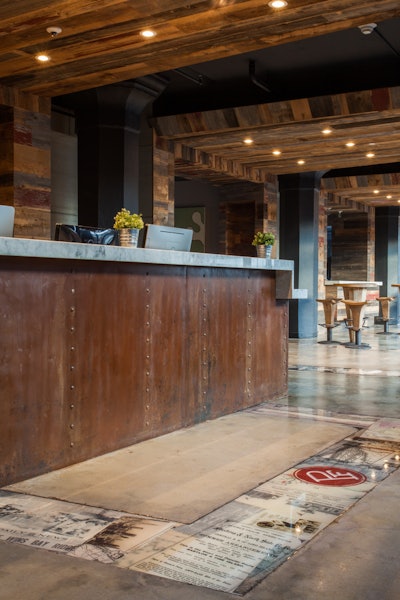
When the Paper Factory Hotel opens in Long Island City, N.Y., this fall, visitors will find an environment that at once embraces the building’s industrial past while offering the modern amenities and design of a contemporary hotel. As its name implies, the 150-year-old building housed a paper factory. Like many of the once-abandoned structures in the historic industrial Queens neighborhood, including those that housed Swingline Staplers, Chiclets Gum and Silvercup Bakery, the Paper Factory Hotel went through a renovation that upholds the history of the neighborhood and its industrial architecture.
In the Paper Factory Hotel, machinery and elements of paper manufacturing history are preserved as part of the hotel décor. Exposed brick walls, fluted concrete columns and the newly polished concrete floors are reminiscent of the building’s former life while highlighting the industrial design feel of the new hotel.
Manhattan Concrete Design completed the concrete polishing throughout the six-story building. The New York-based concrete flooring contractor got involved in the project when owner Matt Koerner met the Paper Factory Hotel owner through a recommendation from another contractor who was working on the building. Koerner met with the hotel owner and discussed the various concrete flooring options — polishing the existing floors, polishing an overlay, epoxy, and other decorative finishes. “The owner knew he wanted a distressed but nice concrete floor, he just didn’t know what. Exposed concrete is still a new flooring option. After considering all types of concrete floor options, the owner decided polished concrete would give him the look he wanted and fit his cleaning and maintenance needs,” Koerner explains.
The polishing process
The nearly condemned property that was transformed into the Paper Factory Hotel was demoed to the bricks for the renovation. Its solid wood floors and wooden beam support system were removed to reveal 18-inch-thick concrete floors. “Once the wood floors and beams were removed, it gave us 4 inches to play with,” Koerner explains. “We poured 4 inches of new concrete on every floor of the building.”
The Manhattan Concrete Design crew placed and finished the new 3,500 psi reinforced concrete floors, keeping the finish as flat as possible while avoiding over finishing the floor.
Some areas of the floors required leveling. Crews started with a 25 metal grit and exposed some aggregate in those parts of the floors. Other parts of the floors received a cream polish. “It’s pretty interesting that throughout the building you will find different levels of aggregate exposure,” Koerner says.
The Manhattan Concrete crews continued its polishing sequence with transitional diamonds before moving to resin-bonded abrasives. Crews followed a traditional sequence up to a 1,500-grit polish. They finished the floors with a stain guard and high-speed burnish.
Edge work requirements on the project were minimal. Manhattan Concrete Design offers three levels of concrete polishing — industrial, commercial and super polish. The Paper Factory Hotel received the industrial polish, which entails the least amount of edge and detail work. “That level of finish was the best match for the rustic look of the hotel,” Koerner says.
The Manhattan Concrete Design crew polished one floor before the walls were in. On the other floors, polishing took place before the door jambs and sheetrock were installed. “In a hotel, because of code and noise issues, they use a double layer of sheetrock which is 1-1/2 inches thick. That allowed us to get the majority of the floor with our large grinders,” Koerner explains.
No protection was used on the floors throughout construction. Post construction cleaning consisted of thoroughly auto scrubbing the floors, applying an additional coat of stain guard and one last high speed burnish.
Lobby treatment
The hotel lobby floors received a unique treatment that echoes the building’s paper-making history and adds visual stimulation for guests. After the polishing process was completed, the Manhattan Concrete Design crew shaved out a 12-inch-wide, 3/8-inch-deep groove that trails throughout the lobby floor. Then they placed vintage newspapers and posters in the groove and finished it with a clear epoxy to bring those areas flush with the surrounding polished concrete.
“The owner is completely thrilled with everything,” Koerner says. “He’s happy about the look, which achieves a sense of luxury while drawing on the building’s industrial history, but he also knows how much money he’s going to save over the years thanks to the concrete. He’s saving a ton of money — not just on the initial cost of the flooring, but also on the maintenance into the future. With no wood or tiles to replace, it’s really going to help their bottom line.”