts of data how to navigate the rapidly changing environment without damaging itself, other equipment or injuring human workers on site. The primary failsafe currently for Trimble’s automated steering on compaction equipment is the operator.
“We allow for operator over-ride—any time you want to seize the steering wheel, an operator will always win,” Clark said, adding that a secondary control is the limited range from the controller.
“There is a well-defined capture zone—and you cannot, once you select automated steering, go anywhere when you are too far from the controller,” Clark said.
Trimble’s automated steering for compaction and other earthworks applications is not currently equipped with electronic eye technology for safety. Trimble Earthworks for Excavators is however equipped with an augmented reality (AR) camera that simulates the view down from on top of the cab. It enables an operator to see a digital model of the site on a monitor, providing awareness of what is going on around the bucket. Full autonomy will require more than machine vision though--images captured by the electronic eye must be interpreted to enable an edge computing application to make decisions about what objects sensed mean for how the machine should operate. Construction equipment must not only see, recognize and respond appropriately to objects in its surroundings but be imbued with the ability to sense and interpret other sensory data like vibration and texture.
As researchers, technology vendors like Trimble and original equipment manufacturers establish a workable method to teach the machines what they need to know to operate autonomously, the industry will progress from remote tele-operation where an operator can control one or multiple pieces of heavy equipment from a remote location to assisted remote operation and then, eventually, full automation. Tele-operation is already available for some equipment classes used in controlled environments like mines, but the deeper neural net required to enable usage on a dynamic construction site will be the next challenge.
Equipment must not only be equipped with electronic eyes and machine vision capabilities, but the artificial intelligence capabilities to recognize objects, humans, obstructions, hazards and other critical elements in their surroundings to enable them to function accordingly. Research into neural networks in construction suggest acquiring the large amount of data from video footage on construction sites, teaching a machine is a daunting task, and training a network using scale models of equipment and other objects may be useful. Initial research in this area though has focused on wheel loaders, which must be able to recognize materials and dump trucks the material is to be loaded on.
A collaboration between Trimble and Boston Dynamics, Spot navigates construction sites to collect photogrammetry images, but follows a defined route in a repetitive fashion. It recognizes and avoids obstructions but autonomous heavy equipment will need a deep neural network to enable it to operate safely without a human operator.
The technology to create a neural network that enables autonomous construction equipment may be some time in coming—even the Spot quadrupedal robot that Trimble and Boston Dynamics are collaboratively equipping with scanning capabilities for data capture on construction sites must be walked through a site by a human to learn a defined route it will take as it discharges its duties. It can sense objects in its paths—including moving objects like a dump truck, and navigate its way around them. But the technology will not, according to sources within both companies who spoke to ForConstructionPros in early February, be immediately applicable to heavy earthmoving or compaction equipment used in production.
One way or the other, complete autonomous operation will require not only machine vision to collect information on the environment around a piece of equipment, but to recognize objects and act accordingly.
“Full autonomy will take time,” Clark said. “At Trimble, we plan to provide value along the way with operator assistance and safety.”