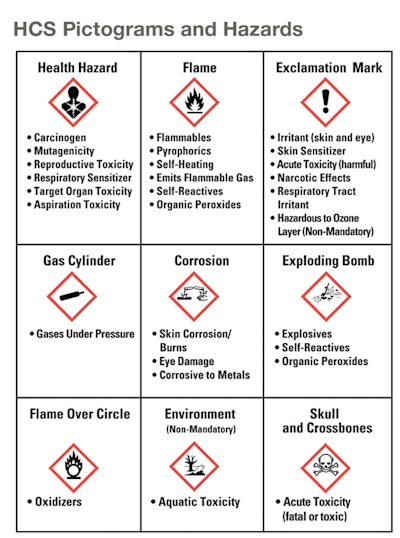
The Hazard Communication “Final Rule” has been in effect for over a year now. In that action, OSHA stated the Hazard Communication Standard (HCS) was to conform to the Globally Harmonized System of Classification and Labeling of Chemicals (GHS). This change was put in effect in hopes of reducing the cost and burden of labeling, while improving the quality and consistency of information being distributed regarding chemical hazards and the associated protective measures to employers and their staff.
Two significant changes were contained within these revised HazCom standards. The first change requires new labeling elements, while the second change will standardize the format of Safety Data Sheets (SDS), no longer to be known as Material Safety Data Sheets (MSDS). These standards won’t be enforced until 2015, but employers need to be ready now because the effective completion date of phase one is quickly approaching.
When December 1st of this year hits, employers must have their workers fully trained on the new label elements and the SDS standardized format. OSHA reports that companies should already be seeing these new labels and SDSs that are consistent with the GHS. In fact OSHA reports that many chemical manufacturers have already begun to produce HazCom 2012/GHS-compliant labels and SDSs. So it’s important that when employees begin to see the new labels and SDSs in their workplaces, they are familiar with them, understand how to use them and know how to access the information effectively.
[subhead] Knowledge = Compliance:
Six main training standards must be included when educating your employees on what they will see on these updated labels:
- Product Identifier: This represents how hazardous the chemical is. This could be the chemical name, code number or batch. This number is determined by the manufacturer, importer or distributer and must match Section 1 on the SDS provided.
- Signal Word: The terms “Danger” and “Warning” will now be used on labels to indicate the severity of the hazard and to alert the reader to this. “Danger” will be used for the more severe hazards, and “Warning” for the less severe. Only one of these signal words will be used on the label no matter how many hazards the chemical may have.
- Pictogram: OSHA’s required graphics must be in a square shape, set at a point. This will include a black hazard symbol on a white background and red frame.
- Hazard Statements: These phrases are used to describe the nature of the hazards of the chemical, including the degree of hazard (i.e. prolonged or repeat exposure may cause damage to the kidneys when absorbed through skin). All statements must appear on the label but can be combined to improve readability.
- Precautionary Statements: Describe the recommended measures that should be taken to minimize or prevent adverse effects that may result from exposure.
- Name, Address & Phone of the chemical manufacturer, distributor or importer.
[subhead] How to Teach It
It’s imperative that your employees know this information inside and out, both for their safety and to keep OSHA happy. But how can you make this information stick? OSHA recommends to first show the labels to your employees and explain how they might use them in their workplace. Explain, for example, how the information can be used to ensure proper storage, or how they would quickly locate first aid information if needed by other employees or emergency personnel. Relating the labels to how workers are going to use them will help workers connect the dots with what they need to know and use on the new labels.
According to Kevin Nordhues, compliance director for Vance Brothers Inc., they were made aware of this information through safety vendors that offer training programs for purchase, one being J. J. Keller & Associates.
“We have already educated our employees on the new standard, including label elements and pictograms via PowerPoint training in January and February of this year. We basically customized the training received from J. J. Keller,” says Nordhues.
Be sure the training you provide also includes the new SDSs, and familiarizing employees with the 16-section standardized format. It may be helpful to quiz them on these sections and ask what type of information should be included in each. To help with that, OSHA has created a QuickCard that identifies each section on the SDS. The QuickCard breaks down each section by number and name, describing what information is included in each area. By June 1, 2015, all SDSs will need to be in this uniform format so it’s important employees are familiar with it now. It may be helpful to print these QuickCards out for your employees so they can have them readily available at their work station should questions arise.
OSHA estimates that more than 5 million workplaces in the United States will be affected by this revised HazCom Standard. That means there are more than 43 million Americans that could be exposed to hazardous chemicals and need this training. OSHA also estimates that 43 fatalities and 585 injuries and illnesses will be prevented annually based on the implementation and standardization of this hazard communication. The monetized value of this reduction in occupational risks is an estimated $250 million a year on an annualized basis.
While compliance with many of the new standards is not required for a few years, OSHA is ensuring workers are provided with “the right to understand” during this first phase. By June 1st 2015, compliance with all modified provisions of the final rule will be required. By December of that year, distributors cannot ship containers labeled by the chemical manufacturer or importer unless the GHS label is applied. However, since the OSHA requirements on these standard are still a couple years off, many companies are simply waiting to comply with the new standard once requirements are finalized.