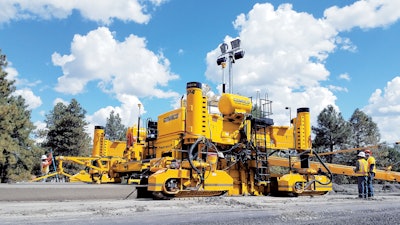
RGG United Contractors, Inc. was started by two friends, Martin Rangel and Roger Garcia, as a small residential contractor specializing in curb and gutter and sidewalk on residential projects in Arizona. They added barrier work to the company’s resume, as well. In 2008, they brought John Kliethermes, a licensed structural engineer, into the company, and for the last 10 years RGG United has transitioned into large federal and municipal projects, including slipform paving, taxiways, runways and freeways.
As RGG United has grown, so has the size of its slipform paving equipment. The company started out utilizing used GOMACO GT-3600s for curb and gutter work. From there, it purchased a four-track Commander III before graduating to a GP-4000, with the capability to slipform up to 50 ft. wide, a 9500 placer and T/C-600 texture/cure machine.
“We started with one paver, one cure machine and a 9500
“It’s been a good stretch for us and now we’re almost solely (revenue based) involved in airport and freeway work – probably 60/40 airport to not," Kliethermes said. "And we’re the sole paving contractor for Phoenix Sky Harbor International Airport since 2009.
“Our two owners have always taken a lot of pride in the equipment, keeping it updated and keeping up with technology. If we have a successful year, their first inclination is to upgrade our tools.”
Last year, RGG replaced the GP-4000 with a GP4, from GOMACO’s family of next-generation pavers. While the next step up in size, the GP4 features the same technology as the GP3 but with the ability to pave up to 40 ft. wide. In addition to bringing the latest technology, the GP4 also offered RGG the advantage of being able to utilize attachments and sensors from the GP-4000. The technology is plug-and-play with the G+ control system.
Full Smoothness Bonus on I-40 Devil Dog
RGG United was hired by the prime contractor to do the concrete slipforming.
“I know when people think GP4, they think wider width paving, but it shrunk down nicely to what we needed,” Kliethermes said. “We did a lane path 24 ft. wide and it performed nicely. This stretch had grades up to 12% incline and decline so it was a unique project climbing up and going down. The GP4 handled it well going uphill and pushing the concrete.”
The Arizona Department of Transportation (ADOT) uses the profile index (prI) with a 0.1-in. blanking band to measure smoothness on its roadways. “The ADOT does offer payment up to $1 per sq. yd. for that smoothness spec and we achieved the full $1 on everything we paved,” Kliethermes noted. “The first major project for this machine and we achieved full bonus – approximately a $70,000 smoothness bonus. That’s real money in the hands for us.”
Successful Approach to Runway Paving
Next up was airport paving and a new concrete taxiway for the Phoenix-Mesa Gateway Airport in Mesa. Phoenix-Mesa Gateway is a commercial airport with a 12,000-ft.-long runway that is able to accommodate some of the world’s largest aircraft, including the Antonov A380. The Apache Strike helicopter manufacturing plant is also located nearby, making it the preferred airport for shipping.
“Airports always need as much real estate as they can get for their operations and they don’t give us a lot of room to work in,” Kliethermes said. “Plus, they lock us into paving in just one direction. A nice thing about the GP4 with slew drives is we just extend the frame out far enough so the tracks can be turned 90° and we can walk completely sideways. Then, we just have to back the paver up to the starting point for the next day’s pour. Its ability to move laterally forward, its travel speed and the simplicity of doing it were key purchasing factors for the [paver] and working inside an airport.”
The operator can put the GP4 in transport mode to walk the paver sideways or load for transport in minutes without assistance. It also features a fast jobsite tracking speed for moving across the project, with a travel speed of up to 66 fpm.
RGG United positioned its concrete batch plant close to the airport to supply concrete for the project. The concrete mix is its own in-house design built for the flexural strength required on today’s airfields.
“Airfield mixes are evaluated on their flexural strength rather than a typical compressive strength in concrete,” Kliethermes explained. “It’s a very high aggregate content, very rocky mix with a low slump preferred placement of less than 2 in. It is not finish friendly but the GP4 finished it out very nicely.”
The paver completed the taxiway in two passes, each 37.5 ft. wide and 16.5 in. thick.
Meeting Strict Specifications
Federal Aviation Administration (FAA) and U.S. Army Corp of Engineer guidelines for airport paving require finishing work to be kept to a minimum. They don’t even allow a bull float to be used on the newly paved concrete. Paver setup and performance is crucial for a smooth slab and sharp edges.
“One of the hardest things to do is stand up the edges when you’re at 16 in. tall. We had not one single edge slump deficiency on the entire project,” said Kliethermes. “I actually walked across the project with the FAA and they were very surprised and impressed with the surface finish and how the edges held.”
A T/C-600 texture/cure machine followed the paver and applied the final texture finish to the surface of the new runway.
According to Kliethermes, the airport classifies must-grinds and smoothness ratings. The FAA uses a profile index allowing a certain amount of variation per mile. RGG United had zero smoothness grinds, earning full payment, plus a 6% pavement bonus.
Onward and Upward
Paving on the airport was completed in six days and the new taxiway was open to aircraft in just three weeks. Since then, the GP4 continues to travel around Arizona successfully completing quality projects.
From the Phoenix-Mesa Gateway Airport, it went to Sky Harbor International Airport in Phoenix for a couple of pours. Then it was transported to Holloman Air Force Base in New Mexico to slipform a 75-ft.-wide taxiway.
“Everyone that has used the GP4 has enjoyed everything from the interface all the way down to how easy it is to access the hoses and service the piece of equipment,” Kliethermes said. “The paver handles beautifully and the ride comes out good. GOMACO has made a paver that is easy to move weight wise and versatility wise while also still providing the power and the strength to pave that thick of concrete, that wide.”
On the Road Again
One unique project that RGG United is also currently involved in is a Federal Highway Administration mega-project on the Loop 202 (South Mountain Freeway). According to the project’s website, it’s the largest project in the state’s history to use the design, build and maintain (DBM) approach. This approach requires the developer to be responsible for maintaining the freeway and giving the traveling public a safe roadway for 30 years.
RGG United will be slipforming approximately 76 miles of barrier wall on the project. It will also slipform 57 miles of curb and gutter. The company currently uses a GOMACO 4400 for barrier work and will be adding another new 4400, as well as the new Xtreme three-track Commander IIIx for the curb and gutter work.
“For the majority of work we do now – airfield paving and slipform barrier – there probably isn’t a specification tighter than when it comes to these two items,” Kliethermes said. “We have found that with GOMACO and their ability to stay on track with upgrading technology, it has allowed us to be able to put these in with less risk to us.”