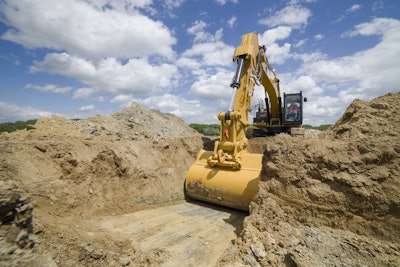
While excavator guidance systems have been around for a few years, the adoption rate has been slow. Both Caterpillar and Komatsu America Corp. recently introduced excavators with integrated grade control technology to help customers realize the true potential of this technology, but they are taking very different approaches. Caterpillar offers an integrated 2D guidance system that can be simply upgraded to 3D to allow customers to witness the productivity gains with minimal risk, while Komatsu is rolling out an automated excavator grade control system.
Scott Hagemann, market professional for the machine control and guidance group, Caterpillar, says customers have been slow to adopt grade control technologies for excavators because the systems are indicate only. “As the customers transfer to using technology on motors graders and dozers, they will not want to set stakes just for the excavator. Without trying the technology on their excavators, the customer does not know the productivity being lost. Once the system is demoed, they see how much of a benefit even indicate-only technology is and the need to have it.”
Cat Grade Control Depth and Slope is a 2D depth and slope guidance system designed to help guide the operator to a preset grade. Caterpillar chose to integrate the system on its standard 323F L excava-tor, which is in the highest volume size class — 50,000 to 55,000 lbs. “It is a 23-metric ton machine,” says Brian Stellbrink, market professional for F Series Excavators, Caterpillar. The system comes stand-ard on all excavator model configurations equipped with the 9.5-ft. stick. “It needs only to be activated at the dealership as part of a routine delivery.”
While integrated on the 323F, the system makes sense for other size excavators, as well. “It is beneficial to order Depth and Slope on all sizes,” says Hagemann.
Using 2D depth and slope guidance, the excavator knows where the bucket teeth are relative to the base of the machine. It works by using a series of sensors, including a sensor in the bucket cylinder, a rotary sensor at the boom-to-stick connection and a sensor at the base of the boom. The sensors al-low the machine to calculate the position of the stick relative to the boom and the position of the boom relative to the base of the machine. “Knowing all that geometry, the machine can calculate automatically where the teeth are relative to the base of the machine,” says Stellbrink.
The operator can now set the desired depth and slope from inside the cab. “For example, if you’re doing a 10-ft. cut with a 2% slope, you can enter that in the monitor, bench that bucket off a known point and start to dig,” says Stellbrink. “[The system] will guide you through audible alarms in the cab and a standard display on the monitors to dig toward that preset grade.” It helps operators to be more productive, finish the job faster and rely less on ground support. It can also lower labor costs, since you are not as reliant on a grade checker.
“The 2D system will help our customers dig footings and basements where a flat surface is needed, or dig a sloped surface for a drainage pipe,” says Hagemann.
Cat Grade Control Depth and Slope is available on excavators only from the factory. “This system can-not be installed at the dealer,” says Hagemann. “The basic advantage of having Cat Grade Control Depth and Slope installed at the factory is integration. We can route the harness out of harm’s way. We relocate the bucket sensor from the bucket linkage, which is exposed to being damaged, and put the sensor into the bucket cylinder.”
He adds, “For the operator interface, we use the standard display that is in every one of our F Series excavators. We also use the joystick switches to control the functions of the system, so operators don’t have to remove their hands from the controls to interact with the Depth and Slope system.”
A Building Block Approach
There are two advantages to the Cat system. “One is the 2D functionality and the other is the ability to use integration to add 3D,” says Hagemann. “Our dealers have told us it takes less than four hours to install 3D on an excavator that has Cat Grade Control Depth and Slope.” Without the system, a lot of time is spent routing harnesses and welding brackets. “It can take dealers up to 16 hours to install 3D on an excavator that has no technology on it.”
Cat Grade Depth and Slope makes it easy to transition to 3D. “It’s a building block to go to the full 3D system,” says Stellbrink. “It’s very cost effective even for those customers who know they want a full 3D GPS system. This system is working very well for those who are digging basements, single trench digging — task-specific jobs within a given jobsite. As you start to move around a jobsite and load plans, that’s often when customers will go to full 3D GPS, which can be built directly on top using the same sensors. The 3D GPS basically adds a radio, masts on the back of the machine, satellite receivers and one more monitor inside the cab.”
Stepping up to Automation
Building on its line of intelligent machine control dozers, Komatsu went beyond excavator guidance to provide an integrated semi-automatic excavator grade control system. “We think the North American market is ready for excavators with machine control,” says Peter Robson, director, Intelligent Machine Controls, Komatsu America Corp.
A previous challenge with machine guidance was speed and the stabilization of sensors to get to grade. In-stroke sensors provide a solution with quick response.
“The ability to rough cut out close to a design surface is really going to change how customers look at what an excavator can do,” says Robson. “We can achieve accuracy to +/- 42mm.” This is slightly more than 1/10th of a foot.
“The automation allows us to improve the operator’s efficiency and productivity,” says Jason Anetsberger, product manager, Intelligent Machine Controls. “The machine is going to limit the opera-tor from over excavating — digging below the design surface. It will also allow the operator to trace the grade automatically for a nice finish and good performance. The operator can focus on the opera-tion without having to follow a light bar or some sort of indication.”
Komatsu worked with Topcon, its collaboration partner, to develop the intelligent excavator. The 52,000-lb., 158-hp PC210LCi-10 shares the same basic specs as the standard PC210. The difference is the integrated semi-automatic grade control system. “This machine control delivers a lot of the attrib-utes and capabilities customers have come to expect from machine control on bulldozers,” says Robson.
“This machine is fully integrated and comes standard from the factory with the machine control system,” says Anetsberger. The bucket cylinder, arm cylinder and one of the boom cylinders all feature Komatsu’s stroke-sensing technology. “We are building off the same technology that we are using on our intelligent machine control dozers. We’re able to very accurately know the displacement of those cylinders so we know where the cutting edge is relative to the body of the machine.”
An inertial measurement unit is also mounted to the machine. “That sensor measures the attitude of the machine. If the machine is rolled to the side, pitched forward or pitched up, that sensor would take care of that,” Anetsberger explains.
The GNSS antennas are mounted on the hand rails behind the cab, forward of the counterweight and engine compartment. A control box monitor with a 12.1-in. touchscreen display is mounted inside the cab.
The PC210LCi-10 includes two key selectable functions: Auto Grade Assist and Auto Stop Control. With the Auto Grade Assist function, the operator moves the arm and the boom adjusts the bucket height automatically, tracing a target surface and minimizing digging too deep. On the other hand, when the operator moves the boom or bucket without arm operation, the work equipment is automatically lim-ited from damaging the target surface. If the arm is operated in combination with boom or bucket operation, Auto Grade Assist overrides Auto Stop Control. Both Auto Grade Assist and Auto Stop Control limit over excavation and allow the operator to focus on moving material efficiently.
The intelligent machine control system controls the bucket by automatically selecting the point on the bucket closest to the target surface. “One of the key features is the minimum distance control,” says Anetsberger. With conventional aftermarket machine guidance, the operator needs to manually set where the focal point or guidance point is along the bucket to calculate grade — for example, the left tip, right tip or center of the bucket. “We have those abilities with this system, as well, but we’ve gone above and beyond. We’ve offered the minimum distance feature, where the system is automatically going to calculate which point of the bucket is closest to grade.”
Consider excavating a slope. “If I come at it with the left tip closest to the slope, it’s automatically going to give me guidance to that left tip,” says Anetsberger. “If I come in at the right tip closest to the slope, it’s automatically going to change and give me the right tip without the operator having to manually select that change in guidance.”
Another feature is a facing angle compass. “To have the best finish grade accuracy, we want the cut-ting edge lying flat on the target surface. With the facing angle compass, it allows the operator to place the bucket perpendicular to the slope,” Anetsberger explains. “That might sound easy, but it is actually quite difficult if you didn’t have this tool, especially if you consider a machine sitting on an uneven sur-face. If you get some complex geometric angles going on there, this is really paying dividends in those slope-type applications.”
The system can be used with almost any excavator bucket, and allows operators to switch back and forth. You simply need to measure the critical bucket dimensions and enter them in the touchscreen display. “The operator can select between all of the pre-measured buckets on the control box moni-tor,” says Anetsberger. “To achieve the best accuracy, cycle all of the cylinders before you start work for the day. That resets everything for fine accuracy throughout the rest of the day.”
On the top right of the touchscreen display, there is a button to turn the automated features on and off, if needed. “We still have the ability to run in guidance or indicate-only mode,” says Anetsberger. “We have the readouts for elevation and the conventional light bars. We also added audio guidance. You can select different tones that play at predetermined or preset distances away from target grade. You don’t need to be staring at the control box or the light bar to know how far you are away from grade.”
Of course, intelligent machine control technology does come with a price premium. “It’s a significant premium, but it’s one that the majority of customers do see a return on investment in 12 to 18 months,” says Robson.
“There is a certain cost associated with the technology, so it needs to be utilized in a way that makes sense financially for the customer,” Anetsberger acknowledges. “The productivity and efficiency that we are seeing will result in good payback for the customer. This machine will have more capabilities for doing finish grading. That capability didn’t exist with traditional machine guidance technology.
“We’ve compared this machine against conventional operation — stakes, no GPS, no machine guid-ance whatsoever — and we saw a reduction of 63% in construction time, which is a huge number,” he points out. “Whether you are going to have that in all scenarios, it depends on a case by case applica-tion. That’s just one example of a hard figure we’ve see in our own testing here at Komatsu.”
Look for this technology to expand to other excavators in the company’s line. “The technology is very scalable,” says Anetsberger. “We are introducing it on the PC210, but there is no reason it could not be used on our larger machines.”
Total Jobsite Integration
Several jobsite integration software packages have emerged over the last couple of years. “This tech-nology marries well with the jobsite management technology out there,” says Anetsberger.
“Komatsu’s machine control excavators, when equipped with a cellular modem, are designed to integrate with Topcon SiteLink 3D Enterprise jobsite management technology. By connecting to SiteLink 3D Enterprise, the job file, targeted design surfaces and tasks can be sent to the operator at the start of the shift. At the end of the shift, as-built data can be sent to the office from the machine,” Anetsberger indicates. “The site supervisor can check progress instantly. In addition, remote assis-tance capability is provided when connected via cellular modem to SiteLink 3D Enterprise.”
As the integrated jobsite emerges, it makes sense to expand the technology through your fleet. “Where you see stakeless GPS machine-controlled dozers, adding the same GPS control automation technology to excavators is very natural,” says Anetsberger.