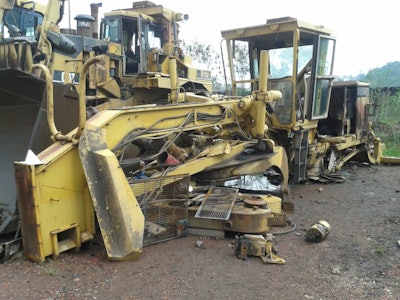
Machine and component rebuilds for heavy construction equipment are part of many contractors’ fleet management plans. Today, contractors target tens-of-thousands of operating hours, multiple service lives and low total cost of ownership (TCO) from a machine by implementing a regimented maintenance plan and multiple machine rebuild strategies.
“Service departments consistently following the machine’s suggested maintenance schedule, oil sampling guidelines and monitoring telematics data will typically realize the lowest total ownership costs,” comments Dave Matranga, a Caterpillar market professional for engines and Cat Certified Rebuilds (CCR). “Include a rebuild strategy into the mix, and companies can drive down TCO even further.”
Caterpillar 16H after rebuild
Caterpillar is celebrating the 35th anniversary of its CCR program this year and closing in on its 5,000th complete machine rebuild. In the past, the typical CCR machine rebuild included approximately 7,000 part numbers either replaced or refurbished. Over time, trends showed better maintained and operated equipment resulted in more reusable parts, lowering machine rebuild cost.
What’s the Standard?
Baptiste recommends working with the dealer even before machine purchase to review applications, how long it is anticipated to remain in the fleet and the company’s expectation for uptime availability. This allows the dealer to run a life-cycle analysis and have targeted maintenance and rebuild solutions planned.
While some may assume that all rebuilds are equal, this is not the case. When it comes to rebuilds, selecting a provider just on initial price-point can sacrifice post-rebuild machine life and productivity.
Over the years, manufacturers have developed rebuild standards. For example, Caterpillar provides its dealers with detailed reuse and salvage guidelines specific to machines like dozers, excavators, trucks and loaders. These documents guide dealers through properly inspecting components for reuse or salvage, based on extensive rebuild history and conservative criteria. This is designed to provide more consistent rebuild results, regardless of where it is performed.
All switches, harnesses and sensors are also replaced during a rebuild. “The highest equipment downtime drivers are miscellaneous items like sensors and switches, so our guidelines require these be replaced,” Matranga says.
Advanced Monitoring
Monitoring machine performance plays a critical role in helping to extend a machine’s service life and rebuild intervals. This begins with the basics of following the prescribed maintenance intervals and having a well-trained operator communicate any issues with the shop.
“Our goal is to have companies catch issues at the Level 1 parts stage, which are parts designed to wear, are not rebuildable and protect the more expensive machine components that can be rebuilt,” says Eric Mathewson, senior parts specialist for Caterpillar undercarriage and ground engaging tools (GET). “Catching issues early increases uptime availability and drives down the TCO.”
Routine fluid sampling provides insight to internal component wear and potential failure. This data analysis allows contractors to plan for any necessary component repair or rebuild.
“Trends like increased metal fragments in the oil give an owner the necessary data to make proactive service decisions,” says Matranga.
A machine’s duty cycle in the field, rather than machine hours, offers a better indicator of service life and rebuild interval frequency. Advanced monitoring of field fleet equipment through telematics provides insight as to how a machine is used in the field.
“We track fuel burn, which is a key indicator of the machine’s workload,” says Matranga. “The higher the fuel burn, the higher the workload and the shorter the time period is between rebuilds.”
Matranga also points to recent developments in remote services as the next evolutionary step in digital machine monitoring to catch field issues early, extending time between rebuilds and lowering TCO.
“Our dealers can now run diagnostics remotely through Cat Remote Troubleshoot and analyze real-time data to help reduce equipment downtime,” he explains. “It’s also possible to upgrade a machine’s latest software remotely through Remote Flash.”
Consider Upgrades
The term “like-new” means just that to many manufacturers, as they push the boundaries of rebuilds beyond refurbishing or replacing the machine’s core components. For example, Caterpillar dealers offer customers the latest technology, wear parts and service updates available for a machine. This way, the rebuilt machine is expected to perform like a new piece of equipment coming off the assembly line.
Several updates are automatically included during a rebuild performed by the dealer. “Cat Certified Rebuilds (CCR) automatically receive appropriate updates that involve machine safety and critical performance upgrades,” says Baptiste. “For less critical engineering upgrades, customers can add those as options at the time of rebuild.”
Mathewson advises companies not to ignore the working end of the equipment. Wear strips and work tools that protect the more expensive components are continually upgraded by manufacturers.
“Our new hammerless GETs fill the bucket more efficiently and usually require about half the time to change, so upgrading work tools to get more from a machine is a worthwhile discussion to have with the dealer during a rebuild,” he says.
The evolution of emissions standards has resulted in significant efficiencies in engine design, allowing them to last longer and, in some cases, save a considerable amount of fuel. “One customer upgraded from a Tier 2 to Tier 3 engine, and the fuel savings alone led to a return on investment, in this case, of about 1.5 years,” says Baptiste.
A rebuild is also the right time to approach the dealer about available technology upgrades to optimize machine efficiency. Manufacturers continually upgrades production-enhancing solutions like semi- and fully autonomous machine operation, grade, slope, and payload technologies.
“Our technology is backward compatible within a model series, so an earlier model receiving a certified rebuild can be equipped with the latest technology,” says Matranga.
Whether it’s to extend a machine’s service life, lower TCO or enhance production efficiency, certified rebuilds offer contractors another avenue for getting a “like-new” machine at about half the cost of purchasing a new machine. “Certified rebuilds should be considered as a part of a company’s fleet management strategy,” Mathewson encourages. “Equipment dealers will be able to walk customers through the rebuild process and help them get the most from the rebuild.”