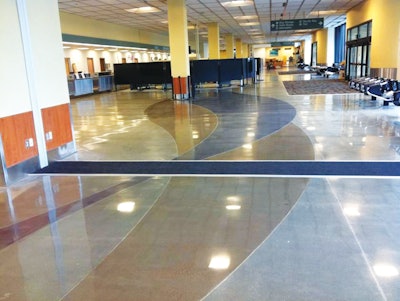
The terminal floor at the Ted Stevens Anchorage International Airport was a 20,000-square-foot, 40-year-old concrete slab that had seen a variety of floor coverings over the years, including tile and most recently carpet. The floor experienced moisture issues, and the carpet made the terminal look dark and out of date.
The design team in charge of the terminal remodel wanted a flooring option that would brighten the space and bring the facility into the modern age. Polished concrete was appealing for its ability to satisfy those needs, but it was polished concrete's low maintenance requirements that really caught the design team's attention.
Steve Rose, owner of Grand Prospect Corporation, a concrete polishing contractor out of Big Lake, Alaska, was brought on to consult the airport job for eight months. He answered the design team's questions about polished concrete, produced mock-ups, speculated on the condition of the concrete under the carpet and explained possible repair options since they didn't know what kind of cracks and spalling they might run into once the carpet was removed.
In the end, the airport design team decided polished concrete would be the ideal flooring option for its terminal remodel and hired Grand Prospect for the job.
Not just hard, but really hard
The Grand Prospect crew started the airport terminal job by removing the existing floor coverings and utilizing a ride-on grinder to remove old adhesives. Once the crew uncovered the slab, it found the floor wasn't as damaged as they thought it would be and were able to proceed with typical repair methods.
"One major issue we had with the floor was the flatness -- you could see the floor waving, or undulating, which we knew would present a few problems in catching those lows and highs when grinding," Rose explains.
With the floor open, repaired and ready for the polishing process, the Grand Prospect crew stumbled upon another surprise. "The floor was poured in a couple different phases. When we started in the middle it was hard, but we were using regular diamonds and having success," Rose says. "But it seemed every time we would cross over a joint line the slab would change, and the concrete was getting harder."
When Rose started scratching around the floor with a Mohs hardness test kit, he found in many places the concrete was a 9 on a hardness scale of 1-10 (10 being the hardest). "Of course that presented difficulties in getting the proper tooling," Rose explains.
Generally speaking, Rose says you want to have your diamonds set in a soft resin bond when you are grinding hard concrete. "If you use a hard bond on a hard floor, the diamonds would just glaze over the floor. That hard carrier wouldn't wear down fast enough to expose your diamonds and the process would be ineffective," he explains.
Grand Prospect worked with its abrasives supplier to get a variety of options shipped in so the crew could test for the most effective tooling. Rose found a super-soft diamond metal-bonded double wing round cutter in 30/40 grit that worked for the initial cut on the really hard sections of the slab. Grand Prospect's second grinding step on the hardest sections of the slab employed a Trojan double weight extra soft metal bond cutter from Diamatic in a 60/80 grit. On the sections of the floor that weren't so hard, the Grand Prospect crew was able to use a metal-bond abrasive with 30/40 grit followed by a 3-inch ceramic transitional abrasive.
Another conundrum Rose faced was the inability to do a full wet grind but somehow cool his diamonds on the super hard concrete. His solution was something in between a wet and dry grind. "We used a misting system," he explains. "We had one worker misting water in front of the machine with a pump sprayer, applying no more than would evaporate from the diamond use. It gave us some of the advantages of wet grinding without the slurry."
A winding design
Once the Grand Prospect crew refined the various sections of the floor with metal-bond abrasives, and in some sections with the ceramic transitional abrasives, it moved through the grinding process with resin-bond tooling. After it completed refining the floor with 400-grit resin abrasives, the crew set into creating the design on the floor.
The airport design team decided on two bands of color – one red and one black – winding down the floors of the terminal like two intertwined rivers. First crew members laid out the pattern on the floor, then proceeded to cut ¼-inch kerfs outlining the ribbons of color. Once the kerfs were cut, crew members applied the dye to the concrete and densified the floors. The next step was to fill the saw cuts with poly urea caulk in a gray color that matched the natural part of the concrete floors.
Once the pattern work was done, the crew refined the floor with 800-grit resin pads. From there crew members applied a floor finish product, specified by the architect, and burnished with 1,500-grit diamond impregnated pads. They then applied a second coat of floor finisher and burnished with 3,000-grit pads.
Last-minute color change
After the crew had all of the black on the floor and about 80 percent of the red placed, it got a message from the airport design team it wasn't expecting to hear -- red isn't going to work.
"Everyone loved the black, but no one liked the red," Rose says. "It just didn't look right on that large scale and no one was happy."
"The design undulates in and out, thick and thin, back and forth -- it has very crisp lines that are saw cut in the concrete, so it's not like we could just do over a big square area. It was a very precise design," Rose explains. "We discussed chiseling it out and putting in an overlay, which horrified me because the overlay would be flat and wouldn't match the undulations over the rest of the floor. There were other ideas about a feather finish overlay and staining that. But I talked them into giving me the chance to experiment a little and to find a color that would be acceptable."
With some guidance from Rose and a few members on the design team who had a good eye for color, the group decided to replace the red with sepia. The Grand Prospect team took its precision grinders to the floor, being careful to stay within the lines of the design. "The trick was to grind down in order to get rid of the color but not grind down too far and cause a noticeable depression," Rose explains.
The crew members started the process by removing the poly urea caulking from the kerfs that surrounded the red ribbon of color. They then used 50-grit resin pads on the hand-held grinders and cut down to the 50-grit level. "We couldn't get all the red out -- red stains deep -- but we were able to scrub it out pretty well so when the floor was dry you could only see a slight hint of the red," Rose explains.
Then crews followed through the same polishing sequence it initially used, applying the sepia in the appropriate step. "It was a very pleasing color and it went well with the black," Rose says.
A satisfied customer
When the terminal floors at the Anchorage International Airport were finally polished and boasting colors everyone could agree on, Rose tested the floor for gloss and slip resistance.
"One of the greatest successes of our floors, with the process we use, is we were able to give the airport a floor with 65 to 70 percent reflectivity and slip coefficient measurements of about 1.2," Rose says. The slip coefficient numbers caught the attention of the airport design team, considering a 0.65 slip coefficient is minimum for ADA compliance and on other floor finishes in the airport maintenance crews work very hard utilizing special products and never attain a slip coefficient of friction over 1.0.
Rose and his crew at Grand Prospect did all the right things in handling the issues the job threw at them. So well, in fact, that the airport has asked them back. "We exceeded expectations throughout the job in both not disrupting their flow and not creating dust and smells," Rose says. "We have since gotten other work from the airport with our grinding and polishing and it is looking at us for more projects, too."