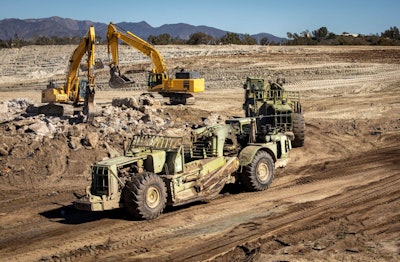
Content sponsored by: Vizzn
Have you ever rented a machine just to see it parked? Has your mechanic ever repaired a machine that wasn’t needed in the foreseeable future? Or have you ever bought a new piece of equipment and then realized you could have made do without it or procured a short-term rental instead?
Buying, repairing, renting, and selling equipment are decisions we make every day in construction companies. These decisions are big dollar decisions and over the course of a year total 10% of our annual revenues. This means, if your construction company has $50M in revenue, you are probably spending $5M buying, repairing, and renting equipment. This capital spending is too significant to simply fly by the seat of our pants. However, to make the right decision every time, we would need a clear and accurate picture of our future equipment requirements. Such information is costly and time consuming to compile, and would change daily, so flying by the seat of our pants becomes the norm.
As a simple case in point, contractors should never fix machines that are not needed in the foreseeable future. Sounds like good logic, right? Well, we all do it and the reason we all do it is because we do not accurately know what equipment we need in the foreseeable future. Hence, the mechanic’s job is to fix stuff that breaks and that’s that. Unfortunately, the inevitable result is that we end up making unnecessary repairs or spending money sooner than we need to.
Fortunately, this information deficit now has a solution thanks to a market disrupting company called Vizzn, Inc and their namesake product, Vizzn Software. Vizzn has created Job Scheduler software that allows for embedding equipment schedules. The construction management software then compiles all these embedded equipment schedules together to create a holistic companywide equipment schedule. Your construction management profile will show you exactly how many pieces of each type of equipment are required every day for the foreseeable future.
As the job schedules change, the equipment schedule changes with it, keeping the picture of your equipment demands up to date and relevant.
Being able to see equipment demands for each type of equipment well in advance helps companies make better decisions around renting vs. buying equipment, selling vs. repairing equipment, and choosing rental terms for hourly vs. monthly. If we are spending $5 million a year on these capital items, making these decisions 10% better would be $500,000 extra in our pockets. This same schedule also helps the estimating teams pursue projects that fit the available fleet.
Better decisions come from having better information! Check out the Vizzn Equipment Scheduler at https://www.vizznsoftware.com/project-scheduler-embedded-equipment.