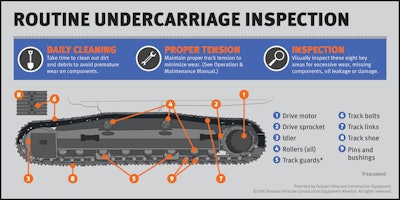
The undercarriage of tracked heavy equipment, such as crawler excavators, consists of many moving components that need to be maintained for them to function properly. If the undercarriage is not routinely inspected and maintained, it can easily cost you valuable time, money and potentially decrease the track’s life span.
By following these six tips, outlined by Shane Reardon, Doosan excavator product specialist, you can get better performance and life out of your crawler excavator’s steel track undercarriage when working in construction applications.
Tip No. 1: Keep the Undercarriage Clean
At the end of each workday, excavator operators should take time to clean out dirt and other debris that may lead to undercarriage buildup. Shovels and pressure washers can be used to help clean the undercarriage.
If the undercarriage is not routinely cleaned, it will accelerate premature wear on components. This is especially true in colder climates.
“If operators neglect to clean the undercarriage and are working in a colder climate, the mud, dirt and debris will freeze,” Reardon says. “Once that material freezes, it can start to rub on the bolts, loosen the guiding and seize up the rollers, leading to potential wear later on. Cleaning the undercarriage helps prevent unnecessary downtime.”
In addition, debris can add weight to the undercarriage, reducing fuel economy.
Many manufacturers now offer undercarriages that are designed for easier track carriage cleanout, helping debris fall to the ground rather than become packed in the track system.
Tip No. 2: Routinely Inspect the Undercarriage
It is important to complete a full undercarriage inspection for excessive or uneven wear, as well as look for damaged or missing components. According to Reardon, if the machine is being used in harsh applications or other challenging conditions, the undercarriage may need to be inspected more frequently.
The following items should be inspected on a routine basis:
- Drive motor
- Drive sprockets
- Main idlers and rollers
- Rock guards
- Track bolts
- Track chains
- Track shoes
- Track tension
During a routine machine walk-around, operators should check the tracks to see if any components look out of place. If so, this could indicate a loose track pad or possibly a broken track pin. In addition, they should inspect the rollers, idlers and drives for oil leakage. These oil leaks could indicate a failed seal which could lead to a major failure in the rollers, idlers or track drive motors.
Always follow the manufacturer’s operation and maintenance manual for proper undercarriage maintenance.
Tip No. 3: Follow Basic Best Practices
Certain construction jobsite tasks can create more wear on excavator tracks and undercarriages than other applications, so it is important that operators adhere to the manufacturer’s recommended operating procedures.
According to Reardon, some tips that can help minimize track and undercarriage wear include:
- Minimize time on slopes: Constant operation on a slope or hill in one direction can accelerate wear. However, many applications require slope or hillside work. When moving the machine up or down a hill, make sure that the drive motor is in the correct position to reduce track wear. According to Reardon, the drive motor should be facing the back of the machine for easy maneuverability up a slope or hill.
- Avoid harsh environments: Rough asphalt or concrete or other abrasive materials can cause damage to tracks.
- Reduce unnecessary spinning: Train your operators to make wide, less aggressive turns. Track spinning can lead to wear and decrease productivity.
- Select the correct shoe width: Choose the proper shoe width by considering the weight of the machine and application. For instance, narrower excavator shoes are better suited for hard soil and rocky conditions because they have better soil penetration and grip. Wide excavator shoes typically work well in soft underfoot conditions because they have more flotation with lower ground pressure.
- Pick the correct grouser: Consider the application before choosing the number of grousers per shoe. A single or double grouser may work well when laying pipe but may not work well in other applications. Typically, the higher number of grousers the track has, the more contact the track has with the ground, vibration is reduced and the track will last longer when working in more abrasive conditions.
Tip No. 4: Maintain Proper Track Tension
Incorrect track tension may lead to increased track wear, so it is important to adhere to the proper tension. As a general rule, when your operators are working in soft, muddy conditions, it is recommended to run the tracks slightly looser.
“If steel tracks are too tight or too loose, it can quickly accelerate wear,” Reardon says. “A loose track could cause the tracks to de-track.”
Tip No. 5: Consider Rubber Tracks for Sensitive Surfaces
Rubber tracks are available on smaller excavators and these models excel in a variety of applications. Most noticeably, rubber tracks provide good flotation, allowing excavators to travel across and work on soft ground conditions. The rubber tracks have minimal ground disturbance on finished surfaces, such as concrete, grass or asphalt.
Tip No. 6: Adhere to Proper Digging Procedures
Excavator operators should follow basic operating procedures as outlined in the manufacturer’s operation and maintenance manual to minimize excessive wear and track degradation.
The undercarriage makes up a large portion of track replacement costs. It consists of expensive components. Adhering to these six undercarriage maintenance tips, as well as proper track maintenance can help keep your overall cost of ownership down and extend the life of your tracks.