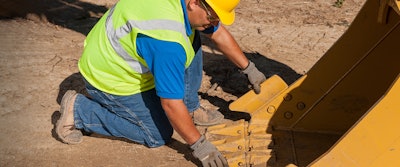
This blog was updated on 6/6/2023.
Here’s a question we get a lot: What percentage should I allocate for equipment maintenance? Unfortunately, there’s no magic number you can plug into your spreadsheet — it differs for every operation. But here are some quick tips for landing on a percentage that’s right for you.
Be Comprehensive. Include Planned Maintenance and Repairs.
A good rule of thumb is to start at each machine’s blade or bucket, work your way back to the rear counterweight or ripper, and consider every maintenance item (planned and repairs) in between. You can generally fit your expenses into these categories:
- Consumables: This bucket covers most of what you think of when it comes to maintenance: fluids, filters, belts, hoses and the like.
- Major replacements: Items like tires and ground engaging tools (GET) can get overlooked because they may not be regular maintenance items for some operations. Make sure you add these bigger expenses to your budget if necessary, so you’re not hit with surprise costs down the road.
- Lifecycle repairs: Do you know how long you plan to keep each machine you operate? If so, it’s smart to factor in maintenance and repairs you know will occur in the future — at 10,000 or 15,000 hours, for example — and amortize the costs over time.
Don’t Just Forecast. Track.
Forecasting is great, but using historic data will get you closest to an accurate budget number. Add up the cost of parts, materials and labor — everything you put into a machine post-purchase — then divide the total by the number of hours that machine has run. That will give you a percentage to allot for maintenance. It also gives you a number you can work into your bids, so you get the best return on your equipment investment.
Factor In Unique Jobsite Conditions.
Dust, materials, altitude, temperature — every jobsite is different, and different factors affect maintenance (and budgeting) in different ways. Do you operate in a cold-weather area? It’s not uncommon to have to switch out lubricants between summer and winter, an added expense. Are your machines digging in granite versus limestone or sand? If so, you probably need to budget more for GET.
Take Advantage of Maintenance “Cost-Reducers.”
Good news: There are plenty of proactive moves you can make to reduce your maintenance budget. One simple step is to work with your equipment dealer to streamline the process. Look into kits that can save you money (and time) by eliminating the need to buy parts one at a time. Ask about parts delivery guarantees (like those included in some Customer Value Agreements) and parts drop boxes. Take advantage of fluid analysis, regular inspections and machine telematics to identify and address issues before they become catastrophic repairs.
This blog was updated on 6/6/2023.