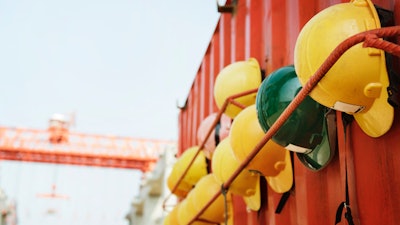
Article contributed by ecompliance.com
The United State’s worker fatality rate has not changed between 2008 and 2017, remaining at 3.5 workers per 100,000. Despite rising investments in employee health and safety over the same period (12% annually, according to Verdantix), we have not moved the needle on fatal workplace injuries.
We want to reduce workplace incidents and are spending more money every year towards this goal. Should we double training frequency or triple site audits or quadruple field-level risk assessments? Even with an unlimited budget, the answer is unclear.
Employee participation 1.0
We firmly believe that safety performance is controllable. The relationship between inputs and outputs is front-line employee participation. Workers most at risk of injury are best positioned to identify those risks. Empower them to eliminate risks, and they will succeed.
While the U.S. worker fatality rate is stagnant, we have the privilege of working with some of the safest companies in the world who have transformed their safety cultures. In 2018, we published a whitepaper titled “Building a High Participation Safety Culture” where we surveyed 40 customers and empirically defined employee participation in workplace health and safety. One-third of the companies in the study were from the construction industry. Spoiler alert: companies with top quartile participation reduced injuries 3.5 times more than their bottom quartile peers.
Participation measures the percentage of all employees who are involved in safety and the frequency of activities. High participation companies typically have 50% of all employees actively involved in safety and perform about one safety activity per day. Actively involved means the employee demonstrates intention, such as completing an inspection or a corrective action. Passive activities, such as attending a toolbox talk, are excluded. Showing up does not demonstrate intent.
eCompliance
Employee participation 2.0
What kind of ‘active’ activities do the safest companies perform, how often and how frequently? What do the safest companies share, and how are they different from the rest?
The whitepaper listed five steps that all high participation companies achieved.
- CEO commitment
- Rise of the safety leader
- Get employee buy-in
- Safety Reflex
- Safety Velocity
The fourth step, ‘Safety Reflex’, refers to information sharing and reaction time. Our follow-up research has focused on this concept. We found three driving factors backed up with data:
1. Act fast
Earning employee buy-in to your safety program takes more than words. Employees need to feel their input is valued and that management cares. In high participation safety cultures, workers are recognized for their expertise, empowered to report hazards and given resources to eliminate risks quickly. Companies with top-quartile participation completed action items ‘Early’ 1.5 times more often than their bottom quartile peers.
2. Transparent reporting
Some companies implement ‘zero incident’ programs. They mean well and set a noble goal. In practice, however, employees hear that no incidents should be reported since any incident is a violation. High participation companies encourage reporting and view it with a growth mindset.
Top quartile companies report nine hazards to every consequence while bottom quartile companies report four hazards to every consequence - a difference of about two times. A consequence is defined as any type of property damage or physical harm.
3. Proactive hazard reporting
Some examples of proactive hazards include hazard identification, safety observation, risk assessments and near misses. Some examples of reactive hazards include procedure violations, policy infractions and disciplinary actions. There is some debate whether near misses are proactive. We take the position that reporting a near miss takes time to stop and identify risk that would otherwise go unreported, and it is easy to ignore since there is no consequence.
Top quartile companies report 50 proactive hazards for every reactive hazard, while bottom quartile companies report five proactive hazards for every reactive hazard, a difference of 10 times.
What drives such a step difference between top and bottom quartile companies? To answer this question, I sat in a room with eight other colleagues reading proactive hazard reports from top quartile companies.
We read hundreds of forms of routine activities such as driving to work. Even for construction companies, driving represents one of the biggest risks’ employees face. These forms identified daily hazards we take for granted: it’s raining, roads are slippery; it’s snowing, roads are icy; it’s foggy, visibility is reduced. At first, we joked how mundane these forms were and figured there was a bonus associated with volume.
After a few hours, the power of these inspections dawned on us. They were not for the manager, or for a bonus, but for the employees themselves. Pausing to consider risks we take for granted, and writing them down, elevates our awareness and leads to safer behavior.
These employees were sensitive to risk many of us barely consider when we get into a car. Some even reflected on their drive once they arrived, noting where they followed too closely and unnecessarily increased collision risk.
It was amazing to read pre-job hazard assessments for housework, such as climbing a ladder to clean eaves troughs. These workers were in the habit of considering risks before a job and documenting their observations. The process helped them feel safe and prepared for the task.
Reducing workplace incidents is intentional. Safety performance is controllable through front-line participation. You are on the right track when a meaningful portion of your business is doing a daily safety activity. To get there, remember these three things: reaction time is how management tells their front-line workers they care and are paying attention. Transparency has impact when it is seen as an opportunity for growth and learning. The ratio of hazards, near misses and consequences says a lot about culture and is worth monitoring and benchmarking. Do these three things and our workplaces will be safer.
eCompliance is working towards a mission of eliminating one million workplace incidents by 2020. This mission is founded on the belief that safety performance is controllable, and there is a clear link between actions and outcomes. As the company discovers insights from its data and from its customers, eComplainace is sharing these findings through its Safety Nerd community. It is a mix of online and physical events where safety leaders can network, share best practices and have some fun.