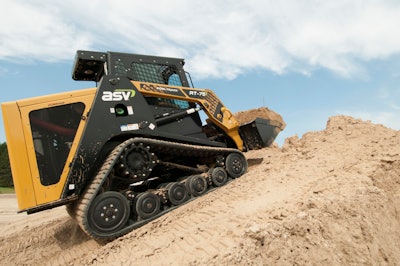
By Buck Storlie, ASV Holdings Inc. product line manager
Examining a compact track loader involves a thorough look in and around the equipment, but it’s what’s underneath that matters most. A tracked machines’ ability to perform in a variety of conditions is its main benefit over wheels, so it’s important to know that it will improve productivity from top to bottom. Undercarriages impact speed of work, user comfort and overall maintenance costs.
Most undercarriages are either rigid-mounted — also known as solid-mounted — or suspended. Both have pros and cons, depending on the application and desired comfort level. Some manufacturers offer variations or combinations of both.
Rigid-mounted vs. Suspended Undercarriage
Rigid-mounted systems have little to no suspension, and therefore the effect of every bump is transferred through the entire machine and to the operator, causing material to fall from the bucket and wearing on components, such as the track, front wheel and undercarriage frame. Because of the simple design and few moving parts, this style of machine tends to cost less up front than suspended systems.
To counter the adverse effects on the operator, a few rigid-frame undercarriage manufacturers offer suspended seats designed to absorb some of the shock. While these seats enhance operator comfort, they do nothing to prevent material loss or component wear. Other designs incorporate bogie wheels attached to high-strength steel leaf springs so each wheel flexes to absorb vibrations. This offers more comfort than a standard rigid design, but not as much as full suspension systems.
Ride control — or loader suspension — is an option to reduce material loss in rigid-frame undercarriages. The system works by using an accumulator as a shock absorber for the loader lift circuit to help keep material in the bucket. However, ride control does little to help with machine impacts and operator comfort. Ride control can also be combined with some full suspension systems for the best of both worlds: minimal spillage in load and carry applications and maximum operator comfort.
Full suspension systems absorb much of the vibration before it gets to the operator or the attachment. This means less material loss and wear, plus faster speeds over rough terrain, allowing for more productivity.
Variations of suspended systems each offer a different level of performance. Single-level suspension systems include torsion axles and standard bogie wheels, offering a base level of suspension. The most advanced option is a dual-level system that features independent torsion axles between the undercarriage and machine, as well as bogie wheels that flex with the track. This combination minimizes vibrations to the machine and operator for improved comfort and ride quality while maximizing ground contact. A dual-level system also improves traction by keeping more track on the ground.
To compare these undercarriages, a northern Minnesota testing facility used an accelerometer to measure the G-force from a dual-level suspension-equipped CTL with six other manufacturers’ rigid-undercarriage machines. Operators maneuvered the machines at maximum speed in low gear over two staggered rows of 3.5-in.-high, 10.5-in.-wide concrete blocks spaced 9 feet apart.
The test found the dual-level suspension machine transmitted 6.4 Gs of machine vibration, while the average of the other machines was 34.9 Gs. Another test at maximum speed in high gear over a smooth surface measured 1.8 Gs from the dual-suspension model and an average of 6.5 Gs from the other loaders.
In addition to providing the smoothest ride, the dual-level suspension machine was the fastest in each type of terrain, moving at 6.3 mph for the first test and 9.3 in the second. The other machines moved an average of 5.2 mph for the first test and 7.7 mph for the second.
Open or closed?
Another consideration of a compact track loader undercarriage is whether it features an open or closed design, which affects ease of maintenance.
Closed undercarriages require enclosed designs because of track tensioner, wheel and sprocket mounting requirements. The metal enclosure protects undercarriage components to some extent, however, any dirt, rocks or sticks that make it inside the undercarriage becomes trapped, accelerating wear.
With an open-design undercarriage, while debris may get inside, the units are self-cleaning, allowing debris to fall out naturally during operation. Because of their accessibility, open designs also are easier to clean than closed designs. Field tests have shown open designs can extend service life of some components by as much as 50 percent. Plus, open undercarriages provide fast access to components for quick replacement of parts such as sprocket rollers and bogie wheels.
What’s the track made of?
Compact track loaders on the market today come with either steel-embedded, all-steel or all-rubber tracks. Each offers a different wear life and some are more ideal than others for certain applications.
The majority of CTL manufacturers offer steel-embedded undercarriages made mostly of steel components: Steel rollers mesh with steel lugs to move rubber tracks. The steel-on-steel parts crush or kick out stuck material, and the heavy-duty components work together with few other moving parts for durability with little maintenance. Steel-embedded rubber tracks average a 1,000-hour lifespan, but can reach 2,000 hours in the right conditions and if well maintained.
Some manufacturers also offer all-steel tracks to prolong wear life in specialty applications. Heavier and more expensive, the tracks are best suited for demanding applications such as demolition, where jagged concrete, rebar and other materials may damage other tracks. The tracks are similar to those on a dozer and offer similar traction, making them good for earthmoving on solid ground. However, their weight and steel cleats require a slow speed to minimize wear and often result in a rough ride and increased risk of damaged terrain.
Rather than steel, a few manufacturers build tracks with fiber-reinforced industrial rubber compounds, and wheels with heavy-duty polyurethane and rubber, the same materials used on many military vehicles today. This combination allows the tracks to excel in flotation and durability, making them ideal for most conditions. No steel also means no rust. When it comes time to replace the track, rubber — which is more pliable and weighs about half that of steel-embedded tracks — is easier to handle. The average all-rubber track life is about 1,500 to 2,000 hours but can be as high as 5,000. In addition, the rubber track’s lower weight allows for higher speeds — as much as 33% faster — than steel-embedded rubber tracks, and all at a lower ground pressure.
The type of track material also impacts horsepower efficiency. Steel-embedded and all-steel tracks create more friction as the steel sprocket teeth engage with steel lugs while protruding through the track, a system that requires more horsepower to move the machine. Since all-rubber tracks don’t use steel-on-steel contact, they build less friction, and more horsepower directs to the hydraulic system and attachment, increasing a CTL’s efficiency by as much as 10 percent.
Track Derailment
A few undercarriage features can reduce the risk of track derailment. Many manufacturers create tracks with lugs only on the inner edge of the bogie wheels, while some include track lugs on the outer edge as well, which virtually eliminates track derailment by guiding the wheels.
Other factors that improve track retention are the number of wheels, the track’s ability to conform around objects and maximize ground contact, the track style and the track tensioner type. Steel and steel-embedded tracks use grease or hydraulic tensioners. These tensioners apply preload to a spring which is necessary to compress and absorb material that is ingested into the track system because the steel makes the tracks inflexible. All-rubber designs, on the other hand, are pliable, so they feature a simple screw-style tensioner that doesn’t need a spring device, eliminating unwanted spring compression that contributes to derailment.
Another series of tests at the Minnesota facility compared CTLs with different undercarriage styles in similar conditions. The first option included a steel-embedded track with lugs only on the inner edge, as well as a grease spring tensioner and 11 wheels per track. The second machine featured an all-rubber track with lugs on both the inner and outer edge, a screw-style tensioner and 12 wheels per track. The results showed that operators needed to tension the steel-embedded track three times and reinstall it after a derailment within 500 hours of operation. The all-rubber tracks, however, required no tensioning and didn’t derail even after operating for more than 1,000 hours.
What moves it?
The type of drive system components can also affect maintenance, operating costs and performance. Manufacturers include either external drive or internal drive sprockets, depending on the type of tracks.
External drive sprockets move steel-embedded tracks via steel teeth that protrude through holes in the track. These systems involve 90 percent of drive torque moving through only one or two sprocket teeth at a time, accelerating teeth wear and creating steel “hooks” over time, which can reduce track life. External drive systems also require operators replace the entire sprocket when teeth worn.
Internal drive sprockets feature replaceable steel rollers that fit with molded rubber lugs to move all-rubber track designs. There is no direct wear between rollers and track lugs in internal drive systems, and replaceable sleeves mean operators don’t need to change out the entire sprocket when individual rollers are worn down. Bogie wheels with metal face seals are another maintenance-reducing feature, as opposed to rubber lip seals, since the metal eliminates the need for maintenance over the life of the machine.
Bogie Wheels
Bogie wheels greatly affect flotation and, therefore, performance in soft underfoot conditions. Some all-rubber-track undercarriage machines have as many as four times more ground contact points in their tracks than steel-embedded-rubber models. This more evenly spreads the unit’s weight, resulting in lower psi and extra flotation on steep, slippery and wet ground, giving contractors more control on snow, ice, mud and slush. Ground pressure on a mid-sized all-rubber track machine, for example, can be about 4 psi while a similarly sized steel-embedded rubber track machine may be 5.5 psi. Lower ground pressure means a lower risk of turf damage, as well as faster and safer work when clearing snow or driving on a muddy construction site, ranch or farm. Low psi and good flotation can even give a compact track loader the ability to drive over snow or mud without sinking.
Remember that a compact track loader is more than just its horsepower or feature-packed cab, undercarriage design is just as important a factor. Examine track loaders top to bottom, keeping undercarriage design, suspension, track type and drive system in mind. Different designs can mean varying levels of comfort, performance and, ultimately, return on investment.