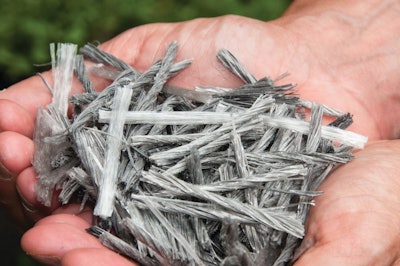
Adding steel or microsynthetic fibers to concrete isn’t new; we’ve been doing it for the past 40 years. Macrosynthetic fibers are a more recent development and they offer solutions to floor and pavement construction that neither steel nor micro fibers can deliver. At first, they were added to concrete at the same dosage rate as micro fibers; one and one half pounds per cubic yard of concrete. But more recently we’ve discovered they could be blended at higher dosage levels, changing some of their performance characteristics — especially for floor and pavement construction.
Dan Biddle, Forta’s vice president, sales, says dosages of 7-1/2 lbs. per cubic yard of concrete provide the most benefit to floor slabs, especially when compared to the cost of conventional temperature-steel reinforcement, sawcut labor, joint-filler and eventual joint repair. At this dosage rate joint spacing can be increased as much as 85 percent compared to standard floor mixes without fibers. Ultimate shrinkage is approximately 40 percent less and there is virtually no curling at joints.
What are macro fibers?
You have probably included synthetic microfibers in your mixes in the past. Typically a 1-1/2 lb. package is added to 1 cu. yd. of concrete and they come in lengths from ¾ in. to about 2-1/2 in. ACI defines microfiber monofilament strands as being less than 0.012 in. in diameter. Placed in concrete, they can help slabs resist observable cracks within the first couple days of placement.
ACI defines macrosynthetic fibers as greater than 0.012 in. in diameter — think of a toothbrush bristle. They can be placed in lengths up to 2-1/4 in., can be evenly blended in concrete at much higher dosage rates (micro fibers tend to “ball up” in higher concentrations) and they change some concrete properties over the life of a concrete slab.
Some early micro fibers originated from the carpet industry, while macro fibers were created exclusively for the concrete industry. The fibers for micro products are made primarily from nylon or polypropylene, each having the same effect on concrete, while macro fibers are typically made of polypropylene and related co-polymers
Biddle says dosage rates of macro fibers between 3 to 7-1/2 lbs. per cu. yd. of concrete produce slabs with reduced shrinkage and curling. He theorizes this is primarily due to the fibers ability to keep mix water uniformly distributed between the top and bottom thickness of concrete — creating a more uniform moisture gradient throughout the slab — instead of water collecting more at the top than the bottom.
RELATED:
- GCP Applied Technologies Launches Concrete App for Calculating STRUX Synthetic Macro-Fibers Dosages
- Pervious Concrete Pavement Gets Fiber Reinforcement
- Not Meshing Around
How macro fibers work
Several manufacturers and distributors sell macro fibers. They include BASF, Euclid, Propex, Forta Corporation, Grace and Nycon. A few of these companies also sell steel fibers. Biddle says the challenge for each company is to produce fibers that mix evenly in concrete regardless of length, have minimal influence on the air entrainment in concrete, and place and finish well in concrete at higher dosage rates.
Jerry Holland, the director of design services for Structural Services Inc., Jonesboro, Ga., says manufacturers often refer to the percentage volume of fiber in concrete — typically ranging from 0.5% to 1% — but determining volume is very complex and contractors think more in terms of pounds of fiber added to 1 cu. yd. of concrete.
“As measured by traditional means there is no difference between compressive, tensile and flexural strength of concrete with and without fibers. Macro fibers mostly influence post-crack behavior,” says Holland. “They keep cracks in the micro category so there is good load transfer. Most manufacturers offer fiber lengths of 1-1/2 in. but I prefer lengths of 2-1/4 in. lengths because they wrap around more aggregates, increasing ductility and anchorage. As fibers change direction it becomes more difficult to pull them apart.”
Concrete contains more water than is needed for hydration in order to facilitate placement and finishing. This extra water causes aggregate separation; aggregates sink and fine materials and water move to the top. Holland adds that macro fibers reduce aggregate and water movement, therefore reducing shrinkage and curling. He also believes the micro-cracking process enables concrete to move a little bit under load, resulting in less curling.
Installing high fiber slabs
As a concrete contractor, Bryan Birdwell, owner of Birdwell Associates, Lakeland, Fla., says he likes to know everything he can about the concrete mixes he works with and wants to control all components. He has a five-year history using macro fibers for floors, super-flat floors and traffic pavement. He both installs his own work and consults with other contractors about the installation of super-flat and high dosage macro fiber floors. His company’s specialty is super-flat floor construction, and he says they use macro fibers for that work too. “Working with 7-1/2 lbs. of macro fibers per cu. yd. yard of concrete is our magic number,” he says. “That’s where floor properties change significantly, allowing one to maximize joint spacing.”
Birdwell’s largest project using macro fibers to date is a 21,000 sq. ft. skating rink placed in 2011. The specifications called out no joints and no cracks. After completing his work he measured the floor for flatness and elevation changes and the numbers were very small. The original measured floor flatness was FF 123 and the floor levelness was FL 123 — numbers that haven’t changed in the past two years.
To achieve the best results using macro fibers requires a systems approach to floor construction. The process starts with the careful fine grading of base materials and proper, even compaction. Uneven subbase preparation can prevent floor panels from moving without restriction. He strongly recommends placing a good vapor retarding membrane on top of the subgrade and in contact with the concrete. This also enables the unrestricted movement of floor panels to reduce the potential for cracking.
Birdwell says he prefers a placing slump of 5-1/2 to 6 in., achieved by using polycarboxylate superplastizers. Depending on the mix design, dosage rates typically range from 4 to 8 ozs. per 100 lbs. of cementitious material. He recommends testing for the amount of air entrainment in the first few loads just to be sure the polycarboxylate and macro fiber product being used isn’t increasing the air entrainment level beyond acceptable levels. He adds that some contractors are also using shrinkage reducing admixtures.
WATCH: SurfaceTech Ace Fiber Additive Helps Improve Road Life
Benefits
Ideally, the owners of floors want perfect slabs that don’t require any maintenance. Construction joints and control joints are usually the locations where trouble begins in terms of repairs and curling issues. So increasing the spacing between joints equates to fewer issues over time. Including high dosage levels of macro fibers comes as close as anything on the market to providing owners with what they want.
The concrete industry is also beginning to see products such as Ductilcrete (a contractor franchise network) and the FAST Floor System offered by Birdwell & Associates, which use macro fibers in their proprietary process to provide maximum joint spacing, no-curl floors and long life-cycle pavements. They also provide warranties and prices that approach conventional concrete floors and pavement.
This article originally published on July 9, 2013.