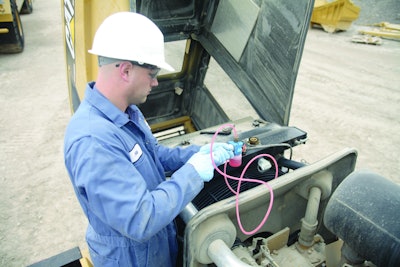
Failure to properly maintain your cooling system is a leading cause of catastrophic diesel engine problems, accounting for approximately 40% of engine failures. The damage being done is difficult to see until it is too late. Liner cavitation and premature failure of the head gasket, water pump, radiator and other critical components occurs within the confines of the cooling system.
“Neglect of coolant maintenance happens all too often and most failures related to the coolant are very preventable,” says Jared Parsons, Caterpillar Fluids Engineer. “As diesel engine technology advances, greater stresses are being placed on the cooling system. EGR coolers put a greater thermal stress on the coolant and can cause breakdown of the glycol.”
Diesel exhaust fluid (DEF)/Selective Catalytic Reduction (SCR) systems, which are starting to come online in the on-road truck market, often use coolant to heat the DEF tank and thaw frozen fluid. “The additional mini-fuel system that is used in many engines today for active regeneration to burn off soot from DEFs can also include a cooling circuit for those components,” says Parsons. “All these new technologies create new opportunities for problems to occur within the coolant and cooling system.”
Randy Bushelli, customer support service and training manager, Volvo Construction Equipment, adds, “Today’s engines use special alloys, seals and ceramics because of the higher peak cylinder pressures, injection pressures and heat that the engine produces. This requires more out of the cooling system than ever before.”
Maintain concentration
It’s difficult to assess the leading cause of cooling system failure. “Of all of the fluids on a piece of construction equipment or truck, probably the least understood is the coolant,” says Stede Granger, OEM technical manager for Shell Lubricants.
One of the primary functions of coolant is to regulate heat within the cylinder head and engine block. It does this by picking up heat and transferring it to the radiator. It also protects against freezing and boiling, and corrosion and pitting of cylinder liners and the engine block.
In the U.S., there are basically two major types of coolant: fully formulated conventional silicate coolant and extended-life coolant (ELC). It’s important to understand which type of coolant is used in your equipment.
“You have to know what type of coolant is in your engine and then maintain it the appropriate way,” says Granger.
Conventional coolants are typically formulated with ethylene glycol base fluid mixed 50/50 with water. Water helps to enhance heat transfer, while ethylene glycol is the freeze point protector. The freeze point needs to be adequately set for the lowest possible temperature the equipment will encounter.
But more glycol doesn’t necessarily translate into a lower freeze point. Once you get past approximately 70% glycol mixed with water, the freeze point actually starts going back the other way.
Water alone is not acceptable either. “If customers use water instead of coolant, it causes the cooling system to corrode,” explains Yukiyasu Endou, director technical service, Komatsu America Corp. “If coolant is not available and water is the only option, we recommend water from a water tap with a corrosion resistor.”
“When you use water that has a lot of minerals in it, you can actually be plating out some of those minerals on the heat transfer surfaces,” Granger points out. Premixed coolants, which use demineralized water, ensure the product you are adding is at a 50/50 ratio.
It’s important to maintain that proper balance. “Too high [a glycol concentration] and you can have issues with pumpability due to high coolant viscosity, as well as overheating, because glycol is a much poorer heat transfer fluid than water,” Parsons explains. “Too low and you can have issues with coolant boiling in engine hot spots, such as turbos, cylinder heads and EGR coolers, leading to cavitation damage or cracking due to thermal stress. Also, when you over-dilute your coolant, you dilute the corrosion inhibitors, as well as the glycol.”
“Proper coolant concentration is very important,” Endou agrees. “Ambient temperature is also important and should be taken into account when determining concentration levels. By maintaining the recommended concentration levels, you will run into far fewer problems.”
It’s just routine
The first step is to ensure the system is filled with coolant and the freeze protection level is adequate for the ambient environment. “An under-filled cooling system can experience major corrosion and overheating issues,” says Parsons. “And inadequate freeze protection can lead to major problems due to low or no coolant flow, or cracking of lines or passages due to expansion of the coolant when frozen.”
Use the same coolant found in the engine for top-offs, and have coolant samples analyzed at intervals as recommended by the engine or vehicle OEM, Parsons advises. Make corrections — such as adding supplemental additives or extender additive for extended-life coolants — based on coolant analysis or OEM recommendations. Change coolant at intervals recommended by the engine OEM based on the type of coolant being used. And be sure to properly clean and flush the system when the coolant is changed.
Routine maintenance recommendations vary a bit from one engine OEM to another. “But generally speaking, conventional heavy-duty coolants should be checked every 250 hours (12,500 miles),” says Parsons. “This typically aligns with the oil drain interval and should be included as a part of the maintenance during the oil change process. This check would be a measure with a field test kit or coolant sample sent for basic coolant analysis to check the supplemental coolant additives (SCA) level.”
By comparison, for its engines or equipment running a Cat ELC, Caterpillar recommends coolant analysis after the first 500 hours, and annually thereafter unless additional checks are warranted due to a suspected problem.
“Conventional coolants do a good job, but you have to maintain them because the additives go away,” says Granger. The additives plate out on the surfaces, forming a physical barrier. After a while, they flake away and new additives must take their place.
“When using conventional coolant technology, many coolant-related failures result from improper management of the coolant inhibitors,” says Parsons. “Problems [include] liner cavitation due to a lack of nitrites, corrosion resulting after inhibitors are depleted and not replaced properly, radiator plugging due to an excess of silicates, head cracking due to the combination of inhibitor additives with poor quality ‘hard’ water, etc.”
Maintenance of additive levels is a must. “If it is a conventional silicate coolant, then it is pretty much mandatory in a diesel engine that you maintain the SCAs,” says Granger. “You do that by either liquid additions or by putting the additives back in through a coolant filter.”
“The No. 1 thing to look for is nitrite,” says Granger. |The nitrites should be above 200 parts per million (ppm), but we recommend that people check with their SCA provider for minimum nitrite requirement. There are test strips for that. Nitrite is the main additive that prevents against liner pitting or cavitation, which leads to pitting or holes in the liners.”
Dissolved solids will build up over time, making it necessary to change the coolant on a periodic basis. In addition, conventional coolants will eventually start to form scale or deposits. Rust and scale buildup adversely affect heat transfer capability.
Conventional coolants also need periodic pH level checks to ensure they maintain a pH level typically between 11 and 8. Readings below 8 indicate that the coolant is becoming too acidic. “Using a different specification of pH could cause rust, pitting of the cylinder, etc.,” notes Endou. “Our engineering standard is a pH level of 7 to 9.”
“The lower the PH the more acidic, and thus corrosive, it becomes,” says Bushelli. “Once the coolant turns acidic, all engine metals start to dissolve. The results are leaking water pumps, heater cores and radiators.”
A matter of chemistry
Granger acknowledges that extended-life coolants are a little more expensive than their conventional counterparts. “But I can also tell you that anybody who does the analysis finds out that ELCs are much cheaper in the long run,” he states.
The cost of a conventional coolant includes the SCAs and the manpower for testing and adding SCAs, he points out. Plus, ELCs promise longer water pump life and better heat transfer.
Caterpillar factory fills its machines with ELC. “Caterpillar has seen many types of issues drastically reduced with the advent of Cat Extended Life Coolant,” says Parsons. “Maintaining coolant chemistry is drastically simplified, while also lowering maintenance costs and extending the coolant drain interval.”
An ELC uses a different chemistry for the inhibitor package. These inhibitors don’t deplete like they do in a conventional coolant. “It uses what we call Organic Acid Technology (OAT),” says Granger. “ELCs protect against corrosion in a much different manner than conventional coolants. The core chemistry prevents against liner pitting. Maintaining the nitrite in the ELC coolant is just not as critical as it is in the conventional silicate coolants.”
ELCs do not plate out on the heat transfer surfaces. The additive is actually attracted to corrosion cells through electro-chemical attraction. “As a result, we only use molecules instead of using massive amounts of additives to coat the surface,” says Granger. There is also no film on the surfaces to impede heat transfer. “In the lab, we can really see the difference between a conventional coolant and an ELC.”
Because of the differences, Parsons cautions against introducing additional additives. “Be sure you do not use an SCA if you are using an ELC product that does not require it,” he advises. “If you add SCA to an ELC, you potentially have issues with the additives dropping out of solution and causing problems like plugging of passages or wear to the water pump seal.”
Likewise, the cooling system should be flushed before switching from a conventional coolant to an ELC. “Systems to be converted from conventional coolant to ELC often [require] a cooling system cleaning first to remove inhibitor deposits put in place by the conventional coolant,” says Parsons.
While ELCs do not need to be checked as frequently as conventional coolant, that doesn’t mean they can be ignored. “Even when running ELCs, I recommend at least taking a look at the coolant, even if no formal tests are conducted,” Parsons suggests. “Check for strange odors, such as a burnt odor, that may indicate a problem. Also check for visible particles in the coolant that can also indicate a problem.”
Proper concentration must also be maintained. Granger advises using a refractometer to calculate an accurate freeze point. “Because glycol has a different refractive index than water, we can very accurately determine freeze point in the field,” he notes.
“The No. 1 item in maintaining an ELC coolant is the freeze protection,” he continues. “If you don’t maintain the freeze protection, you are basically diluting the additives. Once you get to the point where you have too much water, you lose the corrosion protection in the additive. The freeze point in July is just as important as the freeze point in January to maintain the proper level of additive.”
Optimized to the Machine
For the “ultimate” in cooling system and machine performance, consider using OEM fluids.
“Like most OEMs, we recommend that our customers use Komatsu genuine coolant for our products,” says Endou. “We work closely in partnership with our coolant suppliers and conduct many internal tests to make sure we have the best balance to minimize failure and maximize durability for our machines.”
Manufacturers also publish maintenance guidelines based on these fluids. “We recommend cleaning the system and changing the coolant every two years or every 4,000 hours, whichever comes first, when the customer uses Komatsu genuine super coolant,” says Endou, “and every year or 2,000 hours, whichever comes first, when using Komatsu genuine coolant with corrosion resistor.” Corrosion resistor should be added every 1,000 hours.
Volvo serves as a good example of why you should stick with OEM coolant recommendations. “We have Volvo Coolant System (VCS) coolant,” says Bushelli. “It is a monoethylene glycol (OAT) specific to Volvo machines. Basically it has doubled, and in some cases tripled, maintenance intervals for the coolant. It has actually helped the integrity of poorly maintained cooling systems. It will last longer than ELCs.”
But care must be taken when topping off monoethylene glycol, since it is not compatible with ethylene glycol-based products. You need to know what is in the cooling system and top it off with the coolant that is specified.
And switching coolant types may prove ill advised. “For a large customer who wants one common coolant in all engines, care must be taken to research the positive and negative effects that change may have on all engines,” says Bushelli.