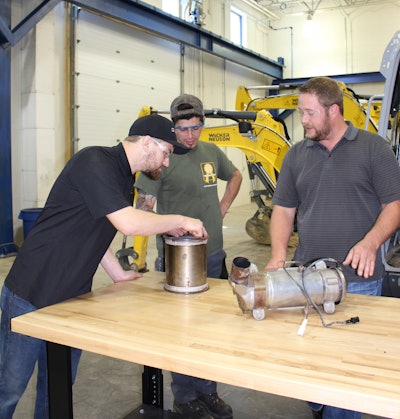
The complexity of current diesel engines, driven by ever-tightening emissions regulations, may require adjustments to your approach to maintenance and repair. While in-house technicians can provide an efficient solution for basic maintenance, any type of repair work beyond the most basic may need to be handled by factory-trained dealer technicians who have access to proprietary tools.
“The previous tier-rated range of engines included technologies that have become more complex with each new generation through the use of electronic engine controls, variable turbos and high-pressure electronic pumps that have mutable sensor inputs to maintain proper emissions output,” says Mark Coberly, East Coast general service manager, JCB North America. “These new components and complex electronic controls mean that each service technician needs training from the different engine suppliers, as each supplier has used different technologies to reach each tier level.”
Furthermore, each engine manufacturer/supplier uses its own specialized diagnostic tools for troubleshooting. “To ensure maximum machine uptime, thorough, specific training has become very important to dealers and customers alike,” notes Coberly.
Aftertreatment systems have become a game changer. “Additional training is needed and recommended for Tier 4 Final machines because they have aftertreatment systems that didn’t even exist on Tier 3 machines,” states Craig Timmerman, product marketing manager, John Deere Construction & Forestry.
Proprietary service software is now a reality. “Tier 4 Final engine service requires specialized diagnostic tools and software, which can differ from one manufacturer to the next,” says Jake Gaylord, technical training manager – North America, Wacker Neuson. “The proper use of this diagnostic technology is best gained through specialized training, and is essential for successful troubleshooting.
“However, no repair ends with troubleshooting, and the use of these tools doesn’t end there either,” he continues. “When a new electronic component is installed, it may require calibration or programming before the repair is complete. For example, if a fuel injector fails on a Tier 4 Final engine, the technician must use a computer program to ‘tell’ the electronic control module (ECM) how the injector should work. If the injector is not calibrated properly, the ECM will not be able to control or monitor the injector. In many cases, without the proper tools and training, most repairs cannot be completed successfully.”
Continual Training Required
Technicians who work on diesel engines must keep up with the rapid pace of technology.
“Diesel engine technicians who service Tier 4 Final equipment require additional training, especially if they’ve only worked on older engines in the past,” says Brad Stemper, solutions marketing manager, Case Construction Equipment. The emissions solutions differ depending upon the size of the machine, the application and the particular OEM.
With each solution, it’s important to understand what the machine is communicating to the operator and technician. “Each system is going to come with a different set of warning lights based on the emissions solution used,” says Stemper. “In SCR (selective catalytic reduction) machines, these will revolve around diesel exhaust fluid (DEF) levels, DEF quality and the overall operation of the SCR system. In equipment with diesel particulate filters (DPFs), these lights will revolve around the type of regeneration required and the overall functionality of the system.
“It’s critical that both the operator and the technician understand what those indicator lights mean,” he emphasizes. “For the operator, ignoring the warnings can cause a number of issues that include de-rating and additional downtime if the regeneration isn’t allowed to take place, or if the DEF level is getting too low. For the technician, they need to be able to communicate to the operator and the equipment owner what those indicators mean, because if they don’t, that could lead to customer downtime related to Tier 4 maintenance.”
Before servicing any equipment, technicians should have a thorough understanding of that particular unit’s aftertreatment system and its warning or condition indicators.
“In fact, anyone directly related to the operation and maintenance of the machine should possess this knowledge,” says Gaylord. “Oftentimes, system warnings can be resolved with simple service regeneration. However, if a condition or warning is ignored or misinterpreted, it can result in costly component failures and machine downtime. This knowledge should be taught at every level of an organization that uses Tier 4 Final engines in its day-to-day operations.”
“Warning lights and diagnostic trouble codes are key tools for a service technician to fix an issue on a Tier 4 Final machine,” Timmerman agrees. Given that many John Deere machines have built-in diagnostics that will help identify problems, it may be possible for an internal technician to repair items such as broken wires or damaged components with proper training. “If the problem is more complicated, John Deere dealers are trained and equipped with tools to help fix the problem.”
It takes more than a basic understanding of the system for many repairs. “Internal mechanics should have a basic understanding of the system. However, the OEM-trained mechanic is more likely to have the correct tooling and parts needed to properly troubleshoot the system,” says Rhys Eastman, director of service, training and warranty, Volvo Construction Equipment.
Compact Equipment Solutions Vary
Compact equipment falls at a critical horsepower breakpoint where a wide range of emissions solutions often apply.
“Generally speaking, most engines under 75 hp will use diesel oxidation catalyst/diesel particulate filter (DOC/DPF) solutions to reach emissions compliance,” says Gaylord.
However, even these solutions vary. “Each manufacturer has addressed equipment in that operating range differently,” says Stemper. “On the vast majority of machines below 74 hp, Case has elected to use a particulate matter catalyst, which is a DOC with a high-efficiency flow-through filter.”
A DOC proves a simple solution for many compact machines. “Barring any physical damage caused by force, incorrect maintenance practices or some other abnormality, DOCs are maintenance free and designed to last the life of the machine without replacement or any regular service intervals,” says Stemper.
But engine-related problems can affect DOC performance. “Engine failures (bad rings/blown turbo) could cause DOC failures,” Gaylord acknowledges. “The DOC needs to reach a minimum temperature in order to ‘light off.’ If the engine is only run at low loads for short periods of time or in extremely cold environments, the DOC could never reach the intended temperature and then you would have a need for maintenance.”
JCB uses an advanced combustion system with an exhaust gas recirculation (EGR) valve and cooler to meet Tier 4 with its 74-hp Ecomax engine. “Maintenance on the 74-hp engine is the same as on the Tier 3 engines, but you want to ensure the machines are cycled monthly to maintain proper operation on the valve,” says Coberly. “EGR valves can seize if not cycled. One other item is to check the crankcase ventilation filter, which should be changed every 1,500 hours or one year of operation on a JCB unit. This can be completed without dealer assistance.”
SCR Requires Proper Training
SCR systems are used by the majority of OEMs for engines greater than 75 hp. These systems have many benefits, but are finely tuned and more complex.
“Improper repairs can result in complete system failure, resulting in costly replacement and machine downtime,” says Gaylord.
All SCR-related repairs should be completed by factory trained technicians who can ensure proper repairs, operation and emissions compliance.
“These are specialized systems that, if damaged, can void warranties and render the emissions solution inoperable and cause further downtime or de-rated operation,” says Stemper.
SCR systems are particularly sensitive to contamination in the DEF. “If any signs of contamination are found in the tank, you must drain the tank of all fluid and dispose of it properly in accordance with local laws,” advises Coberly. “Thoroughly clean the tank with distilled water or DEF tank cleaner. Flush the tank thoroughly, drain and refill with new DEF fluid. If the contamination is severe, it will require a complete flushing of the system to ensure proper machine operation. Flushing of the system should be completed by a trained dealer technician.
“DEF fluid quality is extremely important to the performance of the DEF system,” he adds. “DEF is injected into the exhaust stream where it mixes and reacts to NOx and changes it into harmless nitrogen and water. If the DEF quality doesn’t meet industry standards, it can cause serious damage to the system and require servicing.”
It’s crucial to understand and follow proper DEF handling practices. “DEF handling and storage is extremely important for both the operator and the technician,” says Eastman. “Also, it is vital that the refill area on the machine be cleaned of all possible contaminants prior to refilling the DEF.”
“Precautions should always be taken to handle and transport DEF in approved containers,” Stemper adds. “We suggest equipment owners not re-use open containers or mix their own DEF.”
DPF Filter Service
Many emissions solutions include a DPF that will eventually need to be serviced. It should be cleaned or replaced based on OEM recommendations.
“All DPFs need to be cleaned on a regular basis regardless of horsepower range, as debris ranging from ash, engine oil, wear metals and air-induced dust will remain in the filter substrate,” says Coberly. “Soot and other organic compounds are removed during operation by oxidation. The cleaning intervals vary depending on the condition of the engine/product and its duty cycle.”
Several factors determine how long a DPF will operate before service. “One is the overall surface area of a DPF,” says Gaylord. “The larger they are, the longer they last (typically).” The condition of the piston rings and the amount of idle time can impact the overall service life.
“All DPF systems are designed to run past the minimum government requirement,” says Eastman. “DPF cleaning is largely impacted by application and engine load. For example, an engine with high and constant load will have a longer cleaning interval compared to an engine with low load and high idle time. Service life of the DPF is not based on hours. The system is computer monitored.”
“The hour level at which the DPF will need to be cleaned is condition based, meaning it will vary based on machine usage,” says Timmerman. “The time this service should actually be performed will be flagged by your machine with a monitor indicator, or as required by diagnostic codes. Field results on John Deere machines equipped with a DPF have shown this service is often not required until the first major engine overhaul. Actual intervals will be a result of your specific machine application and regular maintenance practices, such as the lube oil used.”
Several dealers offer filter exchange programs, since cleaning must often be outsourced.
“DPF cleaning is not something construction equipment dealers often do. It’s very expensive to buy the machinery and would require doing dozens per month to justify the expense,” says Gaylord. “These systems are costly to install and require specialized training to operate.”
Relying on Dealers
Forming a partnership with your dealer is critical to successful Tier 4 equipment uptime.
“Partnering with your dealer for preventive maintenance and granting the dealer’s service department visibility into telematics data is important, especially for smaller to mid-sized fleets that may not have professional technicians on staff,” says Stemper. “Telematics, especially viewed by a trained diesel engine technician, can help raise red flags that may tie back to the emissions standards and allow the dealer to address them before they become larger issues.”
Dealers are also best equipped to handle the latest advancements. “With any computer-based system upgrade, the OEM mechanic will be provided with the necessary tools and training to not only correct any potential issues, but reduce any customer downtime,” says Eastman. “Volvo makes sure that its dealers are provided the right tooling and training so their technicians are successful. With every advancement with engine systems — be it Tier 3 or Tier 4 Final — training and tooling is paramount to a successful repair.”