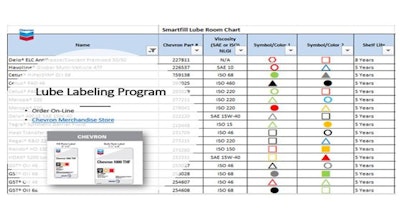
Originally published on Chevron Lube Matters blog
One area where we see many locations fall short of being Best-In-Class is a lubricant labeling program. If you research how to improve lubricant storage, you’re likely to find recommendations about how to organize lubricants using a lube room chart and a corresponding labeling system that any employee could quickly figure out and follow. One of the reasons many sites do not have a lube room chart or a label program is that it takes a lot of time. We know time is in short supply — which is why we have made it easier by creating a system anyone can adopt.
Our system is based on a workplace organizational methodology that originated in Japan called 5S Visual Management, which the best manufacturing facilities worldwide have embraced. 5S Visual Management involves a series of actions which work together to improve productivity and efficiency. If applied correctly, clear visuals throughout a facility identify where all the tools and supplies are supposed to be located. These visuals range from simple diagrams or labels, to detailed process flow maps and directional signs. The general idea is that any person walking through the facility should know what goes where and be able to identify processes throughout the facility.
Chevron developed a similar system called the SmartFill Program. It includes a customizable Lube Room Chart to identify which lubricants belong in the storage area and a corresponding SmartFill label. There are two label sizes available:
- Large labels for bulk tanks, totes or large volume storage solutions and
- Small labels for hoses, top-off containers and component fill points
The SmartFill approach is to match the lubricant product displayed on the chart to the labels and assist in the chain of custody process. A good labeling program reduces the risk of improper top-off and cross-contaminating of products. Thus, being Best-in-Class means having a Lube Room Chart and label that includes the following:
- Product name, which ensures that you can reorder the correct lubricant phone number to supplier, for questions about the product
- ISO grade — viscosity is critical to every machine and component
- Color coding and symbols for easy visual identification for top-off containers, fill points, etc. (optional)
- Product hierarchy based on usage priority
- Supplier part number or internal part number also for purposes of reordering correctly
- Shelf life, which helps with first-in, first-out inventory management in the lube storage room and thus this data is not included on the tank/fill labels
- ISO 4406 Lubricant Cleanliness specification (optional)
In addition to having a ready-to-go program, you can be confident in the labels’ durability, as they are printed on non-melt material and use a special UV Rated Ink to reduce the effects of fading over time.
Rebecca Zwetzig is Chevron’s ISOCLEAN Program Manager. She has 16 years of sales and marketing experience in the oil and gas industry. Her primary responsibilities are marketing Chevron’s ISOCLEAN Certified Lubricants program in North and South America, as well as support-sales enablement with education and value optimization. Since joining Chevron in April of 2013, she has also served as a Direct and Indirect Business Consultant, and Industrial Specialist.