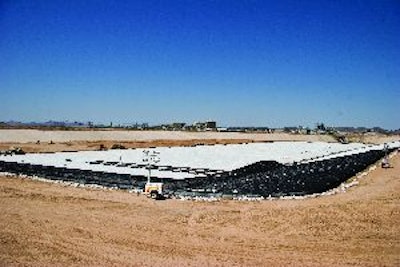
When Arizona Public Service (APS) needed to replace the aging wastewater storage pond at the Palo Verde Nuclear Power Plant, one of the largest nuclear power plants in the world, plant managers called on Asphalt Busters to provide a stabilization solution for sloping sides of the new 40-acre pond.
The treated wastewater is converted to steam in power plant operation to generate electricity. Once used, the remaining water is then pumped to an evaporation pond (more on that later).
As an expert in soil stabilization, Asphalt Busters recommended using an 8 percent cement additive to treat the outside soil to be used in constructing the sloped side walls of the new pond. To ensure that the proposed construction method would meet APS's stringent standards, the contractor performed an onsite demonstration to showcase its spreading and mixing capabilities.
During the demonstration, several air quality tests were made to verify that Asphalt Busters could indeed meet the strict dust/emissions requirements that the plant operation must adhere to under federal regulations. Samples of the cement stabilized matter were also tested to verify that the contractor could also meet the strict spreading, mixing and moisture requirements of the project.
For the actual pond construction, Asphalt Busters used a level mixing area adjacent to the pond structure to spread over 200 truckloads (4,550 tons) of the cement additive (which was applied at a rate of 8 percent of the total combined volume to be mixed) and then injected over 1.4 million gallons of water at 200 to 425 gallons per minute to the treated soil before mixing to a depth of 12 inches in order to produce 55,000 cubic yards of material for the sloped side wall construction.
After Asphalt Busters completed the soil stabilization of the material to be used, a grading contractor then spread and compacted the treated material on the new pond's sloped side walls. The entire pond was then covered with a two-layer liner to seal it from any leakage. Construction was completed between February and May 2006.
With the new pond complete, the soil stabilization contractor then began the process all over to refurbish the existing 80-acre wastewater pond. That work required 5,500 tons of cement to treat 45,000 cubic yards of stabilized soil and was completed between August and October 2007. Asphalt Busters is now in the third phase of the power plant project, stabilizing soil to be used in the construction of a 100-acre evaporation pond. When the new evaporation pond is finished, the original 80-acre evaporation pond will be rebuilt. Dan Selby, vice president of Asphalt Busters, expects the evaporation portion of the project to require 11,000 tons of cement to treat 90,000 cubic yards of material.
Stabilization solution
Selby says proposal and discussion of the soil stabilization solution took about a year before the project actually began.
"When you do work at a nuclear power plant, there are so many procedures and regulations that you have to comply with every step of the way," Selby says. "The existing pond structures were in need of repair, but whatever we recommended had to comply with dust and emissions regulations the plant has to meet.
"There are very stringent regulations concerning dust (particulate matter) that can be emitted from the facility," he continues. "The entire site is under a microscope as far as total emissions being released into the environment. That required some modifications to the skirting around the mixing chamber of our reclaimer/stabilizer, and the emissions output of our equipment was also monitored. The plant has full-time safety personnel who monitor regulations and enforce the requirements.
"The federal government looks at anything that leaves the site. They monitor the carbon emissions generated by any type of activity at the site and not just that of the power plant. They would keep track of our fuel usage during the stabilization process in order to calculate and record the carbon output that occurred during the construction. "
Selby's stabilization crew used a CMI/Terex reclaimer/stabilizer on the project and worked with a grading contractor who placed and compacted the mix on the slopes.
"We not only had to add rubber around the skirting of the mixing chamber, but we also modified the vane feeder of the cement spreader in order to drop a thicker layer of cement in order to control dust," Selby says. "We immediately injected water into the mix on a pass following the cement placement and then unhooked the water to make a final 12-inch-deep mixing pass over the material. Working closely behind the cement spreader again minimized the possibility of dust emitting from the site."
Stabilization expertise
Asphalt Busters has 11 reclaimer/stabilizers in its fleet designed primarily for soil stabilization work.
"We do a lot more soil stabilization than road reclamation," Selby notes. "Most of our road work is pulverization with an occasional full-depth reclamation project.
"A lot of the soil stabilization work we get involved with is either site prep for building projects or parking lot and roadway stabilization," he says. "We used to be in the grading and paving business, but the stabilization business is really a specialty that was needed in this market and one that requires a full commitment in order to deliver the quality customers want."
In 2007, Asphalt Busters provided its soil stabilization expertise to 125 different contractors. Most of the projects were in Arizona and New Mexico, but the contractor does partner with another stabilization contractor in California to provide the equipment and service capabilities required to execute certain types of projects.
"We can provide equipment and technical assistance (operators) that can support a grading contractor who requires our expertise in order to successfully bid and construct a job," Selby says. "We have lime slurry equipment to stabilize soil conditions, and that's something most grading and site prep contractors just don't have in their equipment fleet. So, we're in a position to fill a very specialized niche."
As a specialist in asphalt pulverization and soil stabilization, Asphalt Busters is in a position to provide grading and paving contractors with a service that saves those contractors time and money.
From building pads to parking lots to traffic-bearing surfaces and everything in between, Asphalt Busters is in a unique position to provide contractors with a solid foundation.
"If the existing soil conditions are less than desirable, you can't build a quality project unless you make sure you're building on a quality foundation," Selby says. "We may not be the lowest price, but we believe we're the best at what we do. And any contractor who's going to stake their reputation on building a quality project is going to make sure they're building on a quality foundation."