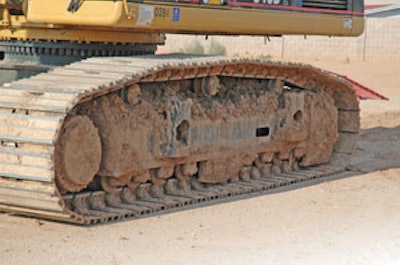
Determining whether to use an excavator with steel or rubber tracks is rather straightforward. "Steel tracks should be used when ground conditions are severe (i.e., rough ground, rocky soils, etc.), which could damage or cut rubber tracks," says Don Lake, Berco America. "Steel tracks should also be used in applications when machine weight and operating loads exceed the capabilities of rubber track machines."
Kara Barnett, aftermarket business manager for Bridgestone Rubber Tracks, agrees that rubber tracks should not be used in environments where cuts are likely. "In those kinds of situations, steel tracks are better. But if you have a situation where you are working on a sidewalk, street or finished surfaces, that's where rubber tracks have an advantage," she states. "There is obviously less noise with a rubber track, and sometimes there is better vibration performance because the rubber tends to absorb the vibration from the machine more than steel."
Application is a key driver of track life. While proper maintenance extends track life, the application determines the maximum possible life expectancy. "In high-abrasive and high-impact conditions, the track life expectancy decreases and operating costs go up," says Lake. "In applications with low impact and low abrasion, track wear is reduced and operating costs go down."
Deciding whether steel or rubber makes more sense in a given application comes down to economics. "For example, if your mini-excavator is working in sand 100% of the time, you will want to take the estimated belt life divided by its cost in comparison with a metal undercarriage," says Eric Mathewson, undercarriage marketing consultant, Caterpillar. "In this case, metal undercarriage life will be longer than rubber belt life. But that extension in life needs to be divided by the extra cost of the metal undercarriage to see the true benefit."
Tension is top priority
Once the proper track for an application is determined, maintenance procedures become the variable affecting undercarriage costs. "Proper track tension is one of the most important factors in reducing undercarriage wear," says Lake. "Improperly tensioned track will result in excessive track wear and operating loads."
The effect is dramatic. "Tight track can accelerate bushing wear by a factor of three times over properly tensioned track," says Paul Ryan, undercarriage service engineering, Caterpillar. (See Chart 1.) "Tracks that are too loose will allow more machine motion and provide a less stable platform for the operator during digging cycles. Loose track may also result in derailing of the tracks during tight maneuvers."
Monitoring track tension on steel tracks is relatively simple. "Track tension is determined by measuring the amount of track sag between the first carrier roller and the idler," says Ryan. "A straight edge or a stringline across the track shoe grousers can be used to obtain this measurement. Track sag is the distance between the straight edge and the top of the shoe grouser."
This measurement should be set to the manufacturer specs. For example, Caterpillar suggests the sag on its excavator tracks be set to 1.85 in. (47mm).
Of course, track tension will change as jobsite conditions change. "Track tension must be monitored in actual working conditions," says Lake. "It should be adjusted whenever soil conditions change, affecting packing conditions, and periodically to compensate for wear."
Rubber tracks also rely on proper tensioning. "Proper tension must be maintained in a rubber track for two reasons - too loose and de-tracking may occur (which will cause damage to the track); too tight and they may break," says Mike Giordano, Solideal.
A loose track may also lead to excess wear. "As the sprocket ratchets on a belt that is too loose, it wears the rubber away from the embedded metal lug, allowing the lug to eventually fall out," says Mathewson. "Track that is over tensioned can have a similar effect, causing excessive load on the lug when it is in the sprocket."
Although all rubber tracks use the same basic components - rubber, steel cords and core metal embeds - every manufacturer uses its own highly engineered design. "The type and amount of each component varies," says Barnett. This will impact the actual suggested track tension.
Always follow manufacturer recommendations since the ideal track tension varies between excavator brands and models.
However, Giordano adds, "A rule of thumb for best track life is 15 to 20mm of sag off the rollers."
Keep it clean
All undercarriages require periodic cleaning. For instance, consider rubber track. "If mud and debris is trapped in the undercarriage, it can affect the track in many ways," says Giordano. "It can stop the idler arm from moving, placing the tracks in an over-tensioned situation. Debris can stop the rollers from moving properly and cause the rollers to scrub the inner surface of the track. Mud can build up on the rollers and idlers, causing 'stretching' of the track or placing it in an over-tensioned situation."
Similarly, packing in steel tracks will lead to excessive tension.
Use a narrow shoe
"The width of the track shoe is directly related to machine weight and soil conditions," says Lake. Yet, the shoe width impacts undercarriage chain life on steel track excavators. "You should always use the narrowest shoe that provides adequate flotation."
"Increasing shoe width adversely affects the bending loads into the track chain with resulting stress increases on the components," says Ryan. "These bending loads can result in loss of pin and bushing retention and, in some cases, track link cracking. An increase of 4 in. in shoe width will increase track chain stresses by 20%." (See Chart 2.)
It is a balancing act between productivity and cost. "Wide shoes can increase productivity by being able to get into places where other machines can't, but with an expected undercarriage wear and structural life of as little as 1/10th of the same machine with standard shoes working in firm soil," Lake points out.
You should also match the type of shoe to the application. "For minimal ground disturbance, the triple grouser shoe is recommended. It is the most common shoe used on small- and medium-sized excavators," says Ryan. "If increased traction is necessary, the single grouser shoe will provide maximum ground penetration. For example, if the operation involves a significant amount of steep slope work, the single grouser shoe may be the best choice. The double grouser shoe offers a compromise on ground penetration, while maintaining high bend strength."
Likewise, you need to pick the appropriate track type for the application. "Sealed and lubricated tracks should be used in high-abrasion, low-impact conditions," says Lake. "Sealed or sealed and greased tracks should be used in low-wear, high-impact conditions."
Operator-induced wear
The operator plays a key role in maximizing steel track life. "Slipping of the tracks should be avoided. And the operator should avoid reverse travel whenever possible, especially high-speed reverse travel, which causes increased wear," says Lake.
Operators also need to be aware of where the idlers and sprockets are positioned during operation. "The operator should avoid traveling the excavator with the sprocket in the front," says Ryan. "This means that the tracks are operating in reverse and, due to track chain geometry, reverse operation results in higher wear than forward operation."
You should also avoid digging over the sprockets. "Operators should always dig over the idler so that vertical loads are transferred through the track link to the idler, and then to the machine frame," says Ryan. "Digging over the sprocket may result in cracked and/or broken bushings because, in this condition, the vertical loads are transferred directly through the bushing to the sprocket and into the frame."
Also avoid digging over the side, which causes high bending loads in the track shoes and track chain.
Rubber tracks can also suffer from operator abuse. "The life of a track is very much dependent on the person operating the machine and the environment they are operating it in," says Barnett. One common abuse is running the track up onto a curb.
There is a series of core metal embeds on the inside of the track, which engage with the sprocket. These embeds generally stop 1 to 2 in. from the track edge.
"When the operator runs into a curb, the excess force causes that rubber to shear off the end of that core metal embed," Barnett explains. "Then you have a crack running down the edge of the track about 2 in. from the outside edge. That whole outside edge is going to end up chunking off. If the steel cords are exposed to any moisture from that cracking, it can cause the steel cords to corrode and the track to fail."
This is also why a rubber track excavator should not be driven over sharp objects. "Sometimes cosmetic cracks can be filled in or repaired for a short-term fix to minimize the exposure of the steel cords on the inside and keep catastrophic failure from occurring," says Barnett. "Once the steel cords have snapped, there is really no good way to repair the track. If the core embeds come out, there is really no way to repair a track in that condition either."
Avoid harsh environments
"Abrasive or contaminated environments have a more severe affect on rubber tracks in comparison to a metal undercarriage," notes Mathewson.
Exposure shortens the life of rubber. "Any rubber product will start to break down when exposed to salts or oils due to the chemical properties rubber possesses," says Giordano. "For this reason, we suggest you avoid running the track any more than you have to in oily/salty environments. When contact does occur, the rubber tracks should be rinsed with water as soon as possible."
It is also important to consider that not all rubber tracks are engineered to operate in the same environment. For example, a mini-excavator track generally can't survive in the same operating conditions as an asphalt paver. "The asphalt pavers obviously have a different compound that is used than the mini-excavator tracks because of the difference in the environment," says Barnett.
Storing rubber
Rubber tracks should always be stored on their sides. "This will ensure that there are no crimps in the track," says Giordano. "Crimping a rubber track will weaken the steel cords and increase the likelihood that the track will break prematurely."
Mathewson adds, "Storing the belts with a fold that is too aggressive can cause the belts to not ride properly when installed on the machine."
If tracks are to be stored for a long time, also avoid exposure to ozone to keep the rubber from cracking.
Minimize travel
Finally, it is important to remember that all undercarriages wear with use. This emphasizes the importance of eliminating unnecessary travel.
"Contractors can minimize undercarriage costs by minimizing the amount of excavator travel on the jobsite," says Ryan. "Increased machine travel translates directly to increased undercarriage wear.