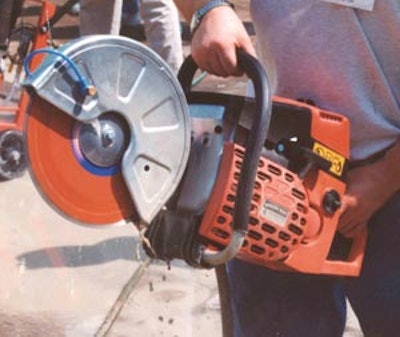
Given the variety of diamond blades available on the market, choosing the right one for the job can be a daunting task for your customers, but you can help make the process easier by arming yourself and your staff with the right information.
In order to effectively serve your customers, it’s important to display your blade inventory in a simple and straightforward way.
To start with, don’t display too many products. You don’t want to confuse the customer. First determine your primary customer base and what blades would best serve them and then go to work on making sure your customers are aware of what blades you have to offer.
While it can go a long way toward assisting your customers with blade selection, an effective display is still only half the battle. Your counter staff really needs to be well educated to ensure your customers leave your store with the right blade for their job.
Before an employee can make the right recommendation to your customers, he or she needs to understand the basics of diamond blades.
Between a rock and a hard place
While it seems counter intuitive, the general rule of thumb for blade selection is simple: hard blades cut soft materials and soft blades cut hard materials.
To understand this, it is first necessary to understand fundamental blade composition and how a blade works.
A diamond blade is simply a circular steel disc with a diamond bearing edge, says Thom Fisher with Diamond Products. The edge or rim can have either a segmented, continuous or serrated rim configuration.
Diamond segments or rims are made up of a mixture of diamonds and metal powders, explains Fisher. The diamonds used in blades are synthetic and are carefully selected for their shape, quality, friability and size. These are then mixed with a powder consisting of metals such as cobalt, iron, tungsten, carbide, copper and other materials. This mixture is then molded into shape and then heated under pressure to form a solid metal part called the bond or matrix.
Contrary to popular belief, diamond blades do not actually “cut,” they grind. Exposed diamond crystals in the bond or matrix do the grinding work. As the blade rotates through the material, the exposed surface diamonds grind the material being cut into
a fine powder.
After several thousand passes through the material being cut, the exposed diamonds begin to crack and fracture. The matrix holding the diamond also begins to wear away. Eventually, the diamond completely breaks up and its fragments are swept away with the material that it is grinding. As the old diamonds are worn down, they are replaced by new ones and the process continues until the blade is worn out.
Knowing this, it makes sense that harder aggregates, such as flint, chert, trap rock and basalt, will break down diamond crystals faster, so it’s necessary to use a softer bond to expose new diamonds. Likewise, softer aggregates, such as limestone, do not break down the diamonds as fast, so it requires a harder bond to hold the diamonds in place in order to use their full potential.
“The application of a diamond blade to the material cut is a relationship that matches the abrasion resistance of the diamond segment to the abrasiveness of the material cut,” explains Gabriel Uriegas with Saint-Gobain Abrasives, makers of Norton and Pro-Cut blades. “Simply stated, hard blades for soft materials and soft blades for hard materials.”
Factors affecting performance
According to Fisher, how a blade performs has much to do with what is being cut, so it’s important to ask your customer what they plan to do with your blades. He points to some of the factors affecting performance:
Compressive strength — Concrete can vary greatly in compressive strength, which is measured in pounds per square in. (psi). Most concrete roads are approximately 4,000 to 6,000 psi, while typical patios and sidewalks are about 3,000 psi.
Size of aggregate — Larger aggregates tend to make a blade cut slower, while smaller aggregates tend to allow a blade to cut faster. The most common aggregate sizes are: Pea gravel (usually less than 3/8 in. in diameter), 3/4-in. (sieved size) and 1-1/2 in. (sieved size).
Type of sand — Sand is the component of the mix which determines the abrasiveness of the concrete. Sand can either be “sharp” (abrasive) or “round” (non-abrasive). Crushed sand or bank sand are usually sharp; river sand is typically round.
Hardness of aggregate — There are many different types of rock used as aggregate. Generally, hard aggregate breaks down the cutting diamonds faster, which means the bond must be softer to expose new diamonds. Softer aggregate generally does not break down the cutting diamonds as quickly and so needs a harder bond to hold the diamonds in place.
Reinforcing steel — Steel reinforcing tends to make a blade cut slower. Heavy rebar can also result from different grades of steel. Typical rebar is grade 40, but grade 60 is also common. Rebar gauges are in eigths of an in.; #4 is 1/2-in. diameter, #5 is 5/8-in. diameter.
Green or cured concrete — The drying or curing of concrete greatly affects how the concrete will interact with a diamond blade. Green concrete is freshly poured concrete that has not yet cured. It is softer and more abrasive than cured concrete. A harder bond with undercut protection should be used in this application until the concrete is cured, at which point a softer bond would be appropriate. The definition of green concrete can vary widely. Water, temperature, moisture in the aggregate, time of the year and the amount of water in the mix all influence the curing time. It is generally considered “green” for eight to 48 hours after it has set.
Wet vs. dry
The use of water as a cooling agent is common in blade applications. According to Uriegas, wet-cutting blades are generally used to cut very dense or extremely hard materials. “The water serves to keep the blades cool and flush the fine particles out of the cut,” he says, noting that “slurry created when wet cutting can stain a surface if left to dry. The desire to leave a clean surface and reduce the need for pressure washing makes the use of dry cutting blades for green concrete joint cutting applications a better choice.”
Dust suppression is also a common reason to use wet-cutting blades. “Wet cutting in masonry applications is a preference when the cutting location is near an area that does not allow the dust to settle before coming in contact with people or equipment,” says Uriegas.
Quality counts
As with anything else, you get what you pay for when it comes to diamond blades. There are more and more economy blades coming into the marketplace today, causing rental businesses to sell more blades than rent them, but high-quality diamond blades are less expensive now than they used to be, and if used properly, can turn a profit quickly. But what are the hallmarks of a premium diamond blade?
“Bond hardness, diamond size, diamond content and diamond quality are some of the key components that determine the performance of a diamond blade,” says Uriegas. “The quality of the individual diamond determines how long the diamond will hold a sharp edge and the ability of the diamond to produce a consistent sharp edge. It is not uncommon for the premium diamond blade to contain a very high-quality grade of diamond suspended in a metal bond that will maximize the cutting edge for a specific diamond size.”
So, the primary differences between premium and economy diamond blades are diamond quality and/or quantity. “The amount of diamond in a blade will change the cutting performance, assuming all other components that make up the segment remain the same,” says Uriegas. “In general, increasing the amount of diamond slows the cutting speed and extends the cutting life of the blade. Consequently, reducing diamond content will increase the cutting speed and reduce the cutting life of the blade.”
Premium blades also frequently employ features that extend their cutting life. For example, wet-cutting blades can feature slanting segments on the core or carbide inserts in the spaces between the segments to minimize the undercutting that results when wet cutting abrasive material. Dry-cutting blades, on the other hand, sometimes use a specific steel core geometry to flush particles out of the cut. Placement of the segment on the steel core and segment geometry reduce the vibration on dry-cutting, high-speed diamond blades, Uriegas says. The reduced vibration results in blades that cut faster and last longer by dampening the hammering and wobble that normally occurs with standard segment and steel core geometry.
All other things being equal, sometimes the choice between premium and economy comes down to your customer base. Since operator misuse can be a significant factor in the rental setting, sometimes it makes sense to rent a customer an economy blade, even though it will wear out faster. If your customer is a seasoned professional, however, premium blades might make more sense because they last longer and perform better over the long haul.
In the end, it all comes down to education — for your employees and your customers. Arm your staff with the right information so they can take the confusion out of blade selection for your customers.