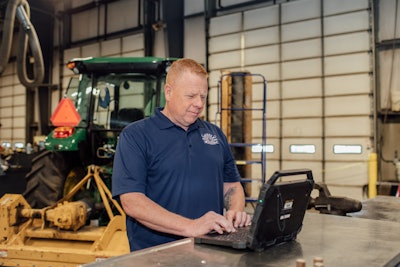
From small, heavy and specialty equipment to personal protective equipment (PPE), fleets can take advantage of digital inspections in fleet management software (FMS) to create custom asset inspections, helping employees and managers catch mechanical issues before they snowball into costly problems and impede productivity and profitability.
Failed items on digital inspections automatically send alerts to anyone assigned to that piece of equipment, including technicians and management, so action can be taken quickly and maintenance can be scheduled.Fleetio
Why Inspections Matter
The process of daily, pre- and/or post-trip inspections can be frustrating for all parties. It’s monotonous and can lead to instances of pencil-whipping, making the data unwhole and unreliable and leading to costly repairs. Unfortunately, this happens — and it can happen fairly frequently for fleets still using paper inspection forms. Using paper inspections presents another issue that can lead to unreliable data, and that’s data entry mistakes.
Inspection data can be very useful when documented and collected reliably and when issues are promptly communicated to technicians, operators or managers — whoever in the workflow needs to know. By providing clear communication around failed inspection items, fleets can quickly take the necessary actions to resolve the issue before it escalates. If failed inspection items go unnoticed or unreported, however, it can cost the business in fines, downtime, profitability and brand reputation.
Equipment managers can use custom digital inspections in FMS to tailor inspections to specific assets, or even groups of assets by type, manufacturer or age/usage, to easily bulk add inspections to asset groups.Fleetio
Digital Inspection Software
Equipment managers can use custom digital inspections in FMS to tailor inspections to specific assets, or even groups of assets by type, manufacturer or age/usage, to easily bulk add inspections to asset groups. Inspections can also be set at custom intervals, such as seasonal versus daily inspections. Because FMS collects and consolidates both equipment service and inspection histories, managers can uncover high-fail components and add those components to a routine inspection for the appropriate assets. Managers can also use this data to uncover parts brands that aren’t holding up well to daily operations.
Additionally, digital inspections in FMS help fleets mitigate instances of pencil-whipping in several ways. Digital inspections are timed, they track entry locations and they can be set to require photos and/or comments on inspection items. Managers can also include instructions on inspection items to ensure the employee knows how to do a proper inspection and specific things to look for. Plus, tailoring custom inspections to specific equipment takes a lot of the clutter out of the inspection process, making it faster and more proactive.
Failed items on digital inspections automatically send alerts to anyone assigned to that piece of equipment, including technicians and management, so action can be taken quickly and maintenance can be scheduled. Stanley Steemer, one of the largest carpet cleaning companies nationally, cut down time spent on inspections from roughly an hour to 10 minutes, a reduction of more than 83 percent, while customizing inspection forms based on compliance, vehicle and equipment requirements.
Inspections for Proactive Maintenance
Whether the fleet is using self-propelled cranes, power shovels or air compressors — or even electrified skid steers, there’s a lot of specialty equipment that can benefit from routine inspections. Reliable inspection data isn’t just good for staying on top of issues, though. It’s also good for being more proactive with maintenance. Using inspection reports in FMS allows managers to surface recurring issues and high-fail items on specific pieces of equipment. Those items can then be added to preventive maintenance (PM) schedules as needed to reduce repair and breakdown instances and associated costs and improve the useful life of equipment.
Reliable inspection data isn’t just good for staying on top of issues, though. It’s also good for being more proactive with maintenance.Fleetio
Inspections for PPE
Many types of PPE need regular maintenance, and because different PPE has different maintenance requirements, it can be difficult to effectively track and monitor each piece. Fleets can use FMS to customize digital inspections for all types of PPE.
A large portion of PPE maintenance is knowing the signs of wear and tear, damage and equipment faults, so managers should communicate these signs with their employees, either verbally or by providing instructions in the inspection tasks. Custom inspections can include things like rips, tears, fraying, breakage, sun damage, loose stitching/thread, cracking, sharp edges and more.
Employees can complete inspections with a mobile device and, like with other digital equipment inspections, results from submissions are uploaded in real time, and failed inspection items automatically alert management.
Inspections for Improved ROI
Digital inspections in FMS help improve accountability within the fleet. Because FMS automatically collects, consolidates and aggregates fleet data, including asset assignments and inspection compliance rates, managers can more easily surface and source ongoing issues. For instance, if a driver is experiencing a high-fail item consistently, it could be a driver behavior issue. Or, if a high-fail item occurs frequently across all of a particular make model year (MMY), there could be an OEM issue.
Knowing the source of issues enables fleets to be proactive in maintenance, equipment purchasing, replacement part purchasing and coaching and training employees around operating equipment safely. Proactive maintenance extends the useful life of equipment, reduces expenses related to repairs and breakdowns and increases productivity, which typically equates to profitability for that piece of equipment. Digital inspections in FMS provide a solution for disparate data, manual data entry and paper forms, better ensuring fleet equipment is consistently operating smoothly and under budget.