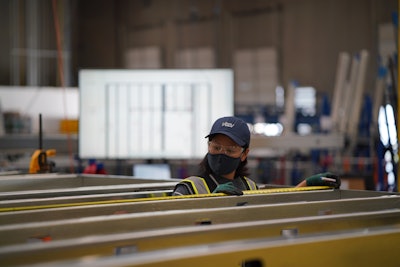
Construction contractors are right now widely adopting enterprise and production technologies that drive incremental productivity improvements and create digital workflows across the distributed team of owner, contractor, subcontractor and designer organizations that collaboratively deliver construction.
A $400 Million Series D funding round for San Francisco-based off-site home builder Veev may, however, provide a glimpse of a more radical transformation of the industry to come. Veev’s approach to the lifecycle of residential built assets drives risk and environmental impact out of construction, the years of operation and the end of a building’s productive life. The round announced today was led by Bond Capital, and should help Veev scale beyond its current geographic footprint to new geographic markets.
Funding Offsite Construction Growth
In a video interview with ForConstructionPros in the days before the announcement, Veev Co-Founder and CEO Amit Haller said the company planned to use the funds to expand beyond its current single factor in Northern California, adding another in Southern California and then, in the course of 2023, expand into Texas.
“The plans are for significant expansion,” Haller said. “There is a seven million home shortage. We are not concerned with competing with other off-site builders. We will all grow as our production levels increase. We are all just trying to solve this housing shortage problem. There is no single player that can move the needle on this problem alone.”
While growth potential in residential construction is significant, there is no technological barrier to Veev’s system entering light commercial or office construction.
“We are not limited to residential when it comes to our structural components,” Haller said. “We are already commercial-ready. The system as it is right now is just limited to up to eight stories or 85 feet due to fire ratings. We can build hotels, light commercial or office buildings. Our focus on residential is coming from our mission statement—this is a crisis we are facing when it comes to housing prices, high cost and a shortage. There is so much work for us for the rest of our life.”
The company plans to go to market through large-scale residential development firms into the foreseeable future—those building between 50 and 100 single family, condominium or apartment units, until they have the scale to interface directly with residential home buyers.
“The business model is that we will become a design-build general contractor off-site,” Haller said. “So we will take the plan for the project, convert it into the digital twin in our system—we have our own proprietary digital twin system. It will be our architect and structural engineers on record, which are employees of the company. And then we fabricate it, deliver it and install it and will also contract to maintain it down the road. So we will take on the entire end-to-end responsibility of the project.”
Veev’s current factory is between 50,000 and 100,000 square feet, and can produce about 800,000 square feet of living space per year, per Haller. He said the company’s plan is to expand by building additional facilities next to population centers with high demand, similar to Amazon’s approach to locating logistics and warehouse centers.
Veev's Northern California production facilityVeev
Greening the Built Asset Lifecycle
Apart from the prospect of high growth, Veev may be an attractive investors or funds focusing on the environment, sustainability and corporate governance (ESG). According to Reuters, $649 billion was invested in ESG-focused funds worldwide last year through November 30, up almost 20 percent over the 2020 and 227 percent over 2019.
The company relies on materials that are green in their energy performance, overall carbon footprint and end-of-life impacts. Projects are delivered with a smart home mechanical system and low voltage lighting, reducing lifecycle environmental impact. The company also recently announced a net-zero commitment to the World Green Building Council.
Veev’s material selection, which consists primarily engineered high performance surface (HPS) materials and steel, create 47 percent less CO2 emissions than traditional construction materials, according to Veev. These materials are configured into pre-built steel-reinforced panels to be assembled on site. This creates opportunities to reduce the environmental footprint of construction and the asset lifecycle drastically even compared to precast concrete, or other approaches to offsite construction.
“The areas we are borrowing our concepts from are semiconductors on the micro level and aerospace design on the macro level,” Haller said. “Our structural integrity is coming from light gauge steel, which is way stronger than wood, lighter and more sustainable. We are using 100 percent recycled steel. Our insulation is an advanced material from the foam industry. Spray foam is being used broadly in the industry and we all know its advantages, but each of our panels have foam built in and arrives insulated and waterproofed.”
But it is in the use of HPS cladding where Veev’s approach to materials is perhaps most revolutionary.
“In the interior, instead of using drywall, we are actually using HPS,” Haller said. “This is the same family of materials as solid surface materials like Corian. Many people don’t know this, but this material was invented not for countertops, but for surgical suites in order to build walls that are antibacterial and maintenance free forever.”
Veev relies on advanced etching and printing technology to transform this single material for multiple uses in the structure.
“One of the most important secrets of the company is that almost anything finishing, interior, exterior, kitchen cabinets, even bathroom flooring, is done with the same material,” Haller said. “The same HPS. This material always comes in white plates and will go through processing internally in our fab shop which will perform 3D texturing. We will convert it to look and feel like anything—the same material can look and feel like mahogany wood, ceramic tiles or exterior stucco or marble or anything you want it to be. We have created an infinite digital inventory, so our supply chain is a digital supply chain so you can have any look and feel you like.”
High performance surfaces are transformed into various textures and appearances.Veev
HPS material is etched in Veev's Northern California production facility.Veev
The reliance on a small number of materials enables Veev to control its supply chain, and its division of labor in the field also limits its exposure to labor shortages.
“Offsite construction is not enough,” Haller said. “Because with offsite, you have the same complicated supply chain as on-site, just in a different location. The same problems, the same 10,000 SKUs in the supply chain, the same framer, the same painter. Yes, it is a little bit more robotic, there is a little bit more automation and there is a better-controlled environment. There is some advantage to offsite, but it is not a game changer. To be a game changer, you need to think about new materials. And a digital twin is a must.”
The company has developed its own digital twin application that enables developers or home buyers to digitally walk through a project, visually approving the look and feel and layout. The digital twin then drives the fabrication process for panels to be assembled on-site. Panels arrive on site with all mechanicals and windows installed, drastically reducing the need for skilled tradespeople on the project site.
“Architects and engineers today draw plans for construction people,” Haller said. “We need to start creating plans for machines—for manufacturing people, not for construction people. That is our problem. Construction people are at a shortage. Creating more plans for construction people that don’t exist is not going to solve the problem.”
The digital twin and tight control over construction tolerances and materials used in construction will also enable streamlined maintenance, replacement and remodeling.
“See that cabinet behind you?” Haller asked during the video interview. “What if you want to replace that? You need to bring in a contractor who will measure the doors, determine what hinge is used, specify cost to repair or replace it with what you want. Maybe the measurements are not accurate, and they have to start again. With our homes, we know the exact dimensions, have the part number for the hinge and can deliver whatever you want with no guesswork.”
BOTTOM LINE: Haller says Veev's technology will not be licensable by other contractors in the foreseeable future, but in time, other residential and light commercial contractors could take advantage of their integrated supply chain and advanced technologies. But even as construction enterprise resource planning (ERP), estimating software, field productivity technology and equipment automation are digitizing the cow paths contractors have traditionally follow, Veev's vision of the future is something to keep in mind as a potential ultimate destination for the industry.