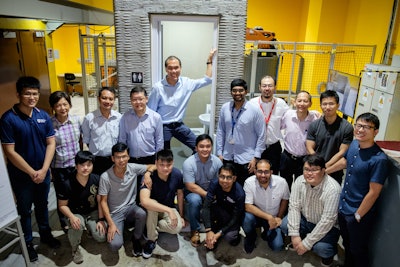
Researchers from Nanyang Technological University in Singapore (NTU) have developed the capability to 3D print an unfurnished concrete bathroom in less than a day.
After printing, the bathroom is furnished with toilet fittings to become a pre-fabricated unit, ready for use in construction projects. Its interior includes a sink, mirror, shower, toilet bowl, ceramic tiled walls and flooring, complete with concealed drains and piping.
Since 2014, all non-landed residential Government Land Sale (GLS) sites in Singapore have been required to use prefabricated bathroom units (PBU) in their construction process. PBUs are usually cast from concrete and pre-assembled offsite with all necessary finishes and fittings to be lifted and installed in a building project.
NTU's proof-of-concept aims to improve productivity for Singapore’s building and construction industry through the use of digital and robotic fabrication methods to reduce skilled labor and manpower requirements. By shifting most of the fabrication off-site to the controlled environment of a factory, PBUs yield time and manpower savings of about 60 percent, compared to on-site construction which was the practice prior to 2014. There is also better control over the materials and the prefabrication process, resulting in higher quality finishes and lesser wastage. The addition of 3D print technology in the manufacturing process could further help firms build PBUs about 30 percent more quickly and 30 percent lighter. From right, NTU associate professor Wong, associate professor Tan and Er Lie from Sembcorp.
According to associate professor Tan Ming Jen from NTU’s Singapore Center for 3D Printing, 3D printing a bathroom unit could help manufacturers halve their production time while lowering transport costs, carbon emissions and materials wastage because. In addition, less space is required to create and store the same number of PBUs in land-scarce Singapore. Conventional PBUs take about two weeks before they can be ready.
“By being able to print-on-demand, companies can save on their inventory costs as well as manpower costs, as they don’t have to hold as much stock and their workers can be redeployed to do higher-level tasks. This approach improves the safety of the workplace, since robots are doing the construction of the bathroom unit,” says Tan.
3D printing technology also allows concrete to be printed and customized, adds Er Lie Liong Tjen, team lead from Sembcorp Design and Construction and Sembcorp Architects & Engineers.
"The complicated shape of a PBU and its walls can be developed and printed at a faster pace to satisfy the needs of individual customers as no formwork or molds are required, whereas conventional construction of PBUs with concrete or lightweight wall panels always limit the possibilities of design. In addition, 3D printing can build curvilinear profiles rather than rectilinear forms," he says.
Over the past four years, the research team focused on developing a special concrete mix that is fluid enough to flow through the hoses and print nozzle, yet can harden fast enough so that the next layer is able to be printed on it. On top of ensuring a consistent print quality, the final product also has to be as strong as conventional concrete. The new mixture includes green building materials such as geopolymers, which are made from fly ash waste.
This innovation was developed by a joint research team led by Tan Ming Jen, in partnership with Sembcorp Design and Construction and Sembcorp Architects & Engineers. The Singapore Center for 3D Printing was created by National Research Foundation (NRF) Singapore to conduct research and development on 3D printing technology and accelerate the adoption of the technology by companies.