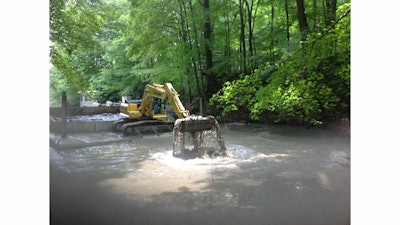
Wickberg Marine Contracting is no stranger to operating excavators around water. This Belford, NJ-based dredging contractor has four hydraulic dredges and mechanically dredges with long-reach excavators on barges. Since hydraulic dredging requires a 12- to 15-acre area to set up, mechanical dredging with excavators is often the preferred method.
Wickberg Marine Contracting currently employs four long-reach excavators and five barges, in addition to standard-reach excavators. Units include a Doosan DX300 60-ft. long-reach, a Doosan DX340 standard-reach, a Link-Belt 60-ft. long-reach and a Caterpillar 350 model.
The long-reach excavators are often strapped onto barges and paired with 5-ft. dredging buckets. The excavators load the material onto material-handling barges. These barges are then moved to an off-loading area where the material is placed on an off-road truck and moved to a location where it can de-water before being hauled away.
Many of Wickberg’s projects are on sensitive waterways. Currently, the company is working in the Erie Canal in Albany, NY. There is a job in Fayette, NJ, and McKay Bay, and a project on the Point Pleasant Canal. Often, these projects are in corrosive environments. “We are in salt water 90% of the time,” says Ted Faxon, general manager.
When working on sensitive waterways, replacing conventional hydraulic oil with a vegetable oil product that is non-toxic to the environment and biodegradable is sometimes mandatory but often a sound policy. “We use the organic, vegetable-type, hydraulic oil in case there is a hydraulic leak,” says Faxon. “We have to change the oil often because it does break down a lot faster. It costs about twice as much.”
But Faxon claims the change is worth the cost. When an excavator leaks or a hose is blown — which is going to eventually happen — you don’t have to report it. You are not damaging the environment.
Maintenance is Critical
When constantly working in water, you need to keep up on maintenance. “The focus should be on the linkage of the machine, such as bucket and stick pins where the machine will lose the grease throughout the day,” says Kent Pellegrini, product application specialist for excavators, Caterpillar. “Any part of the machine that is in contact with the water should be maintained daily if there is a grease location that is submerged or in contact with the water. Sealed bearings and lithium grease would be the preferred path. In adverse conditions, the use of an autolube system may be required. Consistent monitoring of the bucket rotation after hours of use and a good set of ears to hear if the pins are drying out of grease [are also important].”
Choose grease suited for the environment. “Lithium grease provides the ability to adhere over a day’s use in submerged conditions for both fresh and salt water environments,” says Pellegrini. “This grease works well and can last up to a day’s work, depending upon conditions.”
Greasing frequency should also be increased, especially when the machine is removing material in wet, sandy conditions. “The grease is in contact with sand that wears the lubrication out of the bushing and pin ends,” says Pellegrini. “The operator is the source that knows when greasing is required throughout a working day. In some cases, the machine linkage from the bucket and stick pins would need to be lubricated two times a day depending upon the conditions. The autolube system is a good method to help maintain consistent greasing of pins and bushings in applications where machines are used quite frequently in underwater use.”
“Any time you are working with a bucket in the water all of the time, you have to be constantly greasing or the grease just washes out of the system,” says Faxon. “Once every hour at least you have to keep pumping grease into the joints that hit the water. We manually grease. A couple of our machines have the battery grease guns.”
Rust can also be a real issue with prolonged use around water. “The undercarriages rust a lot,” says Faxon. “We had one of our long-reach excavators on a barge for 13 months last year into this year. The undercarriage was rusted. The tracks were rusted. It has taken a while just to get them loosened up again. It really isn’t hurting it too much, but when you start using the track it has to work itself out. That is the nature of our beast.”
There are products available to help prevent the onset of rust. “Caterpillar offers an option called Fluid Film, which is a grease-based formula that adheres to components to reduce corrosion,” says Pellegrini. “The Fluid Film protects the machine components that come in contact with corrosive debris.”
Fluid Films are long-lasting, thixotropic liquids and gels that have been used for over 55 years in the corrosive marine environments of ships and offshore drilling rigs. These products contain no solvents, will not dry out and will penetrate to the base of all metals, providing corrosion protection. They can be applied with airless spray equipment.
JS McCullough Excavating, based in Bainbridge, IN, is a diversified contractor that performs dredging, site work, shoreline stabilization, clearing and snow removal services. “We do just about any kind of excavation service from site development to mechanical dredging,” says Shannon McCullough. “We have been doing this since 2008 and have acquired three barges and a list of earthmoving equipment.”
JS McCullough Excavating determines the best method for dredging or excavation based on distance to the disposal site, the volume of material to be dredged and the consistency of the material being removed. The company uses a One Step placement method for dredging that is preferred by the U.S. Army Corps of Engineers.
McCullough’s fleet includes two Komatsu PC160s, a PC200 and a PC55 excavator and a Bobcat E50 compact model. For dredging, they are placed on barges. The larger excavators use mainly 5-ft.-wide ditching buckets, but they are equipped with quick couplers for easy change-outs. “We prefer not to use a long-reach excavator due to the cost/productivity/expense of transporting the machine,” says McCullough.
Recently, a Bobcat E55 compact excavator and a mini-barge were added to the fleet. The E55 is suited for use in narrow coves. “That has a 4-ft. bucket,” says McCullough. “It doesn’t hold much material.” It can be placed on a 12-ft. barge.
JS McCullough has not had any issues with pins and bushings, despite the dredging application. “We do grease the buckets two to three times a day because it is under the water,” says McCullough. “It seems to be okay so far. We have a couple of excavators that have 3,000 to 4,000 hours on the water.”
The Amphibious Alternative
Operating off a barge is an acquired skill. “It is a training thing,” says Faxon. “You have to get guys in the seat. I only have a few guys I allow out in the water because it is unstable. They cannot be super aggressive. You need guys out there that know what they are doing. Not everybody is allowed to go out and dredge.”
McCullough agrees, noting, “Not everybody can run a barge with an excavator on it. It takes a lot of seat time. You need a lot more experience. The more seat time, the better you get.”
Then there is the amphibious undercarriage alternative to barges or track mats. These typically replace the traditional undercarriage from the slewing gear down.
Wickberg Marine Contracting has used amphibious undercarriages in the past. “I actually rented one for a little over a year,” says Faxon. “We do a lot of work in South Jersey and it is a lot of swampland. Really, that is the only way to do that type of work. You have to get so far out to where you have to work.”
You need to take your time when using an amphibious undercarriage. “It’s a slow go,” says Faxon. “You have to track fairly slowly. But that is okay because you don’t have to use track mats.” The undercarriage design enables the excavator to stay afloat.
When digging, you also have to be a little less aggressive with an amphibious undercarriage. “If I am on track mats and I have a standard 60-ft. long-reach excavator, I can be aggressive and really go after it,” says Faxon. “With the amphibious undercarriage, you cannot be that aggressive with it. You can only get half the production just because of the way they are situated. That is due to the stability because you are floating. Even if you are in the marsh, you are still floating. You can tip the thing over.”
An amphibious undercarriage also requires more maintenance. “You have to be really careful with the tracks. They are not as robust,” says Faxon. “The pontoon is typically lightweight material, so you don’t want go real aggressive with them.”
That said, the amphibious undercarriage does play a critical role in wetland operations. No matter the size of the job, there are times when it provides the only solution. “Sometimes you absolutely have to have them,” says Faxon.