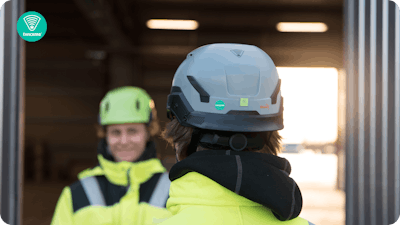
Constructions workers missed approximately 24.2 million working hours due to injury or illness in 2022.
The case for using wearable technology on construction jobsites has never been more compelling. The latest data from the Bureau of Labor Statistics (BLS) reports that 1,069 construction fatalities occurred in 2022, a 7.7% increase over the previous year, with the leading cause of death attributable to falls. OSHA reported a total of 169,200 construction industry injuries in 2021, adding that about 40% of those injuries resulted in missed workdays.
What was the cost? According to the Midwest Economic Policy Institute, in human terms, $5 billion was lost in, production, family income, and pain and suffering. According to Procore, for businesses experienced $7.87 billion in direct workers’ compensation costs.
These are only numbers. But how many construction pros do you personally know who have been injured because of jobsite accidents? Can you afford to add one more name to that list?
This is where wearable technology gets personal. It can make a real difference.
What Is Wearable Technology?
Wearable technology consists of digital devices designed to be worn on the body for the purpose of detecting, recording, transmitting or analyzing information. It appears on construction sites in the form of:
- Smart helmets
- Boots
- Belts
- Gloves
- Glasses
- Vests
- Pendants
- Exoskeletons, worn to enhance human motions
The technology often incorporates microprocessors, compact batteries, WiFi, sensors, neural interfaces and integrated cameras. It also includes Internet of Things technology, tied to cloud software, smartphone apps, or other direct or indirect computing networks where information is stored or processed.
Wearable tech can be used to track bodily movements, read geolocations, monitor physical activities, measure vital information, and determine proper use of equipment based on real-time data relayed from linked devices, such as bulldozers or forklifts.
And this is only the tip of the iceberg. Rapid advances in wearable tech are opening new vistas of applications that was not thought possible just 10 years ago.
New Possibilities Through Research
Today, researchers are exploring new possibilities for wearables in the construction industry. The Stanford Wearable Electronics Initiative (eWEAR) is a multidisciplinary program dedicated to bringing together experts in materials, electronics, data, systems and medical science to assist the industry in keeping workers safe and productivity high through smart technology.
“Industry and academia have an implicit partnership in the development of technology,” said Angela McIntyre, executive director of the eWEAR Initiative. “Collaboration between companies and universities benefit both, enabling a broad range of innovations crucial to the future of wearables.”
Some leading-edge developments currently on the table at eWEAR include the tech below.
AR Glasses
Glasses that project digital content on the inside of wearable lenses to aid in the remote processing of field applications. Augmented reality (AR) helps workers visualize content that is invisible to the naked eye. It’s useful in applications such as servicing underground utilities, fiber cables, gas or water pipelines, or underground sewage systems.
For instance, a remote expert at headquarters or another job site can see on a computer or tablet what a site worker is viewing in the field. From this view, the expert can share mark-ups or other imagery to the worker to assist in completing repairs or complicated procedures.
Such immersive troubleshooting, incorporating spatial computing and remote connectivity, can help speed time-to-resolution, eliminate travel time, boost efficiency, and help solve even complex issues through interactive guidance.
VR Headsets
The Genie team shared the VR experience at their booth during the American Rental Association conference.Genie
VR headsets have been used to pitch design ideas to clients, increase stakeholder collaboration, or provide immersive safety training. They can allow a client to experience a product before it is finished. Or help to unify a team’s collective vision of a prospective project. Perhaps most important, it can help employees train safely for high-risk activities, such as scaffolding installation or hazardous electrical work.
Motion Sensors
Sensors worn on the body to track movement and physical activity. Motion sensors collect kinetic information through wireless components, usually woven into a garment or wearable device. Such sensors can be used with movement analytics software to detect unergonomic movement, or repetitive movement that can lead to injuries or fatigue. The analytics software then compares the worker’s motion against that of a worker doing the task using the most ergonomic technique.
A smartphone app can coach the worker on what motions to improve, or even alert the worker to too many correctly performed repetitive movements that, when performed over time, can lead to an injury or fatigue.
Exoskeletons
Wearable exoskeletons are robot-like machines worn to augment human strength and performance. Active exoskeletons us actuators to impact human movements; passive exoskeletons use resistance elements, such as springs or cords, to support the wearer’s motor activities.
Exoskeletons reduce injuries and stress to the back, arms, or legs. They can effectively assist workers in carrying or lifting heavy items, providing musculoskeletal reinforcement of correct ergonomic movements.
For instance, workers wearing active exoskeleton devices may be able to lift heavy tools or materials in tight spaces, avoiding awkward positions caused by excessive loads placed on the body. Lifting belts, or back belts, represent passive forms of the same technology.
Safety Vests & Gas Sensors
Safety vests go well beyond offering wearers fluorescent, reflective, high-visibility in low-light or high-traffic conditions; they can be outfitted with various sensors to warn the wearer of nearby hazards that can prevent injuries and accidents.
Gas sensors can warn the wearer of high carbon monoxide, hydrogen sulfide, or low oxygen levels, for instance. Haptic (vibrating) alerts can be particularly helpful in areas where noise from machinery or trucks might drown out audible alerts. Such smart clothing can also be equipped to send location-specific text messages in the event of an accident. Or automatically detect if the vest is left motionless, either because it was removed or the wearer is immobilized.
Personal Safety at Work
Integrated digital chips in helmets or hardhats work much like a hard drive storing information. You simply hold your phone next to the device, and the app reads the data, identifying the permitted user.twICEme
TwICEme Technology, a manufacturer of wearable technology for the construction industry, combines wearable items, such as construction helmets, harnesses, vests, and other equipment, with digital applications stored on a users’ smartphone to protect them before and after an incident occurs.
“Before an incident, we support prevention by offering users situational awareness and updates on the health of their equipment,” said Christian Connolly, TwICEme CEO. “After an incident, we support recovery by helping the helpers access essential information that saves time and helps save lives.”
TwICEme does this by integrating digital chips into wearable items. The chips work much like a hard drive storing information. No data is relayed through the chips themselves. There’s no charging involved. You simply hold your phone next to the device and the app reads the data, identifying the permitted user.
When the user puts on the equipment, the chip reads the information (using near-field data technology) and saves it for future use.twICEme
Should an accident occur, each equipped garment displays a TwICEme symbol that, when tapped, automatically reads the user’s data and relays it with the exact location of the wearer, to nearby responders. In this way, anyone can assist a fallen comrade and relay vital information without having to access a phone or communicate with the affected person.
The chips are also programmed to report equipment usage and maintenance data, ensuring that no one puts on a damaged or defective article before going to the jobsite. In this way, an inspector can simply scan the equipment and view a report on the item’s current shelf life and state of repair. They can also detect who wore the item last and also verify ahead of an assignment whether the worker is certified to perform a specific job.
Should an accident occur, each equipped garment displays a TwICEme symbol that, when tapped, automatically reads the user’s data and relays it with the exact location of the wearer, to nearby responders.twICEme
“So many systems are clunky or cumbersome, disinclining users to adopt the technology, which defeats the purpose,” he said. “TwICEme takes less than three minutes to set up, and you’re good to go. That can be a game-changer for companies looking to improve safety on the jobsite.”
Turning High-Risk Training into a Game
So much of making the construction industry safer comes down to preparing workers for safe practice before they operate on a hazardous site. Training, especially for jobs that present high-risk, such as operating aerial equipment or working at heights, can be made safer with VR training.
Genie, a manufacturer of mobile aerial and material lifts and handlers, including man-lifts, articulated booms, and telehandlers, has invested in a VR training platform to prepare people for the experience of operating their equipment—without physically operating the equipment. The training focuses on four activities involved in operating Genie’s mobile elevated work platform.
The VR training experience replicates actual machine sounds, timing and other specs based on Genie’s engineering documentation.Genie
According to Owyen, the VR training experience replicates actual machine sounds, timing and other specs based on Genie’s engineering documentation. A specially programmed headset allows operators in training to control a Genie Z-45E articulated boom lift in four training scenarios.
The first is a basic introduction to the lift’s controls. The second is a ghost arena where the operator is challenged to precisely position the virtual machine to match a given ghosted outline. The third, a safety gauntlet, challenges the trainee to navigate a virtual jobsite, avoiding real-life hazards to collect trophies. Last, a steel erector simulator tests the trainee’s ability to position the boom and weld steel beams onto a structure.
“While VR training feels very realistic, it simply can’t replace that real-world experience,” said Owyen. “But allowing someone to practice what they’ve learned in a classroom, before going up in a lift, not only makes what they’ve learned more memorable, it enhances safety.”In a ghost arena, the operator is challenged to precisely position the virtual machine to match a given ghosted outline. In another scenario, a safety gauntlet challenges the trainee to navigate a virtual jobsite.Genie
The Pros Outweigh the Cons
Like any emerging technology, wearable tech may cause some new employees to pause before fully accepting the idea of equipping a workforce with gear that monitors, measures, and communicates situational data with and to the user.
The costs involved include those associated with:
- The devices
- Software (if any)
- Training
- General equipment upkeep
Workers may not readily accept that the wearables are useful. They may be concerned about the data being used to rate job performance. And there’s always the uphill battle that the status quo is good enough. But is it?
Wearable devices, when used correctly, can bring down costs, by eliminating lost days on the job, workers’ comp expenses, and lawsuits or non-compliance fines for perceived or actual negligence. Equipment monitored through wearable tech gets cared for properly, lowering maintenance costs and extending equipment life.
In addition, companies that use wearable tech have broadly reported increased productivity and efficiency, as workers understand that their work is being monitored. As the saying goes, “what gets measured gets done.”
In an industry that is struggling to recruit new blood, wearable technology can also attract talent, steering the best and the brightest candidates toward companies that use the latest and greatest technology. Indeed, the improved jobsite safety afforded by wearables can be used as a hiring advantage. The extended workforce family appreciates the fact that people on the jobsite are valued and protected, a fact that translates to improved employee loyalty and enhanced enthusiasm.
Companies that place a premium on worker safety hold a competitive edge against those that don’t, which collaterally contributes to respect for the brand. Companies that demonstrate smart operations with wearables can position the business in competitive sales scenarios where customers take note of corporate responsibility and seek to associate with contractors who remain on the cutting edge.
Wear It Proudly
“While a U.S. Chamber of Commerce report found that only 6% of contractors used construction wearables onsite in 2018, some 83% of contractors believe that construction wearables would improve on-site safety,” said a 2021 story published by ForConstructionPros.com.
Since the 2021 story, the barriers of entry have diminished. The technology has improved, increasing the capabilities, while lowering the cost. More options have also become available, as competition in the field expands and research continues.
“There’s no excuse not to start using the technology, even if it’s in small, experimental increments,” said Connolly. “The best advice is to go simple. Try it on a pilot project in a limited application, without getting too complicated, and see what happens.”
Reduced workplace accidents, improved equipment use and greater worker productivity are often the result of implementing wearable technology. Who can argue? Wearable tech has come of age. It’s time for the construction industry to suit up and wear it proudly.