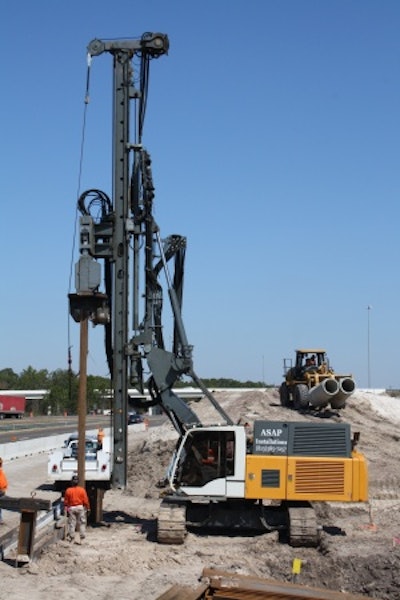
ASAP Installations LLC, based in Lutz in the Tampa Bay area of Florida, was established in 2006 as a specialist steel sheet piling subcontractor by company president Simon den Tuinder. Despite the market downturn, it has built up a fleet of four piling rigs with four crews by persuading general contractors of the benefits of outsourcing piling to a specialist.
"As a specialist, we can do sheet piling installation more quickly and more economically than anyone else," den Tuinder says.
This capability has been significantly enhanced with the purchase in December 2009 of a Liebherr LRB 125 piling rig. ASAP initially took the machine on a lease deal last summer from Liebherr Nenzing Crane Company. But after a successful trial period, ASAP went ahead and purchased the machine.
More force equals more productivity
ASAP needed a high-production machine for a contract installing nine miles of sheet piles at Eglin Air Force Base in Fort Walton Beach for the US Army Corps of Engineers. This is where the LRB 125 piling rig came in.
Conventional vibratory hammers drop only with the force of gravity and are pulled back up with a cable. On Liebherr's LRB series piling rigs, the hammer slides from top to bottom on a fixed leader that pulls the hammer down at the same time as vibrating. The LRB 125, the smallest model in the series, gives a downforce equivalent to 33,700 lbs - at least triple the downforce offered by conventional free-hanging hammers.
A conventional crane-based piling rig with a free-hanging hammer can install maybe 20 pairs of sheets a day. At Eglin, the LRB 125 - fitted with a Liebherr 2323 VML high-frequency vibratory hammer with variable moment - was able to achieve a maximum production rate of 75 pairs of sheets a day, equivalent to 300 ft.
"We like this machine because not only does it offer high production, but also the additional downforce means we can penetrate harder ground," den Tuinder says.
In addition, the rigid mast system means a lot less deflection than conventional telescopic leader piling rigs, which ensures straighter piles and minimal readjustment required during the driving operation.
After completing the Eglin project, ASAP's new rig again proved its merits in the Everglades in January, installing steel sheet piles for a South Florida Water Management District storm water control project. The power of the LRB 125 was able to penetrate a layer of hard rock.
"Typically, conventional sheet piling equipment could not have penetrated that rock. With the LRB 125 we were able to chip away and toe the pile into the rock, rather than just sit on top of it. Making the foundations more solid like this increases the strength of the structure," says den Tuinder.
Mobility enhances use
It is not just the speed and strength of the machine that makes it so useful, however. It is also highly mobile and more compact that an equivalent lattice boom crane.
As a specialist, ASAP takes on jobs all over the state of Florida, sometimes quite small and lasting just a few weeks. "For transport, we just take off the vibratory hammer and fold back the leader," says den Tuinder. "There is no dismantling the boom, like on a crane. It is much easier and quicker to move between jobs."
On site, the LRB 125 has proven itself a nimble mover, as well. In February, ASAP put it to work on a Florida Department of Transportation project on I-75/I-275 in Tampa, where new exit ramps are being built to State Road 56. ASAP installed a series of six coffer cells, each 30 ft. square.
Sheet piles provided a structure that could be excavated to enable the installation of utilities by micro-tunnelling from within the pit. The rig was compact enough to set up inside each cell, install three sides and then walk back to complete the last side from the outside. "We do not need a lot of space to set up," den Tuinder says.
Moving between cells was easy, too. Where there was an overpass to go under, it was simple to fold back the leader to reduce the machine's height, den Tuinder says, although when navigating slopes the hammer would also be removed to ensure maximum stability.
Stability of the Liebherr LRB series is improved by having a lower centre of gravity than comparable machines. This achieved by having the hydraulic hoses move up and down with the hammer without routing them over the top of the leader.
ASAP's machine is now returning to the Everglades for further work with South Florida Water Management District.
Adding versatility
The flexibility of the LRB 125 also opens up new possibilities for ASAP. The unit is a combination piling and drilling rig, delivering from 33,200 ft-lb to 88,500 ft.-lb. of torque, depending on rotary. The LRB can also run a hydraulic impact hammer.
According to den Tuinder, "We can put an auger or a press-in system on this machine, too. So if the ground is too hard to install the sheets, we can pre-drill, or if the client does not allow vibrating, then we can use the press-in system. This means we can offer an even more complete package to general contractors - vibrate, pre-drill or press in."
Source: Liebherr Nenzing Crane Co.