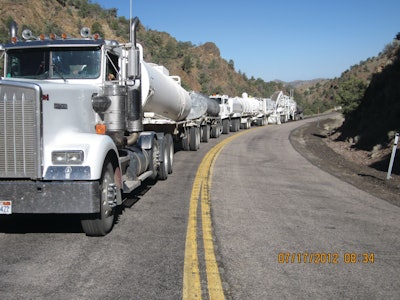
"Our performance with cold-in-place recycling (CIR) has been excellent," says Darin Tedford, assistant chief materials engineer with the Nevada Department of Transportation (NDOT). "In past years we have done more than 50 projects with CIR, and we’ve had minimal issues with construction and minimal failures." He says the main benefit of CIR is to eliminate thermal or fatigue cracking of the asphalt.
CIR refers to the practice of milling an asphalt pavement, then processing the material in a mobile recycling machine that crushes, sizes, rejuvenates and repaves the pavement, all in one pass. As with the example presented here, the Roadtec RT-500 recycling machine can operate either in a mobile mode, as part of a train, or it can be set up as a stationary central plant and do the same processes.
For more than 10 years, NDOT has used CIR on asphalt pavements ranging from low-volume roads to the Interstate. "We try not to spend our small bank account on reconstructing any low-volume road," says Tedford. "So to get rid of cracking we basically use CIR instead of doing reconstruction. We’ll just CIR 2.5 to 3.0 inches and then overlay it with 2 or 3 inches of hot mix, depending on the design."
Value engineering change
Recently NDOT performed CIR on a 16.6-mile stretch of State Route 722, a two-lane road near Austin, Nevada. The state’s original design called for a 2-inch asphalt overlay topped by a double chip seal. The winning bid for that overlay was $4.029 million. But Sierra Nevada Construction, the winning general contractor, proposed a value engineering change to CIR – and it saved the state $500,000, or about 12 percent of the total.
"The terrain in that location was steep with sharp curves in the road," said Darren Coughlin, owner of the Coughlin Company, the CIR subcontractor. "The asphalt surface was oxidized with transverse and block cracking. The roadway was paved with full depth asphalt that was 5 to 6 inches thick."
The mobile recycling train is led by a water truck towing a lime-slurry trailer. The next machine is a Roadtec RX-900 milling machine, which pulverizes the asphalt to a depth of 3 inches and conveys the material back to a Roadtec RT-500 mobile recycler. The milling machine pushes the water truck and lime trailer – and tows the RT-500 recycler and an emulsion trailer. The Roadtec RX-900 milling machine works 13 feet, 4 inches wide and took two passes to cover the 26-foot wide roadway.
When the milled asphalt reaches the RT-500 mobile recycler, it goes to a double deck screen and passes through 1.25-inch openings in the screen. Material that does not pass the screen deck is sent to a horizontal impact crusher where it is crushed and sent back over the screen deck. All material is sized to 1.25-inch minus. With its on-board screen deck, crusher, weigh bridge, and computerized metering of additives, the RT-500 provides excellent control over the cold recycled product.
Material passing the screen deck moves to the 48-inch-diameter twin shaft pugmill mixer on the RT-500. For the SR 722 project, the RT-500 mixed in 1.5 percent of CMS-2S emulsion plus 1.5 percent quicklime as an anti-stripping agent.
The RT-500 can meter in up to three additives. Weight data flows continuously from the belt scale, which is located between the screen and the pugmill, to the emulsion metering system. That assures real-time accuracy of additive metering at all times.
The RT-500 lays the material back down in a windrow on the road. Sierra Nevada Construction then used a windrow pickup machine and an asphalt paver to pave the recycled material. Two 12-ton double drum rollers and one 25-ton pneumatic roller compacted the material. Finally, the general contractor performed a double chip seal on the compacted asphalt.
Versatility of a central plant
"This was a unique project due to the terrain," Coughlin said. "The elevation on the project ranged from 4,700 feet to 7,500 feet above sea level. For the last 1.5 miles we had to take the train apart and set up a central plant operation, because the road was so steep and curvey that the train could not make it around the curves.
"It only took about half a day to set up the central plant operation," said Coughlin. With a central plant, the RT-500 is set up in a nearby stationary location, and trucks haul the milled asphalt to the recycler, which sizes the material and adds emulsion and quicklime. Trucks then haul the rejuvenated asphalt back out to the roadway.
"We like the cold-in-place recycling process," says Dan LeBlanc, project manager for Sierra Nevada. "It’s a green process that reuses the existing structural section. And it also provides a cost savings, so it’s better for the taxpayers, the contractor and the state."
NDOT’s Tedford says the state will perform about 30 miles of CIR this year. That amount is on the low side of the state’s average, but it varies with the need and available funding. "The process has provided a strategy that solves the problem of transverse cracking on lower volume roads that we don’t have the funding to reconstruct," says Tedford.