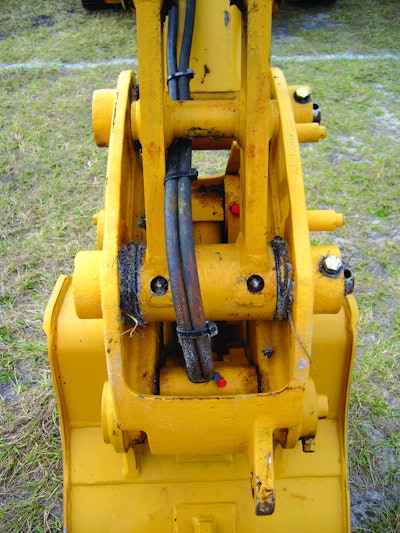
Excavator quick couplers come in many variations with different locking mechanism designs and features. They range from the most basic mechanical designs to sophisticated multi pin-grabber models that automate the entire attachment process and allow quick changes on the fly.
"When you can change attachments on the fly, your excavator can get much more work done on the jobsite," says Cameron Noble, Norco Attachments. It converts your excavator into a tool carrier. "With a quick coupler, you can grab the right tool and be more efficient in your operation."
However, it's important to understand how a quick coupler impacts overall machine performance. It can change the intended geometry of the excavator attachment, especially if the center-to-center pin dimension is significantly different than that of the OEM design.
Tip radius and breakout force
In almost every case, a quick coupler adds length to the stick. "It will move your bucket or attachment out farther," says Ron Peters, product manager, CEAttachments. This will impact the tip radius of the bucket. "Depending upon the size of the machine, it will move it out anywhere from 3 to 6 in."
Any time you lengthen tip radius, you lose breakout force. The trade-off is you gain flexibility. "You have to make a sacrifice when you install a quick coupler," Noble admits. "It is a sacrifice for the efficiency of being able to change attachments. The reduced breakout force or increased tip radius is minimal compared to the big picture of what you can accomplish."
According to Jamie Adams, JRB sales and product manager, Paladin Construction Group, "Increasing the stick length and tip radius of a given bucket will generally reduce breakout force by approximately 3% to 5%. To address this, some excavator end users and/or distributors have intentionally configured excavators with shorter sticks when installing couplers to limit the loss in breakout force."
A coupler's design can help to minimize losses, as well. "You have vertical and horizontal offsets," says Noble. "A lot of the geometry we put in with the horizontal offset helps to reverse the effect of the vertical offset. So that helps you gain back that breakout force."
Bucket design is also a factor. "Bucket selection can and will have an impact on the assembled tip radius," says Adams. This tip radius change can be minimized when using a dedicated coupler and bucket design.
The load-sensing hydraulic systems of the new excavators can further compensate for any reduction in breakout force. "You really couldn't tell from the seat unless you absolutely had the machine maxxed out," says Noble. "Then, there probably would be a noticeable difference vs. the bucket being pinned to the stick."
Most contractors tend to accept a loss in breakout force due to the advantages quick couplers provide. "They do not measure productivity as mere payload and cycle time, but more in terms of maximizing equipment utilization and the ability to do more with less equipment," says Adams.
"Many times, contractors measure machine and coupler value in terms of lower costs for units of work done," he continues. "For example, if the contractor is laying pipe, his concern is how many total feet of pipe he laid that day because he did multiple jobs with one machine, instead of how much dirt did we pick up with one bucket."
In some cases, the coupler actually provides an advantage when digging. "For digging applications, a machine's digging characteristics are equally influenced by configuration, material conditions/types and operator techniques," Adams explains. "Couplers that feature minimal offset tend to be productive in high digging applications. For heavy material, a closer tip radius will dig better."
In general, it's best to keep the stick length as close to the OEM design as possible. "We have engineered our specific design to be the lowest possible profile to reduce that tip radius," says Noble. "Anytime you can reduce the tip radius, it is a good idea to keep it as low as possible."
Adams agrees, noting, "If you want the bucket/attachment to perform as it was originally was meant to, the height of the coupler must be minimized. For this reason, OEMs and bucket manufacturers have started designing based around coupler specifications."
Addressing variations in pin spreads
Past problems with excavator bucket ear clearance problems are no longer an issue. "Today, quick couplers, especially pin grabbers, are so common that most of the bucket manufacturers allow enough clearance with the ears so you don't have any interference," says Noble.
Interchangeability is also no longer an issue. "Nowadays, they are all interchangeable because the market has developed toward the pin grabber style of bucket," says Noble. "Most of the time, we don't run into many issues. As long as it is a bucket that will pin on to the carrier machines, the couplers will pick them up."
That said, Adams points out, "There are no set standards for pin spreads on buckets/attachments, so OEMs build their buckets/attachments with a pin spread of their choosing."
Traditional pin-grabber couplers are made to match the OEM pin spacing and diameter for a specific brand. As a result, pin spacing and diameters change from brand to brand. "You can't pick up a bucket that was built for a different brand," says Peters.
"Pin-spacing couplers only pick up one particular pin diameter and pin spread. Generally, each manufacturer designs these couplers to work with the range they set for their attachments," says Adams. In such cases, you must choose a coupler/attachment combo that best fits the applications. "For example, a wider pin spread will limit the amount of rotation, while a narrower pin spread will increase the amount of rotation at the coupler/attachment."
There are options, however, for mixed fleets. "For example, the JRB PowerLoc has an extra set of pin holes to spread it wider and allow the operator to get more power when needed," says Adams. "In addition, multi pin-grabber couplers provide more flexibility across the several pin spreads associated with different OEMs within an excavator weight class."
A growing number of couplers promote the ability to interface with attachments from multiple OEMs. "This is the main concept of a multi pin-grabber coupler," says Adams. "[These] couplers often allow contractors to use the same coupler and attachments, for example, when they switch to or buy a new excavator."
Options depend on size
The size of the excavator has an influence on quick-coupler design.
For example, all of CEAttachments' quick couplers and attachments for excavators are for compacts or minis. "They go up to about a 12,000-lb. excavator," Peters says. "We have two different styles of quick couplers. The most popular one is our spring-loaded (pin grabber) quick coupler. Then we have a hydraulic quick coupler for mid and larger compact excavators."
These couplers are more compact. "Our quick couplers weigh anywhere from around 75 to 200 lbs. Since compact and mini excavators of this size are generally not used for lifting, the reduced lifting capacity is usually not an issue," says Peters.
Most users of this size of machine lean toward the pin grabber-type couplers. "You don't get a lot of time savings going to the hydraulic coupler. You still have to put a locking pin in both of them," Peters points out. "The big thing is the cost. The spring-loaded quick couplers range anywhere from $225 to $2,500 vs. a hydraulic coupler that ranges from $5,700 to $6,700."
That said, the hydraulic quick couplers do offer advantages for rental fleets and customers who frequently change attachments. "You don't have to get off [the excavator] to hit a release bar to release the attachment manually," says Peters. "It simplifies the attachment process, even though you still need to manually remove and install the safety pin."
In-cab attachment changes
The goal with any quick coupler is to maximize the carrier's versatility. "Hydraulic multi pin-grabber-style couplers with variable pin spread and pin diameter characteristics are generally the preferred option for contractors making multiple attachment changes throughout a work day," says Adams. "They allow the operator to change attachments safely without leaving the cab, so no ground support is needed, maximizing productivity."
Noble adds, "A multi pin-grabber model allows a machine to pick up another carrier's attachments. It keeps it versatile for that guy with the mixed fleet if you can interchange attachments. If you have eight buckets you can use with another machine, too, it saves dollars and cents. The initial investment in a quick coupler may help save money down the road on attachments, especially specialty attachments — compaction wheels, rippers and items you may not use every day."
The Liebherr LIKUFIX is a hydraulic coupler that takes versatility one step further by combining the coupler with an automatic hydraulic coupling system. Mechanical and hydraulic attachments can be safely changed from the cab. "The operator in the cab can stay where it is cool or warm, depending upon weather conditions," says Jeff Powell, general product manager, earthmoving equipment, Liebherr. "He never has to leave the cab."
Hydraulic connections are made automatically. "You have the safety of not needing a second person standing outside hooking up hoses," says Powell. "The contamination risk is minimal and oil spill onto the ground is virtually zero. Now an operator can couple and uncouple between attachments to the true attachment needs. Instead of trying to use a bucket to break up concrete, he can drop it off, pick up a hammer, break it up in a few minutes and hook the bucket back up in 15 seconds or less."
Impact on lifting performance
Quick couplers will add weight to the stick. "On a 200-size machine it will weigh around 600 or 700 lbs.," says Noble. "On a 300-size machine, it's a little more. But relatively speaking, it is a very small number based on the lift capacity of the machine."
In lifting applications, a lighter stick and arm is always better. "You will reduce your capacity with the machine and attachment by the weight of the coupler, plus the slight geometric impact because you have extended the length away from the excavator," says Adams.
"However, when lifting objects such as pipes," he continues, "most contractors remove the bucket/attachment before attempting a lift and use the lift eye incorporated into the coupler design. Since most attachments weigh more than the coupler, the lifting characteristics of the excavator is actually improved dramatically."
Of course, there are weight differences between various types of couplers. "The weight difference is driven mostly by the physical size of the coupler and the material from which it is made (fabricated vs. cast)," says Adams. "Multi pin-grabber couplers tend to be heavier and more robust since they are designed to pick up attachments with varying pin spreads and some with multiple pin diameters. Couplers that are dedicated to a single pin spread and/or pin diameter tend to be slightly lighter and smaller in physical size. Dedicated couplers can (though not always) be lighter yet."