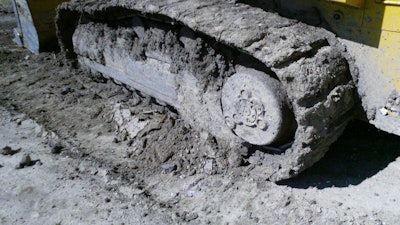
When operating construction machinery that runs on steel tracks, controlling undercarriage cost is critical to optimize the total cost of ownership. Consider that 45% to 60% of the repair and maintenance costs associated with maintaining a dozer over its life relate to the undercarriage.
By selecting the most appropriate undercarriage, following a structured maintenance plan and training operators, you may dramatically lower system costs and thus lower equipment owning and operating costs. There are controllable and non-controllable variables that determine undercarriage life. Not much can be done about the application or underfoot conditions, but the operator’s behavior and the correct machine setup play a major role in cost control.
The best place to start is with proper component selection.
Tip 1: Select the Correct Shoe Width
Choose the proper shoe width by considering the weight of the machine and the application. For instance, narrow shoes have better soil penetration and grip. Wide shoes typically work well in soft underfoot conditions because they have more flotation with lower ground pressure.
Proper shoe width is directly correlated with the machine weight and wheelbase. The wheelbase defines how many shoes are in contact with the terrain. The machine weight with the required attachments defines the ground pressure.
For hard and abrasive material, use narrow shoes; for soft ground such as clay, use wider shoes. For swamps or peat, an LGP (low ground pressure) undercarriage with extreme wide shoes is necessary.
Most undercarriage experts advise using the narrowest shoe possible. The wider the shoe, the harder it is going to be on the undercarriage structurally. Shoes that are too narrow can create their own problems. They allow the machine to sink. It is harder on the powertrain, which results in higher fuel consumption. It will also bring more material into the undercarriage during turns, which reduces undercarriage wear life.
Determine the narrowest shoe that will support the machine’s weight above ground. Go wider only when absolutely necessary.
Tip 2: Choose the Right Grousers
Consider the application before choosing the type and number of grousers per shoe. A single or double grouser may work well when laying pipe, but may not work well in other applications.
Typically, the higher number of grousers the track has, the more contact the track has with the ground. Vibration is reduced and the track will last longer when working in more abrasive conditions.
Tip 3: Pick the Correct Shoe Type
Mid-size dozers offer a dizzying array of shoe types. The number of choices allows the machine to be best matched with the underfoot conditions.
Moderate service (MS) shoes are recommended for use in soft and non-abrasive material. In more abrasive conditions, extreme service (ES) shoes are typically the more cost-effective choice.
The ES shoe helps you from a structural standpoint. It will resist breaking because of the plate thickness. It has a taller and wider grouser. Not only do you get better durability, you get better wear life. But that does come with a trade-off. With the grouser being taller and wider, it is harder to get into the ground, so you could suffer penetration problems. ES shoes also add significant weight to the machine, which could affect flotation.
The grouser works like a blade on the soil, so the thinner the grouser shape, the easier the ground penetration, which results in a smoother ride. ES shoes are not recommended in applications where a smooth ride is key or where the soil provides very high impacts to the undercarriage.
ES shoes are suitable for rock, shotrock applications or pioneering dozers (with oscillating track frame). These shoes are hard on the chain joints, so use them sparingly. Most larger dozers use severe-service shoes, but smaller machines do not benefit from their use, since they add cost and affect smoothness of travel. Severe service shoes affect grading performance, since they can create vibrations that can be transferred to the blade.
Many shoes have options such as trap holes to get material to flow out of the link box. Trap hole shoes are recommended when you are in conditions such as tacky mud that would likely cause a tight track incident. The sprockets will eject the mud out of the link box and ensure you maintain proper track tension.
In other applications, a trap hole shoe can prove detrimental. The shoe is there for flotation. If you punch a hole in the middle of it and it is in soft underfoot conditions, all of that material will eject up through that hole and come right into that link assembly, which can reduce wear life.
Clipped corner shoes are often used for fine grading. The clipped corner gives you less ground disturbance when you are making turns. It allows the tractor to turn more easily. Clipped corners on wide shoes prevent the shoe from bending too much and reduce the risk of links breaking.
There is not one shoe that will work in all applications.
The choice will depending upon your geography, climate and
soil condition.
Tip 4: Select the Proper Chain Design
Lubricated chains are indicated for machines that are constantly moving because the oil is able to create a constant film between the pin and bushing. Sealed and lubricated track (SALT) is required for most applications. It reduces the internal friction in the undercarriage by providing internal oil lubrication, resulting in a long life. This system can be used in almost any application, except in high heat, such as hot slag applications.
Of course, there are still applications for dry track. Dry track is stronger against torsional stress and twisting types of movement. But internal pin and bushing wear will become the No. 1 reason for service work, replacing external bushing wear.
Rotating bushing designs are another means to extend component life. Rotating bushings reduce or eliminate internal pin and bushing wear. Fewer service intervals equal more uptime and less cost per hour.
Rotating bushing tracks take the sliding component out of the wear equation. Therefore, this type of track is much more tolerant of reverse operation. Wear rates are almost nothing, even in high-speed reverse. The rotating bushing is crawling on the sprocket, allowing it to always maintain a round shape whether the operator drives forward
or backward.
In the past with conventional undercarriages, the bushing would be worn at a much higher rate due to “scuffing” wear around the sprocket. With the onset of rotating bushing undercarriages, this bushing scuff wear is basically eliminated.
Rotating bushing designs do not require the machine to be taken out of service to have a technician turn or rotate the pins and bushings. The design goal is to balance the wear of the undercarriage components so they wear out at about the same time.
Not all applications are suited for a rotating bushing track design. Avoid these systems in applications with heavy impact shock loads (rocks and stones), especially when ripping. These impact loads tend to crack and break the rotating bushing portion of the track system, which results in costly track repairs
and replacement.
Tip 5: Maintain Proper Track Tension
Tight track is the No. 1 cause of premature track wear on a dozer undercarriage. When you change applications, run the machine for an hour on the new site and then set the track tension to the correct specification. Re-check the tension as conditions change. For instance, if it rains overnight or during work hours, that will change the amount of packing and track tension will need to
be readjusted.
A tight track can substantially increase wear on the idlers, links, bushings and sprockets. Tight track can also damage the sealing system due to high track joint temperatures. It is always better to run a bit on the loose side so that if packing increases, there is some margin of error before damage/increased wear begins.
Tight track will also rob useful horsepower and increase fuel consumption.
Conversely, when a track is too loose, it can start to drag on the top of the roller frame. It can also result in derailing, chain popping out from the sprocket, unusual impacts between parts and possible chipping and spalling.
The perfect balance between tight and loose stays within the sag recommended by the manufacturer. This requires regular attention. During the life of the undercarriage, normal wear on parts will naturally allow the tracks to become loose.
Tip 6: Keep It Clean
At the end of each workday, operators should take time to clean out dirt and other debris that may build up in the undercarriage. Shovels and pressure washers can be used to help the cleaning process.
A packed track will rob horsepower to the ground and will reduce undercarriage life due to heat and additional stresses. This is especially true in colder climates where mud, dirt and debris will freeze.
The biggest issue when you do not clean out the undercarriage is that the material dries/hardens or continues to fill the space between the frame and track. The links eventually start to drag across it. This adds an additional contact point for
the links and results in higher wear rates.
Mud packing over time creates extra layers of material on the undercarriage parts, over-tensioning the track group association and increasing the wear. Sometimes, hard materials like rocks or concrete getting stuck between the roller shells and the rock guards can lock up the rollers, creating wear flat spots on these components.
Tip 7: Conduct Routine Inspections
Complete a full undercarriage inspection to look for excessive or uneven wear as well as damaged or missing components. If the machine is being used in harsh applications or other challenging conditions, the undercarriage may need to be inspected more frequently.
The following items should be inspected on a routine basis:
- Drive motor
- Drive sprockets
- Main idlers and rollers
- Rock guards
- Track bolts
- Track chains
- Track shoes
- Track tension
Inspect the rollers, idlers and drives for oil leakage. Oil leaks could indicate a failed seal, which could lead to a major failure in the rollers, idlers or track drive motors.
Tip 8: Understand Wear Limits
Eventually, chains, sprockets and idlers need to be replaced. Change them out as a set if possible. If you put used rollers on new links, it will reduce the overall life of the link; the same goes for used segments on a
new bushing. The issue with
this is that the new component and the old component are going to work against each other until their shape matches up again, which results in higher wear rates.
Undercarriage life is driven by wear. You want to run the maximum life of the undercarriage without exceeding it. Once the wear of the link achieves the maximum, the link pin boss may get stuck against the roller flange, even if the roller shell is worn out at its own max. The pin and bushing may start popping out from the worn sprocket. The track adjuster may reach the end of its stroke and not be able to keep the tension on the system anymore, causing the tracks to derail. Any of these factors can cause serious damage and even safety-related issues.
Tip 9: Understand Effects of Control Movements
Modern hydrostatic machines allow operators to turn fast and on a small radius. This creates additional stress on the undercarriage as the track group assembly is subjected to additional pulling forces coming from the final drive. Those extra efforts tighten the track group assembly and increase the wear rate.
This is where operator skill makes a big difference. Sharp turns and counter rotations increase contact stresses between components and should be minimized. These maneuvers apply high stress to the tracks by braking one side or the other. If these maneuvers are done more slowly, it does a lot less harm to the undercarriage. As speed increases, the amount of damage increases. A good track inspection will pick up indications that the machine is not being operated correctly.
High-speed reverse should also be avoided. On fixed bushing track, the bushing and sprockets will see increased wear rates while running in reverse.
During reverse operation, there is sliding wear between the bushing and a sprocket at any speed. But as the speed increases, the amount of load and contact changes, increasing wear rates. Speed also tends to move the bushing out of the root of the sprocket to a point higher on the sprocket tooth, which also changes the contact pattern and results in higher wear.
Tip 10: Pay Attention to Machine Orientation
Side hill operation accelerates undercarriage wear, especially on the downhill side of the machine. The link side is working constantly against the roller flanges, creating accelerated wear on the links and roller flange. The links and rollers on the downhill side will see higher than normal loads and an increased wear rate, whereas operating on flat ground usually wears the undercarriage mostly on the rail surfaces of both the links and rollers.
Operating on side hills wears off the flanks of the links, which reduces overall link width and the available contact area with the rollers. This leads to increased contact stress when the machine operates on flat ground.
It is important for the operator to balance machine orientation as evenly as possible. If feasible, operate half of the time with one side of the machine facing downhill and the other half facing uphill to allow for more even wear.
When moving tracked equipment such as an excavator up or down a hill, make sure that the drive motor is in the correct position to reduce track wear. It should be facing the back of the machine for easy maneuverability up a slope or hill.