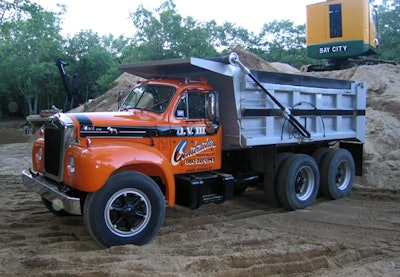
With Equipment Today celebrating over 50 years in publication, we decided to look at the evolution of the heavy-duty vocational truck market.
“We’ve seen so many advancements in Class 8 vocational truck technology over the past 50 years (see also 50 Years of Equipment Impact: Heavy Truck Brands Consolidate) that it’s tough to find a place to start,” says Curtis Dorwart, Mack vocational products marketing manager. “Radial ply tires, anti-lock brakes, automated transmissions, power steering, air conditioning — the list goes on.
“Trucks were a lot simpler, and at the same time, much harder to drive 50 years ago,” recalls Dorwart. “I started in this business 35 years ago in the shop, and there were many 1960s vintage trucks still working. They were fun to work on and pretty straightforward in their design. But back in those days, having to do some sort of internal engine repair or rebuilding was not uncommon around the 300,000-mile mark, or sometimes much sooner.”
Engine durability has since improved dramatically. “What set the stage for the ‘million mile’ engines that are more commonplace today was the introduction of electronic fuel controls in the late 1980s and early 1990s,” says Dorwart. “Initially, it was tough for some to see the simplicity of the mechanical jerk pump, unit injector and pressure-time fuel systems that were commonplace 50 years ago replaced by electronic controls. But the electronic controls set the stage for longer engine life and oil life and better fuel efficiency, and the emissions control systems have delivered measurable and positive impacts on clean air. Gone are the days when a big puff of black smoke between shifts was an indicator of ‘good power.’”
The electronic revolution had a profound impact on heavy truck development. “Electronics have dominated advances in vocational trucks over the past half-century,” says Mark Howerton, product marketing manager, vocational trucks and alternative fuels, Freightliner Trucks. “These advances are in nearly every part of the truck and chassis — from powertrain controls to data buses to diagnostic and telematics systems. Electronic systems have made vocational trucks better optimized for specific applications and easier to diagnose and service, resulting in greater fuel efficiency and increased productivity.”
Power Density Increases
Changes to the diesel engine resulted in substantial performance gains. Fifty years ago, there were a few gasoline engine options still available in the heavy-duty vocational truck market. But by the end of the ’60s, diesel engines, with their favorable torque curves, replaced the gasoline options and still dominate the Class 8 vocational truck market. In the last decade, natural gas has also made inroads in certain applications where the infrastructure makes sense, such as ready-mix fleet trucks that return back to the yard every evening.
50 Years of Equipment Impact: Five Decades of Diesel Engine Evolution
The amount of power produced for a given displacement engine has increased substantially over the past 50 years. Consider a 1965 Mack that was powered by a 14-liter Cummins NTC335 turbocharged diesel engine that pumped out 335 hp at 2,100 rpm. A current Mack MP8 diesel engine is 13 liters and pumps out between 415 to 505 hp with torque ratings from 1,460 to 1,860 ft.-lbs. These gains mean smaller and lighter engines can be used in many applications and more power is available for the most demanding applications.
This trend continues through today. Engine technology has changed a lot in the last five to six years, with significant changes in horsepower and torque curves. A 13-liter built correctly and with the correct power band is able to do the job of the majority of 15-liter engines.
These recent developments have been accelerated by the advent of emissions and fuel economy regulations. While the diesel engines evolved steadily through the ’90s, it was really legislation promulgated by the EPA to limit on-road diesel engine emissions that sparked a technology revolution, although not without a substantial cost to the industry.
This cost is not only in the purchase price of the vehicle, but also in increased complexity. “A lot of operations that used to service their own equipment are finding it too expensive and difficult to maintain the same level of in-house capability they had even 10 years ago due to the specialized knowledge and tools required to diagnose and repair modern trucks and powertrains,” says Dorwart. “There’s also the real (and potentially worsening) shortage of competent technicians and drivers.”
Diesel engine emissions regulations were phased in from 2001 to 2010 and resulted in over a 99% decrease in the measured pollutants, mainly NOx and particulate matter (PM). In the first round of regulations, internal- and cooled-exhaust gas recirculation (EGR) systems emerged as the most popular technologies to meet the target emissions levels. U.S. 2007-compliant engines saw the introduction of diesel particulate filter (DPF) technologies along with the EGR. The 2010 regulations ushered in selective catalytic reduction (SCR) technology. The SCR system in conjunction with EGR allowed the engines to be re-tuned for better performance while still meeting emissions targets. But it also came with a steep rise in acquisition cost.
EPA Diesel Emissions Tier Schedule
“Emissions regulations have impacted the buying trends of customers by causing spikes in truck orders followed by periods of slower order intake after regulations take effect,” says Dorwart. “We saw these spikes and slowdowns on either side of implementation of emissions regulations in 2002 and 2007, which brought EGR and EGR cooling, and DPFs, respectively.
“The implementation of 2010 regulations, which saw SCR added to truck engines, impacted body upfitters, who had to adjust their work to accommodate the DPF/SCR systems,” says Dorwart. “These systems also added weight, which reduced payload capacity and productivity for some customers. Despite these impacts and the added complexity of today’s emissions systems, the reliability is getting better all of the time, and it amazes me how clean and powerful the engines of today are.”
There is no doubt that the emissions regulations changed the landscape. “The most significant impact has been the higher costs of product and technology development,” says Howerton. “We’ve seen the growth of in-house drivetrains, and we also went through a period of time where fuel economy numbers decreased as compliant engine technology advanced. Due to the improvements of SCR aftertreatment systems, diesel engines are now more fuel efficient than ever and this improved efficiency is expected to continue.”
With the cost increases, alternative fuels have gained traction. “The evolving federal emissions regulations and efficiency standards — and the resulting changes in engine technologies — have affected the design and cost of vocational trucks. One direct result is the emergence in certain markets of natural gas-powered vehicles as viable alternatives to traditional diesel-powered trucks,” says Howerton.
Another challenge became frame rail space. Real estate previously reserved for body builders now had to compete with the space requirements of the DPF and SCR system. This placed more emphasis on properly spec’ing the trucks for the applications.
Emissions regulations have not stopped there. Now there are greenhouse gas (GHG) emissions standards in place that will drive further changes in the diesel engine market. Regulation targets will be phased in through 2018, with the primary goal of reducing carbon emissions by increasing fuel economy. Many of these gains will need to come through increased powertrain efficiency.
Increased Efficiency and Integration
As the trucks have become more efficient, they have also become more specialized. While in the ’60s there was little difference between over-the-road and vocational trucks, the differences are now quite substantial. Today, trucks for various tasks may look similar to the general public, but they are nearly always optimized for the application. More sophisticated electronics and integrated design make it possible to further customize performance.
All major truck manufacturers have taken steps toward integrated, captive powertrains. Not that many years ago, it was common to spec your preferred brand of engine with your preferred brand of transmission and axles. One truck model could offer three different engine makes and a couple transmission choices.
While you can still order a truck this way, there has been a definite move toward total vehicle integration where the manufacturer offers a proprietary engine, transmission or axle package. The theoretical benefit is a truck optimized for performance and efficiency, with components perfectly matched and seamless communication between the engine, transmission and various truck functions.
“To meet the requirements for cleaner emissions and greater fuel efficiency, getting that half or quarter (or less) of 1% improvement in fuel consumption is a ‘must do’,” says Dorwart. “The best way to do that is to have a total system approach to truck and powertrain design. So having a vertically integrated solution becomes practical, if not downright necessary.”
“Vehicle integration offer significant benefits to the vocational truck customer as high-performance trucks are purpose built and possess a more optimized engineering design,” says Howerton. “As a result of such tight design integration, vocational customers realize a greater return on investment from increased fleet uptime, fuel efficiency and enhanced performance. This performance optimization even includes telematics and safety options through expanded integration with captive drivetrains.”
Electronic advancements have been at the leading edge of vehicle integration. Many manufacturers have moved toward multiplex wiring to add capability, simplify wiring and reduce weight. With a multiplex wiring harness, multiple pieces of information are sent via a single twisted pair of wires vs. a conventional wiring harness where a single piece of information is sent on a single wire for each gauge or control switch. Electrical data such as engine oil pressure or switch functions such as headlamps flow along the same twisted pair of wires. This makes it possible to automate tasks, such as turning on the headlamps when the wipers are turned on.
It also allows trucks to be customized for the application. The Diamond Logic technology offered by Navistar serves as a good example. It enables communication and control between vehicle components and the body. The vehicle and equipment can be protected by creating interlocks, which are operational limits and rules within the electrical system. For instance, you can make sure the air bags are filled up before you take off when you dump the valve to hook up a fifth-wheel; or when the engine speeds reach pre-programmed engine rpm, the PTO will disengage.
Intelligent Communication
Onboard diagnostics and telematics systems have become common on the current generation of vocational trucks. Sophisticated electronics can simplify fleet management by tracking driver performance, monitoring vehicle health, helping drivers navigate the most efficient route, protecting components from driver mistakes and protecting employees on the jobsite by preventing unsafe conditions.
“The use of telematics is already having a major impact on vocational trucks, but those impacts are related to what the telematics solutions can do to optimize the uptime of the truck and the productivity of the driver,” says Dorwart. “At Mack, we are well down the path of proactive management of uptime and other value-added services for our customers through our integrated GuardDog Connect telematics solution, which comes standard on Mack Granite models and TerraPro concrete pumper models.”
“Freightliner has offered the Detroit Connect Virtual Technician on-board diagnostic system on vocational models (114SD, 122SD and M2 112) equipped with heavy-duty Detroit engines since 2011,” says Howerton. “The perception is that remote diagnostics systems are designed exclusively for on-highway markets, but they are relevant to vocational markets, as well.
“Consider the example of a concrete mixer that experiences a check engine light,” says Howerton. “If the driver just pulls over, the load could harden in the barrel or have to be emptied on the side of the road. This costs the fleet money and disappoints the customer. With Virtual Technician, the fleet gets notification of the problem and its severity. If it is what is called a ‘service soon’ fault, we instruct the fleet that the truck can continue driving and that the fault can be resolved at their earliest convenience.
“Virtual Technician instantly identifies the severity of a fault, and eight times out of 10, the vehicle can continue until service can be scheduled,” says Howerton.
Reducing the Workload
Trying to find skilled drivers has become a challenge that has shaped the way truck manufacturers approach the market. Transmission choice helps mitigate potential abuse from inexperienced drivers.
For many years, the simplicity, reliability and low acquisition cost meant the manual transmission dominated the market. But as skilled drivers have become scarce and electronic engines allow better communication with transmissions, there has been an ongoing shift from manual to automatic and automated manual transmissions (AMTs).
Several new AMT choices in the vocational marketplace are providing popular alternatives to the manual transmission. There are a handful of AMTs available in the medium- and heavy-duty truck markets from companies such as Eaton, Mack, Volvo and Daimler Trucks. Allison remains the dominant source of torque converter automatic transmissions, with Caterpillar offering its own version.
“We anticipate that improvements in fuel efficiency will continue to be a trend in vocational trucks with greater acceptance of AMTs, the wider use of lightweight components and smaller displacement engines that deliver more power,” says Dorwart.
How to Select the Best Heavy Truck Transmissions for Construction Use