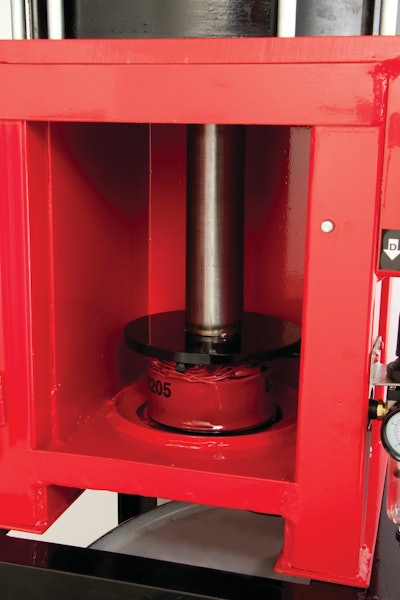
Years ago, oil filters were simply trash, and the waste oil from them was a by-product that was burned in a heater or a costly disposable that a recycling company was paid to take away. Those days are over.
Recycling scrap metal and used oil is a big business now. The question is: Are you taking advantage of the value from old oil filters and recycling the metal and used oil?
This is where the purchase of an oil filter crusher — essentially a device that squeezes all of the engine sludge and oil out of a used filter and flattens it at the same time — can be a worthwhile investment.
Dealing with Regulations
The U.S. EPA and all states have environmental regulations that affect the management practices and disposal of used oil filters. Any business that generates used oil filters is subject to these rules.
Yet, some shop owners and shop foremen scoff at environmental regulations because an agent of the government never came through their door and scrutinized their environmental practices. Even small shops are not above being slapped with fines for everything from properly evacuating refrigerant to the treatment of batteries. The way in which the government treats how waste oil is stored and disposed of is no different.
Most shops, however, are careful to follow environmental regulations, but may sometimes be unaware of the numerous regulations that govern the disposal of waste oil and oil filters. Although many states require that used oil filters be drained for a period of 12 to 24 hours, there are shops that drain oil filters for a few seconds and then throw them into the trash. These filters would be considered hazardous waste according to the regulations, so just trashing them is, obviously, improper management.
While you may not have anyone digging through your trash, there is no reason to expose yourself to excess liability. Plus, there are potential financial benefits to the proper disposal of oil filters and waste oil.
Potential Return From Waste Oil Recycling
With waste oil fetching prices as high as a dollar a gallon, and scrap steel as much as 50 cents a pound, an oil filter crusher has the potential to provide a return on investment over time.
For example, the Ranger Products RP-20FC oil filter/can crusher costs around $1,300. An average oil filter is about half a pound of steel. With two oil filters making up a pound, and a pound fetching about 50 cents in scrap metal, roughly 5,200 oil changes pays for the machine in scrap metal alone. Add to this the profits gained from recycling the increased waste oil that is squeezed out.
Depending upon the vehicles and equipment in your fleet, larger motor oil and transmission oil filters may hold as much as a pint of fluid that cannot be easily drained. Crushing eight filters using the RP-20FC yields a gallon of waste oil, with the subsequent return on investment.
An easy way to determine if your shop will have quick or slow ROI is to look at how many oil filters you buy in a year. If hundreds of oil changes and transmission services are performed a year, chances are that the ROI for the oil filter crusher would be relatively quick.
How Filter Crushers Work
Most oil filter crushers essentially function in the same way. The device presses the filter under high pressure and squeezes the oil out and into a storage container. Filters are then crushed to about a quarter of their original size and deposited into a drum.
The more the oil filter can be crushed, the more money that can be made from selling the waste oil. The scrapper might also give you a higher price for the steel, since more filters can be fit into a truck with less mess.
Modern oil filter crushers connect to an existing shop air supply and use that to derive the force necessary to crush an oil filter. For example, the RP-20FC applies 10 tons of pressure, reducing the oil filter to 25% of its original size. The unit includes a 12 1/2-in.-diameter cylinder, pressure regulator and air moisture separator, and an automatic safety door that automatically ceases press operation when opened. A transparent door provides a view of the crushing process.
In order to use an oil filter crusher safely, make sure that the door remains closed at all times during the crushing operation. When choosing a filter crusher, it is wise to purchase a unit that has a door with an integrated safety switch that automatically stops the press if the safety door is ajar. A feature like this makes accidents much less likely.
A Pressing Matter
To get the most for your money, it’s wise to choose a filter crusher that meets the needs of your business model. Some bearing presses can be retrofitted into oil filter crushers, but they suffer from being hand-operated and messy. This hampers ROI because of labor and cleaning costs.
There are larger crushers that can crush larger cylindrical metal objects, such as paint cans, but most shops would need a crusher that simply compacts oil filters. How do you know which type to choose?
According to Jeff Kritzer, senior vice president of sales and marketing for BendPak, prices for oil filter crushers tend to vary based on the pressing power generated — 10 tons vs. 25 tons — and the power source. Beyond that, there are no major differences between the crushers available.
“The only real variances are whether the crusher is pneumatic or hydraulic powered, its pressing power and the overall chamber size,” he states. “Pneumatic presses are usually less expensive and have fewer operating parts and require less maintenance. Pneumatic presses are typically medium-duty presses with capacities ranging from 10,000 to 20,000 lbs. of crushing force.”
A shop that typically services light-duty and some medium-duty vehicles and equipment typically needs an oil filter crusher capable of a maximum of 20,000 lbs. of crushing force.
“For heavier duty pressing, hydraulic presses that feature an electric/hydraulic power unit and hydraulic operation valve with higher crushing forces ranging from 25,000 to 50,000 lbs. of crushing force are preferable,” Kritzer indicates. Heavier diesel equipment repair shops should explore crushers with a minimum capacity of 40,000 lbs.
Craig Truglia is assistant editor of Professional Tool & Equipment News. For more information, visit VehicleServicePros.com.