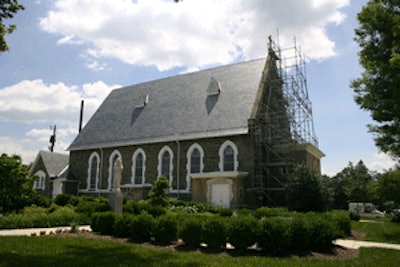
Whether the job calls for rehabilitating a 1920s-era high-rise structure in a city's downtown or restoring a Founding Father's estate to its original luster, historic preservation projects call for a great deal of expertise. A qualified contractor with the experience to handle the numerous challenges presented as well as the knowledge that each project has the potential to be vastly different from the last one is a must.
On any historic project, the age, building techniques used, location, materials and many other factors must be considered throughout the process. In addition, the history of construction is important to keep in mind. The most successful historic repair contractors often approach projects in the most conservative manner possible.
Areas of Concern
Over time, a structure may develop numerous problems. Perhaps one of the biggest enemies of any structure is water. Water infiltration is of particular concern with historic projects because the interiors of these structures are likely to have significant details that are irreplaceable or extremely expensive to repair; ornamental plaster, mosaics, and period millwork all require specialized tradespeople and are relatively labor-intensive.
In addition to interior finishes, foundations are another major area of concern when dealing with water and aging structures. The strength and stability of foundations are often undermined because of improper drainage and/or lack of maintenance; a gutter clogged with leaves for an extended period of time can accelerate settlement around the foundation, and reduce the slope around the perimeter of the building. Water should flow away from a building, especially older buildings that don’t have perimeter drains or sump pumps. A missing downspout could concentrate water from the roof so that it moves directly down the face of a building –- causing a serious problem for mortar above or below grade.
Even without a concentration of water, improper repairs will hasten mortar deterioration. Portland cement came into common usage in the 1870s and gradually became more popular than lime mortars because people were impressed by its great compressive strength. However, many contractors did not, and still may not, realize it was unwise to repair a lime or lime-based mortar with Portland cement. One of the great properties of lime mortars is their high free lime content and their consequent ability to self-heal natural settlement cracks. Moisture absorption into the mortar enables the flow of free lime to help fuse cracks, and the subsequent gradual release of moisture allows the mortar to re-harden. Because Portland cement is much harder and less porous than lime mortars, pointing-up over lime mortars with Portland will hold water in the enclosed ‘cavity’ it has created (the lime mortar areas that were sealed with the Portland point-up). The lime will then dissolve and, instead of a gradual release of moisture (since this is prevented by the Portland), the dissolved lime will ‘pour’ out in a solution. Lime that leaches out leaves only sand behind and, oddly enough, plain old sand is not a very good mortar.
Repairing lime-based mortars with Portland cement is an example of a mistaken assumption that new materials are always better. Using new products and materials on aging buildings can have the potential to contradict the original intent of the structure's design. However, new technology can and should be used in the appropriate way. When using innovative new products to repair an historic structure, much research and in-depth examination is needed to ensure the intended results.
Expert Knowledge Critical to Success
One of the most common misconceptions about historic preservation is that it's the same as any other type of construction. Owners may believe they can work with any contractor, and contractors with experience in new construction may think historic preservation is simply a quick jump. However, working on existing historic structures is quite different from new construction. It requires expert knowledge of the history of construction and historic building materials.
For example, expert knowledge of historic building materials was critical to the repair of the University of Maryland's Davidge Hall in Baltimore. Davidge Hall was originally built in 1812 and stands today as the oldest anatomical hall in continual use for medical education in the English-speaking world. Time had taken its toll on the historic structure and, in 2006, Baltimore-based Structural Preservation Systems was called upon to restore Davidge Hall's 200-year-old windows and doors. When feasible, the existing windows and doors had to be repaired. Portions that required replacement needed to match the original in profile, substance and appearance, using as much original material as possible. The key to success for this project was the knowledge of both historic construction materials and methods; precision was essential. Some severely deteriorated muntins required replacement within a tolerance of 0.0001-inch so that the original glass could be removed, salvaged, and placed back into the sashes. Dutchman repairs were employed where possible when material was missing or deteriorated, and no screws or metals were used in repairs – all pieces were dowelled and glued as they had been years ago when they were constructed. The original wood species was identified and matched for the repair.
New Not Always Better
People often think, "Why should we keep this old structure when it may be easier to build a new one?" New construction often cannot replicate the structural benefits found in historic materials. Old growth lumber is more stable, denser, and therefore stronger than new growth of the same species. It's also important that we preserve our nation's cultural and architectural heritage, not to mention resources. One of the first major historic preservation projects in this country was the restoration of George Washington's home, Mount Vernon, in 1858. Many generations have benefited from the educational opportunities of this preservation effort.
A common misconception is that it's more cost-efficient to tear down an old building and build a new structure. However, new construction –- especially if the building is within a historic district –- may fall under a set of building regulations that could have a financial impact on the project. A recent example when this misconception affected a project financially, involves a building located in a historic district in Bel Air, Md. The building, not protected by historic standards, was demolished in order to build a new structure in its place. However, since the property is located in a designated historic district, the new building must match the district's strict design standards. Now, the owner/developer is having a difficult time getting through the Town's permit and planning boards. These delays affect the project’s bottom-line. In this case, it would have been much more cost-efficient to rehabilitate and adapt the existing structure to its new purpose. Before a decision is made to tear down and build new, all factors must be considered carefully.
Select the Right Firm
Another key to a successful historic repair project is selecting the right firm. Owners should look for experienced, professional firms that take an individualized approach to projects. The following items should be considered: bond capacity, size and longevity of the firm, craftsmanship, a formal Quality Assurance/Quality Control program, as well as proven experience with projects on nationally or locally registered historic structures. Be sure to ask the contractor about their familiarity with the Secretary of the Interior's Standards for Rehabilitation and Guidelines for Rehabilitating Historic Buildings. Failure to address these Standards when designing and undertaking historically sensitive projects could negatively affect Historic Tax Credits and could have a financial impact on a project. Finally, make an attempt to assess the contractor's communication skills. Is the contractor available and responsive? If the contractor isn't conscientious about returning phone calls when a potential client requests information, responsiveness isn't likely to improve as a project progresses. On a historic preservation project, good communication is particularly important.
Mark K. Howell is a Project Development Manager with Structural Preservation Systems. He is a recognized leader in concrete and masonry maintenance repair and has been involved personally in the restoration of many historic structures during the last decade. With a degree in civil engineering and construction management technologies, Howell is a member of the International Concrete Repair Institute, the American Society of Testing Materials E6 Committee, the Sealant Waterproofing Restoration Institute, and the Exterior Design Institute.
Adrienne DeRan is a Project Engineer with Structural Preservation Systems. She is a graduate of Tulane University and has worked on a variety of structures from National Historic Landmarks and federal buildings to resort hotels and adaptive reuse projects. DeRan is involved with the Preservation Trades Network (PTN) and was recently nominated for the Board of Directors. She can be reached at [email protected].
About Structural Preservation Systems
Structural Preservation Systems is a division of Structural Group, one of the nation's leading specialty contractors. Structural Group's four companies include Structural Preservation Systems, VSL, Pullman Power and Electro Tech CP. Structural Preservation Systems is the largest specialty contractor focusing on structural repair, masonry and concrete restoration, strengthening, and protection services for both historic and contemporary structures. VSL is the technical leader in post-tensioning and specialty reinforcement. Pullman Power leads the industry in chimney, silo, and stack construction, maintenance, and repair. Electro Tech CP is a specialty provider of corrosion control services, and technology that protects infrastructure, buildings, and investments worldwide. From operating centers across the United States, Structural Group businesses perform a wide range of projects involving industrial facilities, commercial properties, public infrastructure and municipal buildings. For more information about Structural Group, visit www.structural.net.