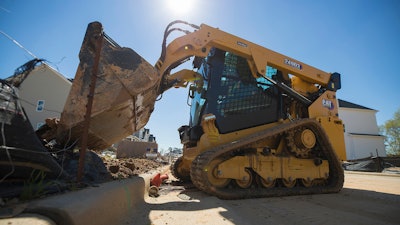
Key differences in compact track loader (CTL) undercarriage design deserve close examination since they can affect jobsite performance. Most undercarriages are either rigid-mounted (also known as solid-mounted) or suspended, with some offering variations or combinations of both. Each offers unique operating characteristics and both have their pros and cons.
"A tracked machines’ ability to perform in a variety of conditions is its main benefit over wheels, so it’s important to know that it will improve productivity from top to bottom," says Buck Storlie, ASV Holdings Inc. product line manager. "Undercarriages impact speed of work, user comfort and overall maintenance costs."
The choice is more complicated than it first appears since no two contractors will use the machine in the same way. You really need to evaluate which track system best compliments how you plan to use the machine.
Bobcat Company advises that you look at the application and determine which type is better suited to the task. For example, are you leveling and grading a high percentage of the time? Or are you traveling across rough ground or new developments most of the time? If the primary focus is leveling and grading, a rigid mount is likely the best solution. If you are moving materials longer distances or have two-speed travel on the machine and operate at higher speeds, a roller suspension, such as the Bobcat 5-Link Torsion Suspension Undercarriage, could be the best option.
Pros and Cons of Going Rigid
One reason the two undercarriage types differ in the applications they're best suited to perform has to do with the distance between the loader lift arms and the right and left carriage. This distance can vary with a fully suspended undercarriage; since the undercarriage can move independently of the mainframe and lift arms, it can make it harder to fine grade to close tolerances.
The design of a rigid-mount undercarriage stabilizes the loader and work group, and is most comparable to a dozer in terms of being designed for grading and pushing, Takeuchi indicates. The lower boom stop also plays a role in the grading and pushing ability of a machine. For example, Takeuchi CTLs provide a positive vertically positioned stop that allows for better weight/power transfer between the attachments and tracks.
Rigid-mount undercarriages also tend to offer simplicity with fewer moving parts. This can make them more durable and easier to maintain. This style of undercarriage also tends to cost less up front than suspended systems.
One drawback of a solid-mount undercarriage can be operator comfort. Since rigid-mounted systems have little to no suspension, every bump is transferred through the machine and to the operator, Storlie points out. It can also cause material to fall from the bucket and wear on components, such as the track, front wheel and undercarriage frame.
Some manufacturers offer suspended seats on rigid-mounted machines to absorb some of the shock of travel over rough terrain, though such seats don't prevent material loss or component wear. Ride control is an option that can address this issue.
One variation of a rigid-mount design includes bogie wheels attached to high-strength steel leaf springs so each wheel flexes to absorb vibrations, Storlie notes. This offers more comfort than a standard rigid design, but not as much as full suspension systems.
The Case for Suspended
Changes to the undercarriage frame and torsion axles on Caterpillar's new D3 Series CTLs reduce machine pitching and rocking, while still offering improved ride comfort.
Caterpillar offers two different fully suspended undercarriage systems, with the type determining whether the machine is designated as a multi terrain loader (MTL) or a compact track loader (CTL). Both use heavy-duty torsion axles to suspend each side of the undercarriage from the machine frame. These axles absorb most of the shock to the undercarriage, machine and operator.
The MTL is designed to provide extremely low ground pressures that enables it to work where other models can't, plus maximizes flotation, ride comfort and speed. “This undercarriage design — all rubber track with rubber-coated roller wheels — is lighter than traditional steel undercarriages,” says Kevin Coleman, senior marketing engineer, Caterpillar. The lower weight, combined with weight distribution throughout the roller system, provides minimal ground disturbance for working in delicate applications.
Applications with long travel distances or hard surfaces can favor a suspended undercarriage.
Variations of suspended systems also offer different levels of performance. "Single-level suspension systems include torsion axles and standard bogie wheels, offering a base level of suspension," Storlie explains. The torsion axles are independent, with four points connecting the chassis to the undercarriage. This enables a smoother ride and reduced shock and vibration in rough terrain.
"The most advanced option is a dual-level system that features independent torsion axles between the undercarriage and machine, as well as bogie wheels that flex with the track," Storlie comments. "This combination minimizes vibrations to the machine and operator for improved comfort and ride quality while maximizing ground contact. A dual-level system also improves traction by keeping more track on the ground."
Open or Closed Case
Another consideration for a CTL undercarriage is whether it features an open or closed design, which affects ease of maintenance.
"Closed undercarriages require enclosed designs because of track tensioner, wheel and sprocket mounting requirements," Storlie explains. "The metal enclosure protects undercarriage components to some extent; however, any dirt, rocks or sticks that make it inside the undercarriage becomes trapped, accelerating wear."
With an open-design undercarriage, the units are self-cleaning, allowing debris to fall out during operation. Their open design concept also makes them easier to clean.
"Field tests have shown open designs can extend service life of some components by as much as 50%," Storlie adds. "Plus, open undercarriages provide fast access to components for quick replacement of parts such as sprocket rollers and bogie wheels."
Built for Durability
The undercarriage will represent a large portion of the costs over the life of the machine. It can make up almost 20% of the machine’s purchase price and nearly 50% of its maintenance cost.
When comparing options, look at how the undercarriage is constructed, how much steel is used (thicker steel = higher strength) and the roller diameter. The larger the diameter, the slower it will turn, which can result in longer bearing life.
Takeuchi builds its undercarriage with large-diameter components and large-diameter bearing surfaces that enhance durability.
The fully welded track frame on Takeuchi loaders uses a unitary design with full-length structural crossmembers that add strength and rigidity to the entire machine. The steel track rollers are permanently sealed with precision metal face seals, and the drive motor positioned in the back to ensure more contact and more wrap, resulting in less stress and wear on the track.
Keeping the drive system out of harm’s way is another consideration. Caterpillar MTLs feature an elevated internal positive track drive to keep the drive components away from ground debris. The sprocket is fitted with replaceable roller sleeves that mesh with molded rubber lugs inside the track for smooth operation. Track lugs travel on the outer edge of the undercarriage roller wheels to ensure proper tracking and help prevent derailment.
Bobcat uses an all-steel suspension system for increased comfort in demanding applications without sacrificing durability. The system reduces vibration and increases comfort, providing a balance between ride, durability and performance.
The Bobcat undercarriage is also fully enclosed for better protection and has few moving parts. Large steel rollers and idlers are utilized to increase the life of the track system, and they are permanently sealed and lubricated for no routine maintenance. Steel imbeds guide and support the center of the track when engaging the drive sprocket, ensuring the optimal the transfer of power.
Tips to Extend the Life of Compact Track Loaders' Rubber Tracks
Impact of Track on the Ground
The amount of track on the ground helps dictate ground pressure and tractive forces. “The suspension system provides increased traction and flotation by keeping the maximum amount of track on the ground at all times,” says Coleman. “The CTL and MTL maximize the track on ground to provide better traction and flotation.”
This can be as important, if not more so, than the track width. The greater the total track footprint, the lower the ground pressure and higher the traction potential. “Couple that with the suspension that helps maintain ground contact, and you have superior traction, flotation and pushing power,” says Coleman.
Another factor that influences ground pressure is the weight distribution. For instance, the rubber track undercarriage on an MTL transfers machine weight to the ground through 24 wheeled contact points so the machine weight is evenly distributed throughout the track.
"Bogie wheels greatly affect flotation and, therefore, performance in soft underfoot conditions,' Storlie agrees. "Some all-rubber track undercarriage machines have as many as four times more ground contact points in their tracks than steel-embedded rubber models. This more evenly spreads the unit’s weight, resulting in lower psi and extra flotation on steep, slippery and wet ground, giving contractors more control on snow, ice, mud and slush."