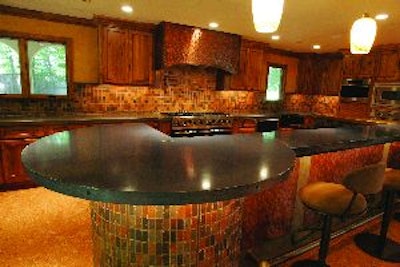
Just like snowflakes and fingerprints, no two concrete contractors are alike. Different backgrounds, business models and artistic flair result in a world full of unique countertop creations, customized for homeowners who offer their own vision to contractors for a truly one-of-a-kind piece of art.
Two concrete countertop contractors from opposite coasts and different backgrounds offer two unique perspectives on concrete countertop making. Chris Jarman of Concrete Connexion in Silver Spring, Md., started his career as a carpenter, restoring old homes in the Washington, D.C. area. "I always had an appreciation for the houses built pre-1940," Jarman says. "There was always a high degree of craftsmanship in those houses, and it was always a lot of fun to learn how the old timers did it as we took those houses apart and put them back together."
Jarman's artistic background led him to start drawing plans for his clients' remodeling projects. "I always had an interest in art and always found a reason to go back and have a pencil and paper in my hand for renderings and so on," he says.
When his wife sat on an airplane next to a man who set up concrete countertop manufacturing shops around the country and told Jarman what she learned, he knew he needed to bring that into his business. "It was a revelation that I could make concrete countertops, concrete fireplaces and objects of concrete art. It was an 'ah ha!' moment for me," he says. "I found a way to be a working artist and actually earn a living doing it and doing something I really loved."
Dave Pettigrew of Diamond D Concrete in Capitola, Calif., first worked as a journeyman carpenter but moved into concrete after he realized he could do a better job building foundations than the guys doing the foundations he was building houses on. "I started digging footings, setting up forms, pouring concrete into forms and I fell in love with it," Pettigrew recalls.
He first started in decorative concrete in the 1970s, using Brad Boman's "cookie cutter" stamps. In the early 1990s, Pettigrew was introduced to chemical staining. "It instantly struck a chord with me, and I realized why I was in concrete ? I could take all these designs I had been doing with the stamps and add the color work to the concrete and go wild with it."
Pettigrew then moved indoors with his decorative work. Around the same time he learned about Buddy Rhodes and concrete countertops, and Pettigrew got his hands on whatever information was available on the topic at the time. He started out creating cast-in-place countertops and just recently teamed up with local concrete precaster Dave Weber, with whom he now shares a precasting shop. Pettigrew says he has an edge over contractors who can only do jobs one way or another, and he's even worked on projects where he used precast and cast-in-place in conjunction to get the best results. "I believe whatever works best on a project is the way to approach it," he says. "I've heard people say that if you cast concrete in place you might as well just lift up a sidewalk 3 feet and call it a countertop, but I beg to differ. There are some people who do some beautiful cast-in-place concrete, and I'm one of them."
Marketing countertops
Jarman and Pettigrew have different approaches to marketing their countertops, but they've both found ways to dovetail their countertop and mold-making businesses with the rest of their services.
"It's hard to make it in this trade doing just countertops," Pettigrew says. "That's the crown jewel that we really look for, but I have to charge so much for them because of the labor and trips to the jobsite that if I just relied on countertops I couldn't do it. We have to diversify and do just about anything precast like benches and bowls."
Pettigrew says he's also often called out to bid a small decorative job and ends up introducing the client to concrete countertops or another decorative element. He tries to sell multiple jobs to one homeowner in order to make the smaller jobs worth his time.
Pettigrew offers marketing packets for his local architects and has a web presence through ConcreteNetwork.com, which he calls his best marketing tool to reach architects and homeowners.
Since bringing concrete countertops into his remodeling business in 2005, Jarman has begun to focus on more kitchen and bathroom jobs that also incorporate concrete features. "We still want to provide elegant living spaces and more comfortable, usable homes for people, but we try to get those jobs that allow us to do more of the concrete work," he says.
Jarman wants to keep his client base local, and he targets designers, architects and homeowners. One marketing arm he uses is the Internet, both through his website and as a member of the Cheng Concrete Exchange.
On the job with Chris Jarman
Jarman is meticulous on the job. "We kind of go overboard in making sure we don't get stress or structural cracks," he says. "One of the key things we do is add the minimal amount of water so we have a very strong mix."
Jarman lets his pieces cure at least five days before taking them out of the mold. He polishes his pieces with graduated grit on diamond polishing pads, starting with a 50 grit if they're going to expose the aggregate and typically end with either 1,500 grit for a satin finish or 3,000 grit for a glossier finish.
"In between the medium to finer grit polishing, we trowel on a cement slurry to fill the pin holes that will develop as we grind down," he says. He finishes with a minimum two coats of sealer and waxes all surfaces with a carnuba wax.
"We do the mold making well because we are also woodworkers," Jarman says. "I have a master mold maker in the shop and I have a lot of woodworking experience in my background, so the mold making comes easily to us. I make detailed shop drawings first, yet we sometimes need to make adjustments when mold fabrication is underway. It is a key part of being able to do these concrete countertops because every mold is custom made and then thrown away at the end of each project."
Jarman's attention to detail hasn't gone unnoticed. He was the recipient of the 2008 Best of Show award from Cheng Concrete's Member's Circle of Distinction Design Challenge for a concrete fireplace piece. The award-winning project also included about 40 feet of precast countertops in the client's home, including a 14-foot island with a 5-foot-diameter circular countertop at one end.
Jarman's first commercial countertop project was a coffee-serving area at a café (see Countertops Special Section cover photo on p. 34). It includes a 15-foot-long upper countertop that was poured in two pieces and a lower one-piece, 6-foot curved section that is 19 inches wide at its narrowest part and expands to 24 inches wide at the other end. Jarman used a stone concrete color and lightly polished the upper countertop as to not expose a lot of aggregate. He got a little more aggressive on the curved portion to expose more of the blue glass and yellow river stone aggregate on the lower curved piece. An agate inlay is a focal point for the piece.
Jarman recently completed a traditional kitchen countertop project that included a 42 inch by 66 inch by 2 inch thick island poured in one section. "It was a real challenge to get it through the door and flip it over," Jarman says, but his crew has experience in careful transport of precast concrete pieces. "We've made a carrying A-frame that we use on the back of our trucks. We carry them on edge and clamp them onto the A-frame so they don't move when they're transported. And we have a couple of big guys we call on who help us move the heavier pieces."
The stone concrete colored countertop features blue glass aggregate, a number of unique stones and fossils the homeowner wanted Jarman to embed in the countertop, and a built-in drainboard which also includes stainless steel rail trivets. "Those are a good idea for maintenance," Jarman says. "Built-in drainboards are utilitarian and provide a design opportunity."
On the job with Dave Pettigrew
Pettigrew has refined a proprietary mix over the years that allows him complete control over mix color and consistency. He weighs out all ingredients proportionally ? rock, sand, water, powder color, fiber reinforcement and so on ? so that he knows exactly what is in the mix. This allows him to recreate exactly the samples his clients approved. In order to remain consistent, however, he gives special care in the grinding step. "When you hone down the surface you have so much sand you want exposed compared to rock and cement, and you want to keep that ration of sand/cement/rock uniform so it shows the appropriate amount of material," he explains.
When it comes to finishing, Pettigrew uses the technique and products that best fit the job. "I don't use any one type of sealer, I use what works best for the project and the effect the client wants," he explains. A project with a lot of voids or spaces might be best with an epoxy. "Or if they want a natural concrete feel I use a penetrating sealer and beeswax," he explains.
Pettigrew recently completed an outdoor kitchen project that consisted of five cast-in-place concrete elements. The star piece of the system is an elevated horseshoe bar poured around the metal supports that hold up a gazebo. Below that is a main prep area and sink, and behind is another concrete countertop around a custom stainless steel sink with a prep surface. Off to the side is a concrete tabletop near a grill. All slabs were poured 1.5 to 2 inches thick and reinforced with #3 rebar and 6 gauge galvanized sheets with 2-inch squares. "We cut those out and leave about an inch clear around the border and then reinforcement is poured monolithically in the concrete," Pettigrew says.
The project also included a concrete couch with a curved seat and a concrete back rest. The concrete back rest was made of block, and Pettigrew poured the seat and plastered the back rest to give it a nice texture. A matching concrete bench can be found in an outdoor shower.
Another recent project from Pettigrew is a rustic, stone-looking, small precast countertop for a kitchen in an architect's office. It has a mottled, natural stone appearance characteristic of sedimentary rock. Pettigrew used a special technique to achieve this look. After building the mold, he splattered it in an irregular pattern with a baking soda paste. Then he added a cement mix, which included natural limestone in place of the rock and sand. On top of that he hand-packed the concrete. Pettigrew says he often uses this travertine effect on precast columns and fireplace surrounds.