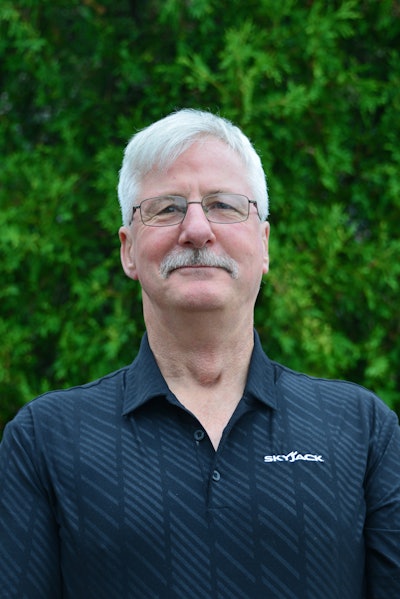
Few would argue that a jobsite risk assessment is a good idea before performing work in a mobile elevated work platform (MEWP). Working at height comes with its share of inherent risks, so it’s vitally important to be aware of the potential hazards that exist on every job and take appropriate action to eliminate or mitigate them. But how many are actually performing this important process? What does it even entail? One thing’s for sure, the new ANSI standard expected to be released this fall requires a risk assessment on every use of an MEWP, beginning with operator training. We asked a panel of industry experts about what this will mean to construction professionals. Following is an excerpt from that discussion.
Jenny Lescohier, editor, IPAF Elevating Safety: What exactly is a risk assessment?
Tony Groat, manager, IPAF North America: A safety risk assessment is a systematic procedure for identifying and managing hazards. It requires a thorough examination of the entire work environment, processes and equipment to determine if there is any potential for harm to the health of the employees in the short or long term, and if there is, how can the situation be remedied. It focuses on the relationship between the worker, the task, the tools and the work environment. Ideally, after you identify uncontrolled hazards, you will take steps to eliminate or reduce them to an acceptable risk level.
Lescohier: What are some of the known potential hazards that should be addressed during a risk assessment?
Tom Retano, construction safety consultation coordinator, CT Department of Labor – OSHA Division: The FOCUS Four (Falls, Struck by, Caught in/between, and Electrical) hazards at a minimum. The ANSI and CSA industry standards provide a detailed list of issues that must be considered prior to and during MEWP operations that contribute to risk associated with the FOCUS four.
Lescohier: Even without the new ANSI standard, shouldn’t a risk assessment be performed prior to all work anyway?
Brian Downham, product safety trainer, Skyjack: OSHA requires it in its General Duty Clause, which states that each employer shall furnish employees with a work place free from recognized hazards that can be likely to cause physical harm or death.
Retano: I’m not aware of a better general tool than a Job Hazard Analysis (JHA); an administrative control for evaluating and reducing hazards that cannot be eliminated through engineering controls.
Marko Kaar, director of safety operations at Bartlett Brainard Eacott: There are many regulations that can be interpreted to mean you have to do a risk assessment, but this verbiage as its written is much more specific in its expectations and almost creates a checklist. There are different working environments, different equipment being used and different hazard exposures in every case, but the more you can boil this down to a checklist-type format, the more easily communicated it will be, and the more effective it will be.
Lescohier: Is there, in fact, a checklist or anything people can glance at to make the risk assessment process simpler?
Groat: There is the list of issues that the safe-use standards define and guidance in the industry to consider, but it’s important to note that you really need to have a qualified person to perform a risk assessment. You can find sample forms for risk assessments from industry associations like IPAF or web searches, but job-specific hazards must always be part of the analysis.
Lescohier: Who’s qualified to do a risk assessment?
Retano: It’s always been my opinion that a supervisor is responsible and accountable for the safety and health of his or her employees. They should be able to do any task assigned to those employees. They should also be better educated in the tasks their employees are trained to do. OSHA’s definition of a “Competent Person” comes close to saying that a “Competent Person” (anyone designated by the employer to stop work to remove employees from hazards, implement controls for those hazards, be knowledgeable of the hazards related to the work) should be qualified to perform a risk assessment. Sadly, that is not the norm.
Lescohier: How difficult is it to perform a risk assessment?
Groat: A risk assessment can be a very simple and routine process that can occur in a short amount of time based on the complexity of work. Changing a light bulb vs. building a high rise will require a different amount of time. But the fundamental processes are the same.
Lescohier: How will MEWP operators benefit from risk assessment?
Downham: When hazards have been identified, controls can be put in place to help prevent incidents or accidents. It improves the safety of the working environment as a start.
Groat: A MEWP operator is a tradesman who is trained to operate a MEWP to access their work. They generally do not select the MEWP being used, and simply show up to perform a task. Obtaining knowledge from a risk assessment developed prior to work by a qualified person provides the operator with clear understanding of the potential hazards on site and the means to avoid the risk from the hazard. They are prepared to work safely and efficiently.
Kaar: There’s also an intangible peace of mind component to risk assessment that’s important for the operator. That peace of mind comes when the operator knows that someone is actively looking out for them, and has done everything they can to reduce risk.
Lescohier: What’s the danger of a risk assessment not being completed?
Downham: If a risk assessment is not completed, there’s always going to be a greater likelihood that hazards are not identified and the risks are not controlled through the job planning.
Groat: All work at height involves the potential hazard of a fall. While workers might be fortunate when a task can be completed without issue, if a risk assessment is not done, the chance that a hazard will be encountered and result in serious injury or death is dramatically increased. And the wide range of working sites and conditions this equipment can be working in further increases the probability that without proper due diligence, the likelihood of an accident is much greater.
Kaar: Liability is another factor that should be considered. We’re often thinking about physical hazards but not about things like public notoriety (you have an accident and your company’s name is in the paper) and law suits that can go on for years. If you’ve done a risk assessment that says you’ve identified physical hazards, it could protect not only the operator but the company from liability as well.
Lescohier: How does risk assessment adapt to changes on the jobsite?
Downham: Worksite inspections should be always ongoing, and the operator is in the best position to identify something that’s changed. At that point, he or she should go to their supervisor or competent person who can then determine if there’s any potential hazard and put any necessary control measures in place.
Kaar: That’s where the planning process often fails. Too often we don’t circle back on changing conditions and different applications. It ought to be done every day before we use the MEWP.
Retano: Specific to hazards, the risk assessment should be a part of any change analysis. Risk assessment is incorporated into many programs and standards addressing safety and health, including but not limited to ISO 14001, the new ISO 45001, “Safety by Design,” and many others.
Lescohier: How often are risk assessments really being done right now?
Kaar: Many larger contractors with ample resources are doing it, and in many cases, it’s the project owners who are driving the process. But we’ve got a million MEWPs in the workforce now, and I’m convinced that the vast majority do not have a daily plan. There’s attention paid to it, but it’s not happening nearly as frequently as it should. Having a standard mandate the process can help increase the frequency of use of this effective risk management process.
Retano: There is great disagreement in the world of subcontractors on what it means to survive or thrive as a company. Many don’t embrace a safe and healthful culture as a means to increase profits. That’s why OSHA and ANSI standards have been developed and continue to be developed. Depending on insurance to control safety and health is reactionary and the cost of that dependence is human lives. Risk assessment is a proactive process not recognized by typical subcontractors as critical to the bottom line.
Lescohier: Why is there such resistance?
Downham: It could depend on a lack of site controls or the time needed to complete the task, but it could also be a lack of awareness of the need for a risk assessment and the benefits it can offer.
Kaar: There’s always an internal cost/benefit analysis being done by individuals on a daily basis. Some believe it’s a waste of time to plan because they know what they’re doing. That being said, there are general contractors and construction managers who figure they’ve transferred their risk contractually, so they don’t need to babysit workers. They think, “If something happens, I’m covered through my contract language; they’ve agreed to follow all rules and regulations. I don’t need to implement another time-consuming process.”
Groat: Owner/operators working 15-hour days are most likely not taking the time. As always, our strength is our weakness: We find a way to get things done, but… do we find a way to get things done safely? And the more they get away with doing things the wrong way, the more it becomes an acceptable practice.
Lescohier: The new standard requires a rescue plan. What’s the value?
Groat: During an emergency is no time to be trying to figure out the most effective way to get an individual down from a MEWP at height. The rescue plan puts planning in place so when a situation arises, you have adequate guidance and instructions to take care of the emergency safely and effectively.
Lescohier: Can calling 911 suffice as a rescue plan?
Groat: No. Are emergency services qualified to rescue at height? Can they reach at the heights that some MEWPs can travel? Do they know how to operate a MEWP to lower it? Emergency services might be a component, but it is not the entire plan.
Retano: As has been said in the preamble for Confined Space Rescue, depending on 911 as a rescue will probably be no more than “body retrieval.” The best rescue is a self rescue. In the absence of that, trained workers on site that can effect a rescue of an MEWP occupant will probably be the most effective rescue.
Lescohier: What’s the big picture goal for the risk assessment requirement in the new ANSI standard?
Groat: There’s great value in performing a risk assessment. Supervisors can use the findings of a job hazard analysis to eliminate and prevent hazards in their workplaces. This is likely to result in fewer worker injuries and illnesses; safer, more effective work methods; reduced workers’ compensation costs; and increased worker productivity. The analysis also can be a valuable tool for training new employees in the steps required to perform their jobs safely.
While we’re talking about risk assessment under the umbrella for MEWPs, the concept really applies to all equipment and all types of work on an ongoing basis. We’re mandating the discipline so it will become a more consistent practice that occurs every day on every job, with the goal of improving overall work safety.