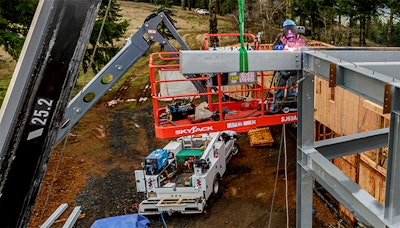
Jobsite welding and repairs can throw a variety of challenges at operators. Having the right equipment and capabilities is essential to getting jobs done efficiently and keeping projects on track.
Including remote control solutions that save time and improve jobsite safety and fuel-saving options that reduce costs, the right technology can make your contractor customers more efficient on the jobsite. Today’s welder/generators offer features that help contractors meet their goals, budgets and timelines.
What technologies and capabilities are your customers looking for when they rent engine-driven welders/generators for the jobsite? Consider these six features and technologies that can help your contractor customers reach their goals.
1. Remote control solutions
The need to frequently adjust weld settings or switch between welding processes can be a hassle when operators have to walk back to the welder/generator each time to make changes or turn the machine on and off. Welding power sources with remote solutions make it easier and faster to make the needed adjustments—like having the front panel in the palm of the operator’s hand.
By using remote pendants or wire feeders that communicate back to the power source, operators can easily adjust weld settings and switch between processes right where they’re working. This saves significant time and money, particularly on large jobsites with many tasks and workers. Not only does it take time for operators to walk back to the power source, but it also increases potential slip, trip and fall hazards when operators must make their way across a jobsite each time they make adjustments to their machine setting. Remote controls also help ensure that operators have the correct parameters for every weld, rather than trying to make do with less-than-optimal settings.
1. Wide range of capabilities
On the jobsite, operators may need to go from stick welding to wire welding to gouging, depending on welding procedures or the application they are working on.
Many field applications rely on the carbon-arc gouging process to efficiently remove metal. Look for a welder/generator that has a dedicated CC gouge process, which optimizes the arc for gouge applications. A dedicated gouge mode enables operators to continuously perform high-quality gouging with a more responsive arc.
Over the past several years, more regions are adopting wire welding, which can save hours or even days of time on big jobs compared to stick welding. Choose feeders and power sources with technologies that make use of point-of-work voltage control to make fine-tuning the arc easier on the operator.
3. Fuel-saving technologies
Less money spent on fuel means more profit for contractors. Welder/generators that have additional fuel-saving technologies help reduce fuel consumption and costs on the jobsite.
Another way to improve fuel efficiency and maximize profits is to choose a welder/generator with electronic fuel injection (EFI). This technology provides faster, more reliable starts in any weather and delivers up to 42 percent greater fuel efficiency.
4. Dual-operator capabilities
An engine-driven welder/generator with dual-operator capabilities is a tool that offers the versatility to accomplish what contractors need to get work done on today’s busy jobsites—with one machine meeting the needs for many different jobs.
With a dual-operator solution, multiple workers can use one machine simultaneously for welding, cutting or operating lights or grinders, which saves space on a crowded jobsite. Welder/generators with dual-operator capabilities not only provide enough power for the two onboard welding arcs, but they also deliver enough power to operate additional inverter-based welding power sources. Weld controls and auxiliary power are completely independent for each arc, and the operators can weld and operate a wide range of tools using the auxiliary power with no impact on arc quality.
These machines also can provide a financial payoff in the long run, since one engine uses less fuel and requires less maintenance when compared to operating several engines.
5. Noise reduction
On many jobsites, there are welders, generators, air compressors and tools being used. This may seem like business as usual and just part of the job, but all this additional noise can make it hard for workers to communicate. On some jobsites, like those in residential neighborhoods or near schools, reducing noise may be required to stay within local ordinances.
Some technologies reduce jobsite noise by utilizing reduced engine speeds, so the engine isn’t always running at the highest speed and generating the highest level of noise. Also, consider technology that lets operators turn the unit on and off remotely. This helps reduce jobsite noise—eliminating the noise of the machine running when it’s not in use—and also saves fuel. The average welder/generator is only used about 30 percent of the time it’s running, meaning that up to 70 percent of the time it could be turned off.
6. Front panel lockout
On busy jobsites, contractors often have many welding power sources staged in the same area. Sometimes an operator or a welder’s helper accidentally makes adjustments on the front panel of the wrong welding machine—unintentionally causing problems by changing a different operator’s settings while not making the intended adjustment to their own machine. To avoid this hassle, look for an engine drive and accessory that will lock out any changes on the machine interface once the two have been paired. This prevents accidental changes that can result in rework or poor weld quality.