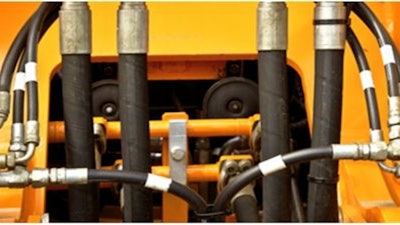
Originally published on Chevron Lube Matters blog
When lubricant sales representatives discuss hydraulic failures with maintenance managers, the conversation typically focuses on extending the life of the hydraulic systems (valves, cylinders, pumps, hoses). Since it is widely accepted that particle contamination in oil is one of the major causes of component failure, there is great validity in the fact that failures can be delayed or even avoided when lubricant cleanliness is properly addressed.
When a customer decides to proceed with a clean oil program, it begins by determining the correct ISO 4406 cleanliness for component. To simplify the target for the system, use the specification for the component with the tightest ISO cleanliness specification as the standard for new oil being delivered. This is what we call validating the third specification for your oil, as everyone knows how important the viscosity grade and performance properties are.
Overlooking this third lubricant specification, however, has dire consequences. While new, pre-filtered oil costs an incremental amount more, it offers a greater cost savings overall — through increased valve, cylinder, pump, hose and seal life.
Multiple OEMs have reported the benefits of clean oil, which are reduced component wear and extended rebuilds, leading to decreased downtime and reactive maintenance tasks. That said, asking for an increase in operating budgets can be challenging.
First, maintenance personnel may not be tracking their failures or identifying RCAs (Root Cause Analysis) as to why failures are occurring. Rather, maintenance staff become accustomed to changing out the failed parts on a more regular basis and come to except this status quo as the norm for their operation.
Also fueling the status quo, many industries that employ maintenance and repair workers must deal with frequent turnover. Employees who are exposed to an unsafe environment, or at a shop that can’t stay on top of its tasks, are more likely to leave. Thus, reducing unscheduled activities not only has a direct impact to the bottom line, it can also improve shop morale.
But even if you aren’t convinced that oil cleanliness can save money or improve morale, as a maintenance manager the thought of a critical hydraulic system failure will keep you awake at night. Whether in-plant, on a construction site or in an underground mine, if you have hydraulic equipment, you have plenty of maintenance to think about, both scheduled and unscheduled.
Another common frustration with hydraulic systems is leaks. This, too, has some shops thinking it is normal and unpreventable. As maintenance personnel will attest, most of those leaks occur at rigid-to-flexible fittings where O-rings have simply failed. What many don’t take the time to quantify is that small leaks add up quickly.
Looking at the chart below, one drop in 10 seconds doesn’t seem to add up to a significant amount, but imagine this was occurring with 25 out of the 100 hydraulic systems on site, which would add up to 1,000 gallons a year. Multiply that loss by the cost of your hydraulic oil, let’s say $10/gallon for example, that would mean a $10,000 annual loss. Does it make sense to take that $10,000 annual loss and reinvest it in a clean oil program?
Chevron
During an evaluation to uncover the cause of one customer’s high fluid leak rate, Chevron’s team of Industrial Specialists discovered a customer was leaking nearly 800 gallons of oil per day. Instead of addressing the root cause issue — contamination — the location opted to collect the leaked oil, attempt to reclaim it and use it again. This was costing the company $150,000 in maintenance practices.
Although there is limited test data available linking the shortened life span of O-Rings to higher levels of particulate contamination, we have customers who have seen firsthand that such contamination is responsible for the abrasive destruction of the elastomer material degrading its ability to seal effectively. Constant abrasive activity essentially sand blasts the system and degrades the softer O-Ring material leading to seal deterioration, leaks and premature component failure.
Of course, a leaky O-Ring may or may not be considered significant, depending upon which hat you’re wearing. The engineer might point out that an O-Ring is designed to be replaced and probably costs only a few dollars. But the maintenance manager is thinking about how many man hours the repair will take, what parts must be disassembled to access the failed seal, the opportunity cost associated with the down time of an entire line, and finally the lockout tagout process to isolate potential energy so that the necessary human-machine interaction can be accomplished safely. On top of that, they must balance their workload with their budget.
Overall, it is safe to say particle contamination wreaks havoc on components which can lead to extreme leaks, headaches, and not to mention exposure to safety issues (like slips, trips and falls). If you want to calculate the cost of your fluid leaks, check out Parker Hannifin Corporation’s Oil Leak Calculator.
Conventional wisdom would suggest that preventive maintenance is a proactive approach, in which cost is justified as it will reduce premature equipment failure when done properly. Perhaps a more innovative approach is to aim to improve your equipment life from the very beginning, by ensuring your oil starts clean and stays clean.
Since joining the company in 2000, David Hasch has held various roles at Chevron including direct sales representative, supply chain production planner, and lubrication engineer in Chevron Lubetek where he provided technical support for lubricants across the globe. In his current position, Marketing specialist, he creates technical content to help showcase the company's products and solutions across all commercial and industrial market segments in North America. David graduated from the University of Louisville with a Bachelor of Science in Urban Geography and GIS Technology. He earned his CLS in 2014 and is fluent in Spanish and Portuguese.