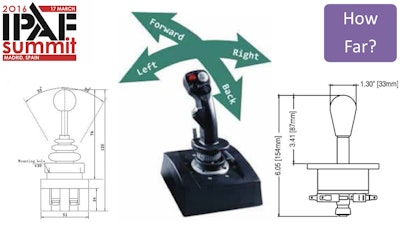
Seasoned operators of aerial work platforms (AWPs), also known as mobile elevating work platforms (MEWPs), sometimes wonder why the controls don’t function from machine to machine in a more similar, consistent way.
The control panels can vary in terms of shape, control layout, function actuation, indication and marking, to highlight just a few areas as manufacturers have updated and changed designs.
The quest for consistent human-machine control interfaces, which is a standing challenge across most industries, has gained increased relevance in the aerial equipment sector.
A joint group from the IPAF Manufacturers’ Technical Committee and the Association of Equipment Manufacturers (AEM) MEWPC, working in partnership with the UK-based Health and Safety Executive (HSE) and Health and Safety Laboratories (HSL), completed its review of human factors and ergonomics in January this year.
“Manufacturers wanted to ensure the latest knowledge in terms of control placement, operational ergonomics and human factors, including those found in other industries, were adapted and incorporated for AWP/MEWP design standards,” said Philip Godding, Principal Product Safety and Reliability Engineer, JLG, and chair of the IPAF Manufacturers’ Technical Committee. “While we demonstrated that there was an organic trend towards consistent function operation, this was an opportunity to evaluate the relevance of the latest thinking and to seek global consistency for future products.”
This groundbreaking collaboration produced a framework for reviewing state of the art human factors and ergonomics in the use of AWPs/MEWPs. It has also led to the development of the first global draft standard for MEWPs to consider control function consistency. The aim of all this is to achieve consistent controls performance in order to improve operator safety by reducing the likelihood for human errors where possible. The research identified design as but one factor in minimizing the risk of incidents when using MEWPs.
“The outcome of this project tells only part of the story, as manufacturers worked in partnership on an accelerated timeline,” Godding elaborated. “Had this work not been prioritized and followed a more traditional review process, it is likely that development of this draft would have taken a further three to five years.”
The new draft international standard ISO 21455: “Mobile elevating work platforms – Operator’s controls – Actuating forces, displacement, location and method of operation” is now under review and comment by the International Organization for Standardization (ISO) Technical Committee 214 for elevating work platforms and its Working Group 1 for mobile elevating work platforms, TC214 WG1.
This standard aims to clearly define control performance criteria and introduce additional human factors/ergonomic elements for controls used on MEWPs. It focuses on the areas of control location, function, movement, layout and markings. This draft is in the early stage of development and should be completed within three years.
What does this mean for end-users? The new draft ISO standard is about developing compliance requirements for protection that meet the expectations of users and about developing performance criteria that can be applied to all MEWP control designs where no previous standard existed, said Brad Boehler, president of Skyjack, presenting a review of this work at the IPAF Summit.
He said, “It’s about addressing the questions: Where? How? How hard? How far? – Where are the controls located? How are they activated (forward, back, push, pull)? How hard do you have to push it? How far will the machine go (forward, back, left, right)? How should different actuators be evaluated, whether push-button, joystick, touch-screen?”
The draft standard is a first of its kind for the industry in bringing consistency to where controls are located and how they are activated.
Chris Wraith, IPAF technical & safety executive, said: “We should not lose sight of the aim of standardizing MEWP control design and functionality to improve safety, but this must be done without smothering the ability for design innovation. Take the automotive industry – Cars have key controls that are the same in all models. Foot brake and foot accelerator are always in the same sequence and position. But indicators, windscreen wipers and lights may be located in different positions, even the sequence of gears may be different.”
On the question of what percentage of accidents could be attributed to controls and errors, Boehler said that these could be traced to a multitude of factors.
“The causes of the accidents analyzed were less about control position and ergonomics, and more about what operators do in specific work environments,” he said. “The draft standard is about defining where controls are located in an expected space, the directionality of controls, and force, ensuring any ambiguity of operation is reduced as much as possible.”
Does this mean that AWPs/MEWPs are now going to operate the same way? No, and they never have, said Chris Wraith.
He explained: “While the trend is towards standardization and internationalization, most standards are written in ‘descriptive’ language as opposed to ‘prescriptive’ language. This allows manufacturers to introduce new innovative features and designs while still complying with the standards. It provides opportunity to consider advances in technology and allows continual product development, something prescriptive standards would stifle.”
Wraith stressed that familiarization is the key. Professional training is essential. But on top of that, managers must make sure specific machine familiarization takes place for all operators. Operators should ensure that they are familiarized with each specific machine prior before use.
To be safe, never assume similar machines operate the same. Always make sure that you know and understand the specific features of the AWP/MEWP you are operating at all times.
See IPAF’s technical guidance F1 on familiarization at the Publications/Technical Guidance section of www.ipaf.com.