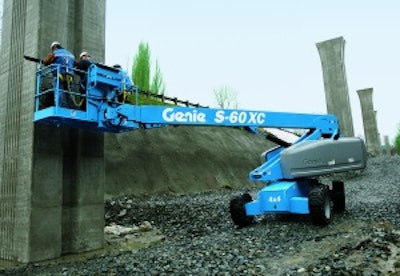
If you've been renting aerial lifts for any length of time, you probably know what information to give rental suppliers and what questions to ask to get the right equipment for the application. On the other hand, if you're a first-time lift renter, or use them only sporadically throughout the year, getting the exact aerial platform to meet your needs can be tricky.
How high will you need to reach? What are the jobsite conditions? Will you be working inside or outdoors? These are just a few questions that require answering before picking up the phone or trekking to the rental center. There are others, as well, including critical information about how you plan to use your aerial lift once on site. The following are a few suggestions from manufacturers, rental suppliers and contractors that can help you select the right equipment from both a productivity and safety perspective.
Narrow Down Your Needs
"The first issue contractors need to address is how they intend to use the unit," says Frank Schneider, Terex AWP product manager, Genie Booms. "Changing a light bulb in a parking structure requires a much different lift than installing exterior glass plates on the fifth floor."
Answering three questions will help narrow your renting decision. "First ask: 'Where will the work be performed?' This tells both the height requirement of the lift and model needed," Schneider indicates. "If the work is to be done overhead, then a vertical lift would be in order. A telescopic lift would be needed for outreach applications, and an articulating boom would be best suited for obstructed work areas.
"Second, knowing how many people and what tools and equipment are required to get the job done will indicate platform requirements including capacity and need for AC power," he continues. "Finally, will the work be indoors or outdoors? Indoor applications call for an electric or propane power source and fixed-axle or 2WD units with non-marking tires. Outdoors generally calls for a diesel or gas power source, oscillating axles and 4WD, and RT tires."
"Consider the total work area and any constraints or limitations, e.g., where the machine may not fit or be able to maneuver," adds Jeff Weido, Terex AWP product manager, Genie Scissors. "Look at lift weight, as well. Since contractor weight estimates will likely be low, if the job calls for lifting 1,000 lbs., then a contractor should consider a machine that can lift 1,200 to 1,500 lbs. This ensures maximum performance."
Be Work Specific
After deciding on the type and size of machine, take a close look at the type of work to be performed from the platform.
"Today's leading manufacturers offer a variety of options that will increase productivity. Welders, plasma cutters, saws, pressure washing systems and lighting packages all can be powered by built-in generators and electric cable and air/water lines running through the boom to the platform," explains Jim Hindman, spokesperson for JLG Industries. "Using these integrated tool systems increases productivity, eliminates the need for costly ancillary equipment and, by eliminating wires and hoses running over the side of the platform to the ground, provides a much safer working environment."
Avoid making generalizations about applications when renting a lift, emphasizes Eric Eccles, general manager of RSC Equipment Rental, Tucson, AZ. "Mechanical contractor customers, for example, often have large, bulky items in their baskets. This application requires a wide scissor rather than a 32-in. narrow unit that would normally be used for getting into confined areas.
"Similarly, insulation contractors often want RT (rough-terrain) scissors even though they are working inside," he notes. "This allows workers to store large bundles of insulation in the basket. The more they can carry means fewer trips to the ground to reload and ultimately more productivity."
Details, Details, Details
Eccles stresses that details associated with the jobsite and work requirements are just as important as the big picture application. He gives these examples:
Building access. A standard door is 34 to 36 in. wide. An electric scissor lift typically comes in 32- and 46-in. widths. Without a double door for access, the operator will not be able to get the wider lift into the building.
Available power. An electric scissor lift should have enough battery power for an 8- to 10-hour day. However, batteries require eight hours of constant electricity to fully recharge while the unit is not in use. Often, new jobsites have temporary generators that run only during working hours, giving you little or no opportunity to charge the lift.
Working height. Understand the meaning of working height. For example, a contractor may ask for a 25-ft. scissor lift to accommodate a 25-ft. working height. In reality, a 19-ft. scissor lift with a 6-ft.-tall person in the basket would reach the same height and be 35% less expensive. Also note that an electric lift will not go above 6 ft. on any uneven surface.
"Access to the working area is also important," adds Eccles. "A contractor working in a ceiling grid or in between piping or other mechanical fixtures may discover that a full-length scissor will not fit into the overhead working area. A single-person personnel lift with a smaller, narrower basket would be a better option."
Be detail oriented when inspecting the jobsite terrain, as well. As Hindman relates, a four-wheel-drive unit or one with a crawler undercarriage might be required for soft or muddy conditions. Sloped sites may need a machine with more gradeability, and those with scattered debris require machines with higher ground clearance.
And keep in mind you have plenty of tire options to suit conditions. "[You] can select traditional pneumatic tires or go with foam-filled tires to avoid flats," Hindman points out. "High-flotation tires work best in certain turf situations, and solid, non-marking tires are designed for use on wood flooring or tile and marble surfaces."
Safety First
Operator experience is critical, states Dale Roesener, senior vice president of H&E Equipment, Las Vegas, NV. "The aerial lift operator needs to be trained on equipment for both safety and productivity reasons. If the operator is inexperienced, make sure to ask the rental store for training."
If there is uncertainty about site conditions that could present a safety issue, bring that to the rental store's attention, adds Danny Tittle, a purchaser for Tucson-based Kazal Fire Protection, and an RSC customer. His company uses a variety of lifts to install fire protection equipment in new construction and to service older systems.
"Most of our new installations require working on pavement," he says, "although at times the jobsite will call for an all-terrain lift. There are occasions when a small articulating lift will be needed to work around desks to repair an older system.
"One of the chief concerns when renting any lift is safety," he states. "If we're unsure about the type of lift we need, someone from RSC will come over and inspect the site to ensure the machine fits the application."
Weido offers two additional safety tips for operating scissor lifts. "Anytime a scissor lift is used outside on an uneven surface, we recommend the use of outriggers for additional support and stability," he says. "Another consideration is floor loading specifications for multi-storied buildings. Always be sure that the aerial lift floor loading specifications fit within the floor loading limits of the jobsite."
Rent vs. Own
Stark Electric performs a variety of lift applications, from running conduits inside buildings and lifting transformers outside, to unloading switch gear from trucks. "We may use scissor lifts or boom lifts, depending on the application," says Chad Lynn, estimator. "Some applications are on concrete and others are off road."
The range of applications, in combination with the service it receives from RSC, encourages Stark Electric to rent vs. owning lifts. "RSC maintains the equipment and is very prompt if a machine goes down; they will come out and swap it out immediately," says Lynn.
"Having several different applications is one of the reasons so many of our customers rent," asserts Roesener. "Contractors who rent, though, have to be assured about delivery time. A lift that shows up two hours late on a job translates into costly downtime."
According to Schneider, three factors greatly affect the decision to rent vs. buy: the availability of the desired configuration, rental rates, and length of intended use. "Certain machine configurations are rare and may require purchase since they won't likely be found in the typical rental fleet," he elaborates. "Even though current rental rates favor renting, if the intent is to use the machine for an extended time, then the purchase option would likely be best."
Today's market, however, doesn't favor owning from a continuous-use standpoint, Eccles asserts. "Fifty nine percent of our scissor lift rentals are for less than one week. The average weekly rental on a scissor is $240 with $65 delivery and $65 pick-up. Service on the unit and available exchange in the event it fails on the job are included in the rental fee. So the weekly rental cost comes to $370," he notes.
"If a contractor doesn't have his own transport, it can cost upwards of $100/hour for transport to and from the jobsite, not even considering the maintenance costs if that, too, is contracted out," he continues. "Often, contractors have two or three short-term projects, and owning a unit would multiply transport costs. The alternative would be to own a couple of lifts, one for each job. This would tie up capital dollars on equipment that would only be partially utilized."
The drill is the same whether a contractor is renting a unit or buying one, says Hindman. There's a lift for every application, thanks to the wide variety of products on the market today. Reviewing needs, looking at jobsite parameters and asking the right questions before selecting a machine can save, in his words, "a whole lot of time and trouble on the job."