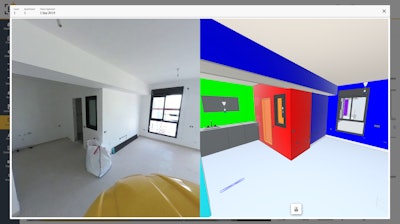
The construction industry's productivity problems are well known.
With the industry using outdated methods and the low rate of digitization in the field, low productivity is perhaps to be expected. What can be done to accelerate the change and bring the necessary outputs that will raise standards and value in the sector?
Increasing and maintaining efficiency and productivity are key to making this change, but to do that, contractors need accurate data to tell them where improvements can be made and direct them to act accordingly.
With its roots in manufacturing, the control room concept provides an answer, with an approach based around the automation of processes, continuous tracking and measurement of project progress.
Mission Control
The idea of ‘mission control’ is usually associated with agencies such as NASA. It’s the center of a process involving many people with one ultimate goal, or mission, all brought together to fulfil their own individual tasks to get the job done. All parties depend on each other’s work and rely on having up-to-date, accurate and impartial data that can give a real-time view of progress and milestones, as well as being an indicator of any issues.
But the concept rings true for construction projects, too, and the laser focus on data management and constant tracking of each element can be the difference between a successful outcome or a failure to meet objectives.
Project Visibility to Avoid Errors and Delays
One of the main challenges on a construction project includes accessing the data from the site and being able to structure it in such a way to get meaningful insights that can be analyzed and divided into action items accordingly.
The control room gives a bird’s-eye view of the project (or projects) by providing all mission critical information to the relevant stakeholders when they need it, allowing them to make decisions based on what is actually happening, instead of what they think is happening. This could be an early warning of a substantial drop in pace from a particular trade that will impact the construction delivery path. Or, it could be identification of an error that, if not resolved immediately, will delay the work of the next subcontractor due on site, creating a domino effect of delays.
Through the power of technology, a new approach is available to project teams that would previously have had to rely on inconsistent and patchy data to keep things moving and determine progress through only subjective information. Now, the project is laid out in front of everyone who needs to input and contribute. The control room provides just that, total control.
Buildots software uses algorithms to control job site productivity.Buildots
BIM Allows Project Control
One big factor in the journey to realizing this shift to a truly digitized construction sector and being able to fully embrace the new technology available to us is the adoption of Building Information Modelling (BIM).
Mandated in the United Kingdom since 2016, tentative steps are already underway to introduce the same in the United States. BIM is the key to enabling control room-type management of projects, thanks to the provision of a 3D model and schedule to track and compare against the collected, as-built data.
The application of BIM methodology and the mapping of all construction processes and workflows means the foundations are in place to provide the construction manager with invaluable project data. It’s reasonable to suggest that the fusion of new technology with BIM-enabled projects will widen the gap between companies that have adopted change, versus those that are staying outside the digital world.
The level of data insight described above is a game-changer for construction management and the level of granularity and automation is reminiscent of manufacturing environments, where process controls are highly developed. This is the benchmark that construction should strive to attain.
In fact, a global McKinsey study revealed that the cost of this lack of transparency and visibility of quality data results in an estimated 30% loss in industry productivity. In turn, the benefits for contractors utilizing technology for process management are huge, resulting in major increases in efficiency and productivity. They include:
- Automated progress tracking: Continuous tracking means site labor can be allocated and focused to the actual needs of the project.
- Early warnings: Issues spotted can be rectified immediately, instead of snowballing to major problems later, requiring costly rework.
- A single source of truth: Data analysis is based on objective, accurate information, which can be supported with evidence.
The control room is elevated completely when you go beyond the project level and instead apply this across a whole enterprise.
Imagine the insight that can be collected when comparing multiple projects; the ability to spot trends in processes and subcontractor productivity. For the first time, data becomes the most powerful tool on the construction site. The ability to see the whole picture also creates insight on performance, meaning the lessons from successful projects can be identified and carried forward as a template for future success.
Working smarter
Of course, the control room is not just a concept, physical control rooms exist across many industries, but understanding their purpose and benefit as we apply the same methodology to the software world makes a compelling case for their use in construction.
Ongoing innovation and organizations already adopting this approach mean the construction control room will maintain an essential place as part of the project management function, with highly efficient and more predictable outcomes.
Buildots AI uses a simple hardhat mounted camera and computer vision algorithms to track job site activities.Buildots
Bio
Roy Danon is CEO and founder of Buildots, a construction tech startup that uses artificial intelligence, digital twin technology and wearable hardware to create project workflows to improve processes, minimize delays and save money.