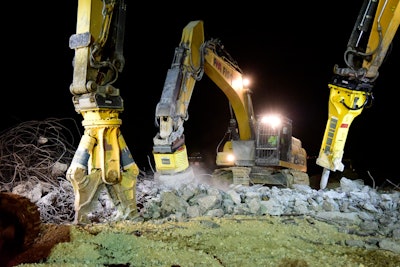
Demolition can be a brutal environment, yet attachments that are properly maintained can have a service life measured in decades.
“If you want anything to run at peak performance, you need to constantly maintain and stay on top of it,” says Tom Schwind, business line manager, Epiroc. “Everybody wants to treat their attachment like a bucket. They don’t want to do any maintenance to it.
“The most important thing is to keep up with your preventive maintenance,” he continues. “Be aware of your environment and treat the attachment like it’s a piece of equipment, not just an ancillary bucket or something that you’re going to destroy. The environment for demolition tools and hydraulic breakers is a very tough environment. We don’t need to make it harder.”
Preventive maintenance programs have a proven track record. “I have a customer in Philadelphia that has hammers that go back to the Krupp name in the ’90s,” Schwind notes. “They’re still running every single day. They have an excellent maintenance program.”
Understand Maintenance Demands of Specific Tools
It all starts with following the manufacturer’s recommended service intervals. The type of service required depends on the specific attachment. For instance, crushing and concrete pulverizing attachments need periodic inspections for cracks.
“When you’re using any kind of muncher, cracker or shear, a crack presents a real problem. There’s a lot of tertiary forces. You can find a crack, detect it, air arc it out, re-weld it and you’ll be fine,” says Schwind. “You let that go and that little crack becomes the proverbial huge crack. I’ve seen lots of demolition tools literally split in half.” Steel can be worn away quickly in crushing applications.
Shears and processors are high maintenance attachments. Maintenance intervals are a guideline because the severity of the application and operation may require additional and increased scheduled maintenance.Okada
“Maintenance intervals are a guideline because the severity of the application and operation may require additional and increased scheduled maintenance,” he adds.
Hydraulic breakers have unique set of maintenance requirements. “Grease and lubrication is the key to hydraulic breaking,” says Schwind. Friction due to lack of lubrication creates heat and will quickly wear out the lower and upper bushings and thrust ring. If the bushings wear out, they will eventually take the seals out. “Now you have an extremely costly repair. If your lower bushing is wearing quickly, my suggestion is to replace that bushing before it gets to 100% wear. You may want to replace it at 85%.”
Bushing wear needs to be constantly monitored. “A lack of grease and neglect — not checking the bushings on the breaker and allowing those to get worn past serviceable limits — will inevitably induce a catastrophic failure,” says Greg Clinton, product service manager, Montabert.
Don’t ignore leaks in the interest of finishing a project. “You can also have a very sudden catastrophic failure with a breaker because the seal goes out and it starts leaking oil,” says Schwind. There is a temptation to keep going to finish a job when a leak first appears. “If a hammer is leaking oil, you need to shut it down immediately because that oil becomes like a lapping compound which results in much more damage. Pushing it may cost you a lot more money in repair or replacement.”
Regular inspections ensure proper hammer operation. “We recommend every 40 to 50 hours of breaker operation to remove the tool and inspect,” says Clinton. Reseal the breaker anywhere from 350 to 500 hours if the hammer is not leaking. “If the hammer is not leaking and your bushings are within spec, run it until your bushings are close to wearing out. Once you get to the 95% wear mark on your bushings, you need to start looking at scheduling it to get resealed.” Take it down, replace the bushings, reseal and inspect. “It pretty much goes on bushing wear unless you have a catastrophic failure.”
An exception would be a breaker that sits idle for long periods of time. “Even if the bushings are not worn out, if you are not using the hammer every day and it is sitting a lot, I would recommend that you reseal it yearly,” says Clinton.
Autolube systems are recommended for mid-size and larger breakers. “All of [Epiroc’s] medium and heavy breakers come with autolube included in the price. We have what we call the ContiLube system,” says Schwind. “An autolube system will probably get you 10 to 12 hours on our largest hammers, depending upon how you have the setting.”
Montabert recommends autolube systems on all breakers 3,000-ft.-lb. impact class or greater. “Typically, once you get to 3,000 ft.-lbs., you cannot put enough grease by hand to the bushings to keep it washed and keep it lubricated,” says Clinton. “Heat will take up a good share of that lubrication. The heat is so great that you just cannot keep up.”
Telematics Changes Game
Tracking hours on most attachments has been a guessing game, but that is changing with telematics.
For example, Epiroc has released HATCON, a telematics system that tracks how long an attachment (not just hammers) operates. Because it works off the vibration of the machine, it allows you to differentiate between when the attachment is operating and when the machine is operating, providing actual service hours for the attachment.
Telematics systems can also be used as training tools. “Hydraulic breakers should not be run for more than 30 seconds,” says Schwind. “If it’s not penetrating, you risk hurting the piston, mushrooming the point, it will not be getting grease. There’s a lot of bad things that can happen in that scenario.” HATCON will let you know if the operator is exceeding that limit. “It’s not a big brother thing; it’s an opportunity for you to help train and work with end users to make them better at what they are doing.”
Ensure a Proper Match
“Improper sizing of the carrier and attachment is the first mistake companies and end users make,” says Smith. “If the attachment is too small, you may not be able to process the material based on size and type. In these cases, you can experience longer cycle times, premature failure and increased cost of wear items (i.e., blades, knives and teeth). You may experience a need for more frequent maintenance intervals and increased repairs to reduce premature failure of structural and major components that may not be covered by the manufacturer’s warranty. Increased downtime can occur, which affects profit and the bottom line.”
Montabert recommends every 40 to 50 hours of breaker operation to remove the tool ad inspect. Reseal the breaker anywhere from 350 to 500 hours if the hammer is not leaking.Motabert
Hoses Are The Lifelines
Keep an eye on the condition of hydraulic hoses. “Demolition environments are incredibly demanding. Hose life can be significantly shortened under such applications,” says Keith Zulauf, senior fluid power application engineer, Gates.
“Consider the enemies of the hose to include heat, abrasion and ozone — and each of these is present in demolition environments,” he points out. “Demolition equipment also sees very high duty cycles, quickly oscillating between unloaded and maximum load conditions, which puts additional demand on hydraulic components. Temperature can also be an issue — both the system temperature and the ambient temperature. Gates offers high-temperature hose product solutions for these types of applications.”
Grease and lubrication is the key to hydraulic breaking. Friction due to lack of lubrication creates heat and will quickly wear out the lower and upper bushings and the thrust ring. If the bushings wear out, they will eventually take the seals out.Epiroc
Hose couplings can become a source of failure. “Proper installation of the hose coupling is critical to assembly performance,” says Zulauf. “Over- or under-torqued thread-end terminations can lead to system fluid losses and contamination, creating fire and safety hazards and necessitating environmental cleanups. Maintenance personnel should receive training in thread-end torque requirements. Torque wrenches should be used for thread-end termination installation. Over-torqued hose assembly thread-end terminations are one of the leading causes of short assembly life, as a result of cracked coupling mechanical seats leading to leaks at the coupling.”
Also ensure that you do not create restrictions when installing quick couplers on the hoses. “If you are going to use a quick coupler, we recommend one that is the same diameter as your hose because you don’t want it to be a neck-down point,” says Schwind. “It can create heat, which is bad for all hydraulic attachments. It can also change the pressure because you are necking it down.”
When utilizing hydraulic quick couplings, Epiroc prefers the screw-on fittings for larger demolition tools. “You can get a positive pipe fit,” says Schwind. “It doesn’t allow any contaminants. When you take it off, you can reverse the male and the female on each line.” When the attachment is removed, the two hose ends can be connected to create a totally closed system. Nothing goes in the dirt, so you don’t let contaminants in.
Schwind adds, “If you are using any quick coupler, make sure you definitely have either an inline filter or your filter is working in your tank to pick up if anything does let go.”
Ensure Cleanliness of Replacement Hoses
Take special precautions when fabricating replacement hoses.
“The hose assembly process introduces contamination in a variety of ways: lubricants from the hose manufacturing process; contaminants from the coupling fabrication and plating processes; and debris generated when the hose is cut,” says Zulauf. “Hose cleaning systems like Gates MegaClean and UltraClean can remove assembly contamination before the hose assembly is placed in service. Both systems use pneumatic projectiles to remove contaminants. Cleaning a hose assembly in this manner is quick, easy and effective.”
To minimize the risk of contaminants, always cap a hose immediately after assembly and cleaning. “If you’re wondering why it is so important to minimize contamination, consider the system on which this hose is being installed,” says Zulauf. “Hydraulic pumps are extremely expensive, and their operation is tuned for tight tolerances at the valves and pistons. These are small orifices, and any contamination in the hydraulic fluid can affect their operation, so cleaning the hose assemblies after crimping is essential to minimize downtime and maintenance costs.
“Proper hose routing is the best way to protect a hose assembly from environmental damage,” he continues. “Hoses that are too long can unexpectedly rub against machine elements. Hoses that are too short may require excessive bending at the coupling, which can minimize hose life. Proper routing can also include clamping and/or yoking the hose to the machine to keep the hose in place, although care should be taken to account for hose flexing and hose elongation when pressurized to avoid creating other problems.”
Selecting abrasion-resistant covers and using hose accessories for risky areas can help extend hose life. “Manufacturers such as Gates offer high-abrasion hoses that provide significantly longer life in those applications,” says Zulauf.