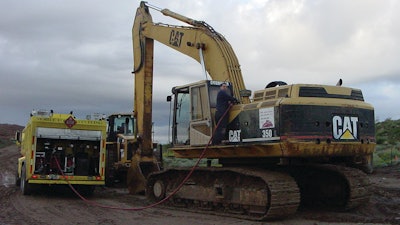
Choosing the best diesel fuel for your fleet should be based on more than the cost of the fuel. One of the more critical considerations is the cetane rating. It is an indicator of the combustion speed and the compression required for ignition. The higher the cetane number, the quicker the fuel ignites under pressure.
Cetane is rated on a scale from 0 to 100 with higher numbers indicating higher combustion speeds. Modern diesel engines often require cetane levels anywhere from 45 to 55. Generally, the higher the cetane number, the better.Water is a problem during transport, storage and use. Newly refined fuel is clean and free of excessive moisture. Refiners and pipeline operators adhere to strict fuel storage tank maintenance procedures with regular removal of water bottoms and occasional chemical treatment to assure American Society for Testing and Materials (ASTM) specifications are met.
When purchasing conventional petroleum-based diesel, you also typically have a choice of grades. The most common and widely available grades are Diesel No. 1 and No. 2.
Diesel No.1 is commonly referred to as winter diesel since it tends to perform better in cold temperatures. It is free of paraffin wax and therefore offers the best operability during the coldest parts of winter. It has a lower viscosity and is less prone to gel in extremely cold climates. The higher cetane rating also results in faster, more efficient starts. This puts less strain on batteries.
Diesel No. 2 is the most common fuel found at fueling stations. Used for most common operating conditions, it is less volatile than Diesel No. 1 and provides greater fuel economy.
Diesel No. 2 is inclined to gel in the winter, however. When the temperature drops, the paraffin in the fuel begins to solidify. Over time, this wax-like substance clogs the fuel line and the fuel filter and prevents the free flow of fuel, making it harder to start the engine. The fuel will begin to gel when the temperature drops to the fuel’s cloud point. This is the point where the paraffin in the diesel begins to look visibly “cloudy.”
As the temperature continues to drop, the fuel will reach the Cold Filter Plugging Point (CFPP). This is the lowest temperature at which it can still pass through a 45-micron filter.
There are additives that can drop the CFPP to prevent gelling. But as the temperature falls, you need to consider changing from Diesel No. 2 to No. 1.
Another common solution is blending fuels to meet the local conditions. Diesel No. 1 and No. 2 can be readily blended, with most service stations offering blended fuels for local weather conditions. They can be blended in almost any ratio up to 100% Diesel No. 1.
On-road vs. Off-road Diesel
There was a time when there were physical differences between on-road and off-road diesel, primarily in the amount of sulfur allowed in the fuel. Ultra-low sulfur diesel (ULSD) for on-road use had a limit of 15 ppm of sulfur, while off-road diesel could contain 500 ppm.
Then, in 2011, it was mandated that all diesel fuel produced in the U.S. be ULSD. While the ULSD fuel is cleaner, the downsides are that it produces less heat energy and has less lubricity, which can increase fuel system wear in older machines.
Today, the difference between on-road and off-road fuel really boils down to the dye color used to differentiate the tax status of the fuel. On-road fuel is taxed to maintain the road infrastructure, while off-road fuel is exempt from this tax.
Red dye is used for off-road fuel — both No. 1 and No 2 — and clear or green is used for on-road diesel. The red dye is easy to spot and can be quickly identified with a black light even if it has been diluted with on-road fuel. This makes it easy for inspectors to catch diesel fuel customers trying to avoid the tax.
Fuel Cleanliness Drives Uptime
The cleanliness of the diesel fuel in your equipment has a major impact on uptime, especially with the advent of Tier 4-compliant engines that rely on high-pressure common rail fuel injection systems. Because these engines work at higher fuel pressures and have smaller injector openings, even the smallest amount of contamination can prove problematic. The most common contaminant in diesel fuel is water.
Fuel cleanliness has always been an essential part of maintaining the performance, reliability and usable life of all diesel engines. International Standard Organization (ISO) cleanliness codes are used to determine the cleanliness level.Several factors contribute to moisture accumulation, including climate, storage tank installation and fuel handling procedures. Temperature changes can cause suspended water in the fuel to settle out.
The ISO cleanliness codes are derived from ISO 4406:99, which states particles per 1 mL. The codes show three sets of separated numbers, which refer to ranges depicting the number of particles present in fuel that are larger than 4, 6 and 14 micron, respectively. As 6- and 14-micron particles are both larger than 4 micron, those particle sizes are also present in the first number. The second number only shows particles larger than 6 micron, while the last number only shows particles larger than 14 micron.
In the past, a cleanliness of ISO 18/16/13 has been specified by the fuel injection equipment manufacturers, which means no more than 1,300 to 2,500 particles greater than 4 micron can be present in the fuel. This level of cleanliness requires careful fuel-handling practices. Make sure all storage, transfer and equipment tanks are clean and fitted with the appropriate filters.
Fuel for Tier 4 engines has to be 100 times cleaner than that used in Tier 3 engines. Where Tier 3 diesel engines can operate with fuel containing between 1,300 and 2,500 particles greater than 4 micron, Tier 4 engines can only have between 20 and 40 particles greater than 4 micron. The cleaner the fuel, the more efficiently it will burn in these engines.
The stringent cleanliness requirements place a greater demand on fuel filters. Even small pieces of dirt or dust that don’t get filtered out of the fuel can get stuck in the openings of injectors, causing decreased engine performance or system malfunctions.
Consequently, filters must now prevent sub-visible particulate from entering the engine. Particulates in the 1- to 5-micron range must be removed, whereas 20 years ago, particulate removal was in the 50-micron range. (The human eye can see 40 micron and above.)
With engine injection pressures reaching 15,000 psi and above, removing water from fuel is essential to maintaining performance. While just 20 years ago engines were able to burn water that entered the fuel system, now even the smallest amount of water can cause an injector tip to blow and the engine to need overhauling.
All fuels contain some water in suspension. But unlike gasoline, diesel fuel is less refined and will hold a much larger amount. This water can cause severe problems with water separators on the equipment. It can also cause the fuel injector tips to explode, resulting in expensive repairs. In fact, slugs of water in diesel fuel can cause sudden cooling in the engine and may result in shortened engine life.
Low levels of water dissolved in the fuel are not necessarily a problem. However, free water in diesel fuel could result in excessive injector wear, filter plugging, power loss and corrosion of engine fuel system parts. You can often tell if there is a problem by a simple visual inspection. If the fuel is hazy, or there is evidence of free water, then there is too much water in the fuel system.
To remove water from fuel, many filter manufacturers will use an absorbent technology to literally absorb the water. Once the absorbent can no longer absorb and hold water, the filter must be replaced.
Water is a problem during transport, storage and use. Newly refined fuel is clean and free of excessive moisture. Refiners and pipeline operators adhere to strict fuel storage tank maintenance procedures with regular removal of water bottoms and occasional chemical treatment to assure American Society for Testing and Materials (ASTM) specifications are met. Unfortunately, after it leaves these facilities, water bottoms removal is often neglected.In 2011 it was mandated that all diesel fuel produced in the U.S. be ULSD.
Several factors contribute to moisture accumulation, including climate, storage tank installation and fuel-handling procedures. Temperature changes can cause suspended water in the fuel to settle out. For instance, any time warm fuel is placed in a cooler tank, whether for storage or transport, moisture will drop out of the fuel as it cools. This makes it necessary to periodically drain off the water, which is a simple task. Water is more dense than fuel, so it always settles out to the bottom of the tanks.
Biodiesel Provides Green Alternative
Despite the recent interest in biodiesel, the concept of renewable diesel is not new. In fact, Rudolf Diesel’s namesake engine, developed in 1893, was designed to run on peanut oil. But the oil boom eventually resulted in an ample supply of inexpensive petroleum-based diesel.
Biodiesel is a cost-effective and more environmentally friendly alternative to conventional petroleum-based diesel fuels when used in the correct applications. It improves lubricity when compared to ULSD. It also reduces emissions of hydrocarbons, particulate matter and carbon dioxide. In addition, biodiesel and renewable hydrocarbon diesel fuel offer higher cetane numbers than traditional petroleum diesel for better combustion.
There are limitations, however, when compared to petroleum-based diesel. Biodiesel typically has a higher cloud point, which means it may not perform well in low temperatures unless blended with traditional petroleum-based diesel; it has a tendency to absorb more moisture; and it typically produces slightly less power and fuel economy when used in higher blends.
Biodiesel comes blended with petroleum diesel fuel in various ratios — from B5, which is 95% petroleum diesel and 5% biodiesel, all the way up to B100, which is pure biodiesel. Engine manufacturers often publish the maximum content of biodiesel recommended for their products, such as B10 or B20.
Biodiesel blends up to a five volume percent are considered to be normal diesel fuel as defined by ASTM D-975, the standard specification for diesel fuel oils.
Biodiesel is chemically distinct from petroleum diesel and has a separate ASTM standard, which was developed back in 2002. It must meet ASTM D6751.
Poor-quality biofuel can be an issue. If biofuel is not refined properly, a by-product called glycerin will become present in the fuel. Glycerin is basically the same thing as a soap. It will coat fuel filters as well as potentially deactivate coalescers, inhibiting their ability to remove water from the fuel.
Perhaps the biggest hurdle for biodiesel is the availability of feedstocks to produce it. It is typically made from oils and fats such as soybean oil or used cooking oil, with soybean oil the most common feedstock. These sources are simply not capable of producing enough quantity to completely replace petroleum-based diesel.
The inherent limitations of biodiesel could soon be addressed by an emerging fuel source known as renewable diesel. Renewable hydrocarbon diesel is a drop-in fuel. It can replace petroleum diesel completely.
Biodiesel and renewable hydrocarbon diesel go through a different production process. Biodiesel goes through a process called transesterification. The molecules in biodiesel are primarily Fatty Acid Methyl Esters (FAMEs). Transesterification removes the esters from oil.
Renewable hydrocarbon diesel goes through a process called hydrogenation. Both processes work to take readily available fats and oils (recycled cooking oil, animal fats and soybean oil) and optimize them for today’s commercial diesel engines.
There are many similarities between biodiesel and renewable diesel. Renewable diesel is a bio-based fuel, derived from a variety of waste agricultural feedstocks, that meets the same standard as traditional petroleum diesel fuel, yet substantially reduces carbon emissions with additional air quality benefits.
Renewable diesel is often produced from a process called hydrotreating, which is already being utilized in today’s petroleum refineries. During this process, hydrogen replaces other atoms such as sulfur, oxygen and nitrogen and converts the oil’s triglyceride molecules into paraffinic hydrocarbons. The resulting renewable diesel reduces waste and by-products, yields a higher energy density and improves cold flow properties. This process also enhances the blended fuel storage and stability of the finished biofuel product.
Yet, hydrotreating is only one method of producing renewable diesel. According to the Diesel Technology Forum, other methods under consideration for creating renewable diesel fuel include biomass-to-liquid (BTL) and thermal conversion process (TCP) technologies. BTL uses high-temperature gasification to convert biomass into synthetic gas, or “syngas,” and then uses a Fischer-Tropsch process to catalytically convert the syngas to liquid fuel. TCP processing converts biomass or other carbonous material into a “bio-oil,” which is then refined into diesel-like fuel.
Both BTL and TCP offer the potential to convert large volumes of cellulosic biomass into liquid fuels, but require further development. They remain far from being economical for large-scale fuel production.
Renewable diesel has the potential to dramatically cut greenhouse gas emissions. The California Air Resources Board (CARB) has also determined that renewable diesel fuel yields air quality benefits that improve the emissions performance of older vehicles that may not use the latest emission control technologies. Renewable diesel can be used as a strategy to achieve sustainability objectives.
Diesel engines are going to be around for the foreseeable future, and renewable and biodiesel fuels hold promise in reducing the dependence on more carbon-intensive fuels.
Resources: Citgo, Diesel Technology Forum, National Biodiesel Board