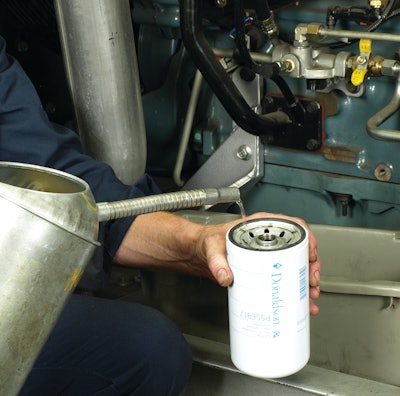
The first line of defense for equipment fluid systems is the filters. "Liquid filters are an important and integral part of equipment's critical life support system," says Brent Birch, engineering lab manager, Champion Laboratories' Luber-Finer brand. "Abrasive contaminants, oil degradation compounds and combustion by-products (for engines) must be removed from the oil to control wear and provide for a cost-effective operation."
Unfortunately, too often filters are unable to perform effectively due to lack of attention or missteps during the service process. "Most of the experienced technicians doing fluid servicing do it as part of a bigger project, and see filter changes as a necessary evil," says Paul Bandoly, manager of technical services/customer training, WIX Filters. "Or else it's being performed by the lowest guy on the totem pole."
Consequently, best practices may be overlooked, leading to problems down the road. "It's not going to sideline you within hours of use," Bandoly acknowledges. But the eventual results can be costly. "The best [scenario] is that you reduce equipment service life and serviceability. The worst is catastrophic failure of your equipment."
Start with the right replacement
One of the most common mistakes is using the wrong replacement filter. "The appearance of two filters doesn't look any different, but the capabilities can be significantly different," Bandoly points out.
In the face of budgetary constraints, it can be tempting to purchase a cheaper product that appears to have the same properties. Yet, it's important to consider overall operating costs. "Always consider the total true cost of operation over the vehicle lifetime and not just the initial filter price," advises Birch. "There are many substandard filters available that are of low cost. Unfortunately, they often are very poor performers and will not protect your equipment from accelerated wear."
That's why it's so important to follow manufacturer recommendations. "Choose filters determined by the manufacturer to be based on a direct cross from the Original Equipment Manufacturers' part number and not by size or general appearance," says Randy Thompson, field service application engineer at Donaldson. Also consider the warranty policy and service support should a problem occur.
Bandoly suggests consulting with your filter supplier on a periodic basis. "Part number recommendations change; part numbers are superseded," he points out. "At least once a year, get together with your filter supplier and validate that you're using the right part number for your equipment."
"Involve your filter and oil supplier as much as possible," adds Birch, "to achieve peak performance with your particular application."
Storage and handling
Dusty, dirty fluid filters are a contamination issue waiting to happen. "I'll go out to construction sites and see parts containers with a layer of dust so thick you could plant peanuts in it," Bandoly comments.
He notes that boxes are often opened to look at the parts or to place filters on a shelf. Any contaminants that accumulate on the filter can easily enter the fluid system during installation. "Keep boxes sealed and keep filters wrapped until they're ready for use," Bandoly advises. "Keep them stored in a clean area."
Filters should remain in their original packaging until just before they are installed on the machine. "Avoid leaving filters uncovered and exposed to contaminants during service," says Thompson.
Once taken out of the packaging, check filter condition. "Always inspect filters for any damage or missing components prior to installation," says Thompson. "Never install filters that are damaged or dented."
Filters in poor physical condition can fail prematurely. "Filters with dents and damage may not resist the pressure impulse and vibration loads as designed," Birch notes.
Premature failure can result. "If you use a spin-on filter that's damaged or dented," says Bandoly, "you're setting yourself up for a fatigue fracture."
Pitfalls of pre-filling
Pre-filling of fluid filters is a common practice, but one that can be fraught with risk if handled improperly.
"To pre-fill or not to pre-fill, that is the question," says Birch. "Pre-filling engine oil filters reduces the 'dry start' period required to fill the empty filter, which must occur before the lube system can achieve pressurization. The media is also wetted prior to being subjected to the high-velocity oil that enters a dry filter upon startup."
Problems arise when dirty fluid is introduced into the fluid system during the pre-fill process. "When filters are pre-filled through the threaded hole in the baseplate, the oil is going directly to the clean side of the filter and will not be filtered prior to its flow path through the pressurized lube system," Birch indicates.
Given today's tight system tolerances, component wear and eventual failure are almost inevitable. "The subsequent contamination created will contribute to short filter life," says Thompson. "If the filter plugs and the system goes into bypass, contaminated, unfiltered fluid can create additional wear."
Consequently, pre-filling is a good practice only when the equipment, environment and maintenance supplies are very clean, says Birch, and proper pre-fill procedures, in accordance with OEM recommendations, are carefully followed.
Installation best practices
Perhaps the most crucial step in filter replacement is to maintain as clean a service environment as possible.
According to Birch, "[You] cannot take too many precautions regarding cleanliness during oil changes and engine service. Regardless of pre-fill or not, the engine oil cap area should be thoroughly cleaned before opening that port. The cap and its gasketed sealing service should also be cleaned and lubed as required prior to re-installation."
"Accelerated component wear and, in the worst case, potentially blocked fluid passages can occur with severe contamination in powertrain or hydraulic systems," Birch points out. "Clean areas around the filters to be serviced and the fluid fill points whenever possible by washing down or wiping up any contamination in the immediate area."
"Keep bulk fill hoses clean and as free of contaminants as possible," adds Thompson.
It's also crucial that you understand how filters should be installed. "With spin-on filters, we're seeing installation instructions routinely ignored," Bandoly comments. "Cartridge filters have very defined instructions."
Part of the problem is changing installation requirements. "Gaskets, threads, baseplate geometries all evolve continuously," says Bandoly. "It's not uncommon for a product with the same part number that you bought two years ago to need 1 1/4 turns vs. one turn to install."
"Always follow the filter installation instructions silkscreened on the filter or provided by your equipment manufacturer," Thompson emphasizes.
"Don't forget to wipe dirty oil from the filter base before installing the filter," Birch adds.
Apply clean oil to the filter sealing gasket to ensure proper sealing function and to achieve proper installation torque. "To put a filter on 'dry' imparts unusually high torsional loads on the elastomeric (gasket) material, and greatly increases the potential for the filter to be in an under-torqued condition," says Birch. "Either of these cases can contribute to leakage after the unit leaves the maintenance shop or is returned to service in the field."
Installation with a dry gasket can also result in damage to the filter canister/shell by the installation tool. "Filters with dents and damage should be removed and replaced immediately," says Birch.
Care should be taken to tighten filters per instructions. "If you over or under tighten gaskets, you're setting yourself up for problems," says Bandoly. "If you over tighten, the material becomes stressed and severe compression can set in. This causes the seal to flatten and become hard, and eventually the filter loosens up."
This can be easily avoided. "When dealing with spin-on filters, the best tool in your toolbox is a Sharpie," Bandoly asserts. Because the indicators on the filter aren't always easy to see, he recommends taking the marker and highlighting where to stop torquing. "As you turn the filter to tighten it, you will know exactly how far to tighten. You will have no doubt how far it's been turned.
"The simplest way to prevent over or under turning," he adds, "is a $.99 marker pen."
For specific tips on how to efficiently change spin-on filters, view Caterpillar's How-to-Video: Change a Spin-On Filter.