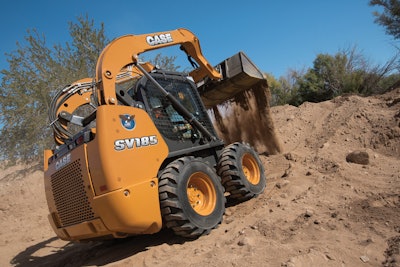
Due to their compact nature, range of operating capacities and application versatility, skid-steer loaders pose a unique challenge when it comes to meeting Tier 4 Final emissions compliance. No one-size-fits-all solution exists. We are witnessing a variety of solutions — even within a given manufacturer’s line — as manufacturers select solutions they feel are in the best interest of their customers.
Emissions compliance has led to some of the most extensive changes to skid-steer loaders over the past decade. “Tier 4 Final compliance has been a major factor in the loader market in 2013,” says Jamie Wright, product manager, Terex Construction Americas. “One of the largest challenges manufacturers have with Tier 4 compliance is finding an engine manufacturer partner. Manufacturers need to pick a supplier that has a broad range of engine options ready for Tier 4 and that is able to engineer the engine options to fit into the loader’s engine compartment.”
Space is at a premium. “Tier 4 Final engines with diesel particulate filters (DPFs) require a lot more space because there needs to be room for the DPF to fit inside the engine compartment, as well as other added components that need to be incorporated into a loader to support Tier 4 Final regulations,” notes Wright.
Additional cooling capacity is also required. “Tier 4 engines require loaders to be engineered with larger coolers to disperse the heat produced by these engines,” says Wright.
When Terex developed its solution, it considered which approach best aligned with its customers’ needs and the way they used the machines. “The Tier 4 Final solution for Terex compact equipment came down to simple operation, low cost and no additives,” says Wright. “Terex has incorporated an EGR (exhaust gas recirculation) engine with a DPF exhaust system in our line of skid-steer loaders. EGR technology is well suited for lower horsepower engines operating in high duty applications.”
John Deere chose a similar approach. “Skid steers and compact track loaders less than 75 hp will incorporate EGR, a solution you are accustomed to in John Deere equipment, combined with exhaust aftertreatment,” says Sam Norwood, commercial work site product sales manager, John Deere Construction & Forestry. “Exhaust aftertreatment includes a DPF and diesel oxidation catalyst (DOC).
“Like our larger construction machines, cleaning to oxidize soot in the DPF takes place automatically and has no impact to machine operation under most operating conditions,” he adds. “This is a field-proven solution that has been used by John Deere in off-road applications for machines over 100 hp for several years. Machines greater than 75 hp will feature selective catalytic reduction (SCR).” NOx regulations for engines greater than 75 hp are more drastic than for those under 75 hp.
Understand Regen Cycles
Engines that use a DPF go through regeneration cycles to burn off the collected soot. “Heat in the exhaust system is required for regeneration to burn off the particulate matter trapped in the DPF,” says Wright. “All EGR engines with DPF exhaust systems capture soot until they fill up and create too much backpressure. At that point, the DPFs use one of two approaches to regenerate (clean) themselves: active or passive.”
Passive regeneration cycles occur continually when the exhaust temperatures are hot enough, and are transparent to the operator. No intervention or action is required. “During normal operation, the exhaust heat will naturally clean the [soot] buildup in the exhaust filter,” says Norwood.
“For machines operating in a high duty cycle environment, like skid-steer loaders, enough heat is generated to clear the DPF through passive regeneration, which does not impact machine operation,” says Wright.
During an active regeneration, diesel fuel is actually injected into the exhaust stream. It elevates the temperature in the DPF to burn off the soot. “Active regeneration cycles give indicators to the operator through an operator interface to make the driver aware that the unit is about to undergo [regeneration],” says Wright. “At this time, the operator should inspect the DPF area for contaminants before the active regeneration occurs.”
John Deere uses an active regeneration (auto cleaning) process on its skid steers. “With auto cleaning, exhaust filter cleaning is automatically performed as needed, with no interaction from the operator,” says Norwood. “An exhaust filter cleaning indicator will illuminate on the monitor when the system is actively performing an exhaust filter auto cleaning. The machine can be operated as normal during this process. When the exhaust filter auto cleaning process has completed its cycle, the cleaning indicator will automatically turn off.”
Case skid steers that are equipped with a DPF also use active regeneration. “Both active and passive regeneration take place, and that is determined by the type of workload being applied to the skid steer,” says Brad Stemper, solutions marketing manager, Case Construction Equipment. “If the operator is working at consistent speeds and applying high-power loads, that generates higher temperature and regeneration takes place passively. If operation is more inconsistent, where the operator is regularly starting and stopping or working in a low-speed application where temperatures never reach required levels, then active regeneration takes place.”
He notes, “Active regeneration breaks down into two categories: automatic and manual. Both involve injection of diesel fuel into the exhaust stream to help raise the temperature. Manual is often called service regeneration.”
John Deere claims regeneration cycles will not adversely affect the performance of its skid-steer loaders. “Like our larger construction machines, cleaning to oxidize soot in the DPF takes place automatically and has no impact on machine operation under most operating conditions,” says Norwood. “Oil change intervals remain at 500 hours and an additional DPF cleaning interval will be no less than 3,000 hours.”
Proper fluid management is the most effective strategy to achieve maximum service intervals. “Adhering to recommended oil, fuel, fuel additive and coolant specifications in the owner’s manual will maximize the hours of operation before ash cleaning is required,” says Norwood.
“When it does become time for a DPF service, John Deere Reman offers a DPF exchange program that provides a cost-effective, convenient solution,” Norwood comments. “The program provides a clean DPF in exchange for your DPF core. John Deere Reman carefully cleans DPFs utilizing state-of-the-art tooling and robust verification processes to ensure the integrity and longevity of the product. The entire exchange process takes under an hour and your machine is ready to get back to the job.”
DPFs require very little maintenance or attention other than the 3,000-hour cleaning interval. “Although more sensitive to duty cycle and temperature, once installed, these DPF systems are considered to be more user friendly as they do not require fuel additives, have no moving components and only need to be serviced for annual cleaning,” says Wright.
DPF, DOC or SCR?
Some manufacturers are using a combination of technologies across their engine families.
Take Perkins, which supplies engines to various manufacturers. “At Tier 4 Final, no aftertreatment is necessary for our 400 Series engines below 24 hp, while from 25 to 61 hp, the range utilizes a DOC and DPF,” says Nick Stephenson, 850 Series product manager at Perkins. “The aftertreatment has been designed to be as compact as possible, with flexible mounting arrangements to ease installation.”
Between 75 and 121 hp, the Perkins 850 Series uses SCR and a DOC to meet the Tier 4 Final emissions standards. “At Tier 4 Final, we believe the combination of an SCR and DOC system at this power rating delivers the best combination of power and fuel efficiency compared to other technology approaches,” says Stephenson.
Case Construction recently introduced four models with Tier 4 Final engines. The company takes a different approach based on the size. “Our goal has always been to go beyond compliance and do what is in the interest of our customers,” says Stemper. “Our choice in technologies is driven by machine design, operating characteristics and customer needs.”
The Case SR175 and SV185 medium-frame skid steers use a DOC-only solution to meet Tier 4 Final. “These machines are commonly used by contractors with large fleets, as well as rental fleets,” says Stemper. “In these applications, the machines may have various operators and move around between jobsites regularly. Using the maintenance-free, DOC-only solution for these models creates greater convenience and more efficient operation.”
The Case SR130 and SR160 compact-frame skid steers use cooled exhaust gas recirculation (CEGR) technology with a DPF to meet Tier 4 Final.
Caution: High Pressure
High-pressure common rail (HPCR) fuel injection is critical to meeting the emissions standards. But the higher fuel injection pressures also make it necessary to use sound fuel management practices.
“Fuel quality can definitely affect the fuel system in a Tier 4 engine,” says Wright. “Very low sulfur content is recommended with Tier 4 Final engines. Dirty fuel does not burn as clean and can plug fuel injection nozzles as well as the DPFs more quickly, potentially increasing operational costs and losing productivity due to downtime.”
Impurities found in diesel come in many forms. “Particulate matter such as dirt, sand and rust are some of the most destructive because they act as abrasives inside the fuel system,” says Norwood. “Pressures found in HPCR fuel systems can reach upwards of 2,000 bar or 30,000 psi. This has the effect of turning even the smallest particle into scouring agents that can, over time, damage fuel system components such as fuel pumps and injectors. Well-serviced fuel filters can remove much of this contamination, but not all.”
The higher fuel injection pressures associated with the common rail fuel injection systems mean you should pay careful attention to maintenance practices. “Customers should already be diligent about their fuel handling and cleanliness, as this can have a direct effect on component life and thus owning and operating costs,” says Kevin Hershberger, Caterpillar. “HPCR fuel systems are more sensitive to contamination from dirt or water, which means you will need to continue to monitor the fuel water separator and drain water when present, as well as change your fuel filter element per the owner’s manual.
“Probably one of the most important steps for a customer to follow is to not pre-fill the fuel filter element in an attempt to ‘prime’ the fuel system,” Hershberger continues. “This practice can allow unfiltered fuel into the fuel system. The Cat SSL/MTL/CTL products provide an electric priming pump/auto air bleed combination fuel system. This fuel system design allows the customer to simply replace the fuel element, turn the key switch to the ‘on’ position and the fuel system primes and the air is bled out automatically.”
The concern with fuel goes beyond cleanliness. “Our fuel supplies in North America are relatively clean and reliable,” says Stemper. “A bigger concern is ensuring that fuel supplies are kept fresh and that any chance of putting degraded fuel in the machine is eliminated. This is not a concern in most construction applications, where fuel supplies are regularly turned over. Customers should always be aware of this.”
In addition, pay careful attention to the engine oil recommendations from the manufacturer. “Some CEGR systems require the use of higher-spec, more expensive oil to deal with the effects of higher soot levels that result from lower combustion temperatures,” Stemper explains. “Most manufacturers recommend using oil that meets the API CJ-4 oil specification. CJ-4 oil exceeds previous performance requirements and is specifically designed to protect emission control systems, help comply with emissions standards, reduce engine wear and control piston deposits and oil consumption.”
He adds, “CEGR engines with a DPF should also use ultra-low-sulfur diesel fuel (15-ppm maximum sulfur), because small amounts of sulfur can impair the filter's effectiveness.”
Upside of Tier 4 Final
Despite the new hardware on some of the machines, there is a definite upside to Tier 4 Final. “The largest benefit is that customers should expect the same or even better performance with their Tier 4 Final machines,” says Norwood. “In addition, fuel economy has improved on some models, as well as ease of starting in cold weather and at higher altitudes.”
Efficiency has also increased. “Our Tier 4 Final engine range delivers better performance and fuel efficiency when compared to our Tier 3 offering, as well as meets the U.S. EPA emission standards of a 90% reduction in particulate matter and nitrogen oxides,” notes Stephenson. “At Tier 4 Final, end users will notice the improved transient response on our 400F which, in keeping with the rest of the engine range, can be flexibly adapted to simplify installation and servicing."
On the 850 Series, Perkins has seen an increase in performance at Tier 4 Final, with the engine now capable of up to 121 hp at 2,200 rpm, an improvement of around 10% from Tier 4 Interim. “Additionally, the move to a SCR/DOC system means a 3,000-hour filter replacement is not required,” says Stephenson. "The machine operator will need to ensure that diesel exhaust fluid (DEF) is supplied to the machine, a requirement of SCR technology.”
Likewise, Case skid steers have seen performance gains. “There will be a noticeable improvement in the performance of all four models given the enhancements that we have made,” says Stemper. “The SR175 and SV185 have been updated with a new ISM diesel four-cylinder turbocharged and aftercooled engine with a HPCR fuel system and electronic control. The SR175 delivers 21% higher peak torque rise at 1,800 rpm compared to the previous model, while horsepower increases 12% from 60 to 67 gross hp. The SV185 remains at 60 gross hp, yet delivers 7% more torque than the previous version."
The Case SR130 has moved from 46 to 49 gross hp and offers a 9.6% torque boost, while the SR160 offers 60 hp and a 28% increase in torque.
As you can see, Tier 4 Final will offer you a greater range of choices and better performance compared to either Tier 3 or Tier 4 interim. In the end, that is good news for everyone.