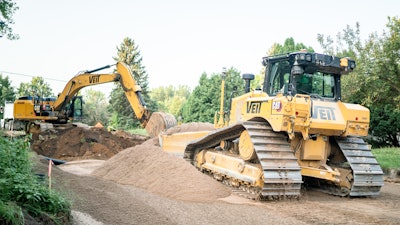
Britton Lawson, director of construction technology at Veit, credits much of the company’s success to its technology culture. He noted, “It’s a mentality that’s been fostered over generations, and an attitude that helps us continually improve performance, quality and safety across every job.”With real-time production data on site, operators and laborers are able to work with foremen to help make more informed and productive decisions.Trimble
Veit was one of the first adopters in the Upper Midwest of the traxcavator (a hydraulic tractor/excavator), hydraulic rippers, wheeled and articulated loaders and, more recently, high-reach excavators and downhole hammer drills.
Veit talent and innovation is delivering some of the industry’s most complex projects today. With more than 30 3D machine control systems used on dozers, excavators, motor graders and skid steers; 30 rovers and total stations; and 50 base stations, the company maintains one of the largest technology-enabled fleets in the Upper Midwest.
“The real challenge for us is logistics,” said Lawson. “We have many projects ongoing at one time in multiple states, so equipment has to be moved on a daily basis to facilitate jobs. When it comes to technology, workflow and process improvement, our focus is assured connectivity.”
Digital opportunities
At any one time, Veit might have 100 to 120 commercial, industrial, energy and infrastructure projects in process.
“During peak construction times, we have many operators and machines on various projects in many states. We need to be able to react quickly in response to issues that arise in this fast-paced environment,” said Lawson. “Speedy file transfer is critical.”
In the past, Veit has relied on familiar data transfer methods such as email and VPNs – both of which require time, money and expertise. Today, all of its GPS-guided machine control systems, base stations, rovers and total stations are connected to the cloud, enabling easy transfer of 3D project files to field crews.
“One of our biggest business advantages is our ability to move information quickly, accurately and efficiently to our people and equipment,” said Lawson. “We can push designs out to any machine on any jobsite anywhere in the world, which gives our crews the most current information. If our crews have questions about a culvert, fence line or some other project detail, we can add to model and sync with ease. No more laptops or thumb drives.”
Veit’s Construction Technology team uses Trimble Business Center to create and modify models to share with field crews, and WorksManager to wirelessly transfer data such as 3D constructable models to the sites.Trimble
In the last year, the company has also applied Trimble WorksOS Software to connect design data from the office with machine control data for real-time progress and productivity updates such as cut, fill, volume and compaction data.
Lawson said, “We didn’t realize or think about the value of real-time data when we invested in digital connectivity – but it’s a huge advantage.”
Real-time results
Veit crews first tested WorksOS on a very large distribution warehouse project in summer 2020.
“This was a huge job that required us to move 20,000 to 30,000 yards a day totaling about 600,000 yards over the course of about five weeks. We had multiple scrapers, dozers, excavators, trucks and other equipment on the job,” said Lawson. “By connecting to our machine control data, we were able to verify quantities and track our progress per the schedule. Better yet, we did the entire job without one stake in the ground.”
Trimble
“With WorksOS connected to Trimble Earthworks, we were able to quantify how many footings and how many lineal feet of material were completed each day,” he said. “Now we can benchmark our production capabilities for future estimating and bidding.”
With WorksOS, Veit teams are able to get near real-time machine mapping data. Lawson continued, “We can see how much quantity is moved in a day at a jobsite, compare load counts and production quantities, even on a dozer. We’ve never had production data for dozer operations, just best guesses. But, with WorksOS, quantities of material pushed and hours are automatically tallied, which helps us bid future projects more accurately.”
The company’s technology-centric mentality is also opening the door to innovative thinking on the job.
Collective decision-making on site
“One of the intangible benefits that we’ve realized from our investment in machine control and other systems is the way it empowers our operators. We’ve found that they are more immersed in the process and subsequent decision making, which results in a better-quality job,” said Lawson.
He points to an increasingly common jobsite occurrence related to moving dirt. Typically, a foreman dictates how dirt is moved in a cut/fill situation. With real-time data, operators and laborers are able to work with foreman to help make more informed decisions. It’s a much more collective decision-making workflow.
“Because the data about materials and designs are readily available on the job, our crews are coming up with ideas to improve common practices such as the digging of building or bridge footings to improve safety, accuracy or speed,” he said.
Recognizing this increased collaborative process, the Veit Construction Technology group is hosting GPS internal training sessions to further explore features and functionality of the systems for their field crews.
Virtual diagnostics
As Veit’s fleet has grown, so have the number of support questions.
“We don’t expect our operators to be experts on software features and functionality after one training session,” said Lawson. “Our goal in training is more to introduce them to capabilities. Then, since a majority of operators are hands-on learners, when they have a chance to put a feature to work, they can call, and we can guide them through the process.”
A key component of that on-the-job support is Trimble Remote Assistant, a real-time technical support application for field crew personnel and machine operators, which is particularly beneficial to new employees.
“Many times, during the height of our construction season, new operators will get thrown into a machine with very little training,” said Lawson. “With Remote Assistant, we can walk them through the process as if we were in the cab with them – they’re up and running very quickly.”
Remote Assistant has also become invaluable to Lawson in support of machine diagnostics.
“Instead of driving out to a jobsite, we can log into any of our operator’s machines and diagnose a problem – no more waiting for a technician to drive to the jobsite,” said Lawson. “In many cases, they can return to work while we work an issue. It’s a huge advantage because we’re not stopping the operator, foreman or the overall production. Bottom line: improved uptime.”
Lawson estimates that the company has virtually streamlined the process and reduced technical support cost by almost 200% since implementing Remote Assistant.
Unexpected opportunities
Veit’s legacy of technology adoption has been integral to the company’s growth over the years, according to Lawson, who added that support from executive leadership is second to none.
“Achieving the value of technology investment and application is not possible by a single person – it’s a company commitment that requires complete buy-in from management,” he said.
He also points to the importance of industry relationships to stay current with industry advancements. Sitech Northland is Veit’s anchor for all things related to jobsite technology.
“Our relationship with them has really grown over the years as we’ve expanded our fleet, and particularly as we’ve focused on new capabilities and connectivity,” he said. “They’re often the ones to introduce us to new technology that can help improve workflows, safety or productivity. They have been a huge partner and ally throughout this journey.”
Lawson emphasizes the value of connections – both with people and solutions – as key contributors to the company’s success. “Our time is valuable, our crew’s time is valuable and our equipment is a significant investment,” he said. “The faster we can provide data to our teams, the better off we’ll all be. The technology – machine control, GPS, underwater sensors, software and more, are all great, but the biggest value to us all is when everything is connected, which has opened the door for opportunities that we never knew existed.”Trimble