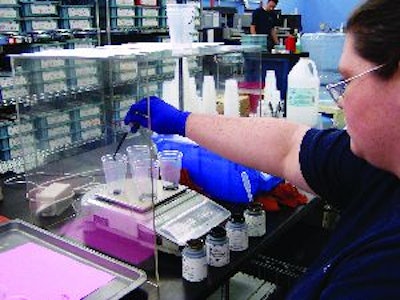
Oil analysis is not new, yet many contractors under utilize it. "I would say 25% of our customers are using oil analysis," estimates George Wacaser, product support manager for Martin Equipment, a John Deere dealership headquartered in Goodfield, IL, and serving Central Illinois, Eastern Iowa and Central Missouri.
While numerous customers are starting to use oil analysis, most are not yet getting the maximum benefit out of these programs. "I think the future is going to be extending out oil intervals and using oil analysis to really maximize your maintenance," says Wacaser. "That's when you have everything else under control and know exactly what you are doing. Then you can go to the next step."
To get the full benefit of fluid analysis, you need to get beyond thinking of just engine oil. Dave Nycz, Caterpillar, points out, "Oil analysis gives you an idea if there is anything abnormal going on with any of the fluids. We look at engines, transmissions, axles, final drives and cooling systems. It is like a blood sample at a doctor's office. It gives you a general idea of the health of all of those compartments."
Walt Silveira, North American technical manager for Shell Lubricants, adds, "We always talk about oil analysis, but the other key to this is a coolant analysis program, especially in large pieces of equipment where the cooling system is critical to the operation of the engine." Combining the use of extended-life coolants with coolant analysis can dramatically reduce the maintenance of managing these systems.
Get more ROI from your program
An effective fluid analysis program can deliver numerous benefits. "Fluid analysis ? including analysis of engine and hydraulic oil ? aims to drastically reduce catastrophic downtime, optimize drain intervals and save the construction contractor money," says Diego Navarro, John Deere service marketing manager. "Oil analysis is a very powerful tool for contractors because it lets them know in advance what maintenance problems might be on the horizon, giving time to fix the problems before they translate to downtime."
He continues, "Through oil analysis, we can discover that parts are wearing abnormally on a piece of equipment; the contractor is using the wrong types of fluids or mixing fluid types; there are environmental factors at play, such as temperature, water or dirt; or there are abnormal amounts of contaminants, both externally (such as water and dirt) and internally (such as glycol or sulfur from fuel). Oil analysis goes to finding the root causes of problems. So oil analysis helps to avoid larger maintenance problems."
The benefit is reduced equipment downtime. "If you can catch things like coolant leaks or dirt entry early, you can make the repair and get the machine back in service," says Nycz. "There is no permanent damage."
However, the return you realize on oil analysis really depends on what you put into it. It starts with the oil sample. According to Wacaser, a good portion of "bad" samples are the result of improper sampling. "A good share of the time, we take a sample a second time and find there really is no problem," he notes.
This is where an investment in oil sampling ports can pay a huge dividend. "The more devices those machines have to simplify the oil collection, the quality of the samples will go up dramatically," says Wacaser. "Taking a good sample without a sample valve is a pretty good art. It is difficult to do in the dirty environment those machines run in."
Maximizing the value of the results means accurately tracking the history. "The key to oil analysis is trending," says Silveira. "A good oil analysis software program really helps."
It also helps to know the metallurgical makeup of the engine. "Many engines are similar, but some are different," Silveira comments. "As we go to newer technology engines, [it helps to know] if it is babbit or bearing wear vs. liner wear vs. ring wear... In many cases, the OEM can provide you with [the information] to assess where those metallurgical families line up with the engine. You may be able to diagnose something sooner than later."
You also need to understand what drives failures. "In the past, we always just looked for wear metal. What we are finding is that wear metal is really the result of other things, it is not the cause," explains Wacaser. "So now we look at the quality of the oil, the mixing of the oils and how long it has been in the machine... We are trying to get back to causes, not react to wear."
Consider the oil's viscosity, as well as the Total Base Number (TBN), which is the reserve capacity for acid neutralization. "You can look at that and you know how many hours you can run that oil without doing any damage whatsoever," says Wacaser.
Oil analysis can also be used to spot when the wrong products end up in a certain component. "Some people are taking it to the next level, where they are watching the additive concentration in oils," says Silveira. "Depending upon the additive makeup of the oil you are using, it helps you determine if the oil was contaminated." For example, say the oil doesn't contain zinc, yet it shows up in the oil analysis report. "Somebody may have topped off with a different oil, like a hydraulic oil."
Costs vs. benefits of extended drains
"Condition-based maintenance requires a very structured testing program to ensure you are doing the correct testing at the correct time," says Jason Papacek, data analysis manager and certified lubrication specialist, POLARIS Laboratories. "You also have to consistently review your reports, read the recommendations and take action when necessary. A reporting software application can help you manage the data across your fleet, as opposed to one report or unit at a time. How effectively you sample and react to data will determine how much you can benefit from a condition-based approach to maintenance."
Nycz reports that the number of customers currently optimizing oil drain intervals is a small portion of the population. As petroleum prices and disposal costs increase, there will be more of a demand to optimize oil drains. However, the fluids and filter costs are still a small piece of the overall operating cost of the machine when you consider fuel, operator, tires, tracks and other items that wear out and need to be paid for on an hourly basis.
In addition, oil drain optimization is only for the very well-managed fleet. "The real key is whether or not the customer has the discipline to do the job correctly," says Nycz. Do you really drain your oil today at regularly scheduled intervals, or does it sometimes creep up 100 or 150 hours? "A customer that doesn't have a good maintenance program is likely to drift off and get himself into trouble. Also, don't try this if you have a fleet full of machines that are falling apart or are badly in need of an overhaul."
Another consideration is the timing of the service intervals. You don't want the extended service interval on one component to lead to servicing of other fluid compartments out of sequence. "It is so expensive to send a person out there to take a sample or to change a filter that a lot of times they will just change the oil," says Nycz. "You still have to consider your service time."
To determine if it makes sense, weigh the increased risk against the benefits. "We would advise anyone who is going to do this to actually calculate how much money you are going to save in your particular fleet," says Nycz. "Throw the numbers into a spread sheet and figure out how much you are going to save on oil, disposal costs, service costs. Consider that you are taking a bit of a risk and see if you are willing to take that risk for $10,000, $30,000 or whatever that number may be."
Important points to ponder
Optimizing oil drains is not something that can be done overnight. "Extending drains is a process," says Papacek. "Work with your lubricant supplier to determine realistic expectations, then test at various intervals to find the optimum interval. You may find you change the oil less often, but you should test more often to effectively monitor the affects of the extension. Caution should be taken to control the type of lubricant being used. Be sure the proper lube is also used when topping off."
The amount of top-off oil also needs to be carefully tracked. "If you are not measuring your oil makeup, you may not truly understand what the numbers are telling you," says Silveira. Consider the case of an engine using 5 gal. of makeup oil between extended drain intervals. "The actual numbers you are looking at are very skewed. That fresh oil dilutes the value of the numbers. So knowing your oil consumption is important if you are trying to extend out oil drains."
He explains, "If you have a unit that is consuming twice as much as another unit, your TBN and TAN levels will definitely be different because you are refreshing the oil." The added oil will also mask the true contamination level. "Understand that 100 ppm of silicon in an engine that is using more oil is actually a more severe number than in an engine that is not consuming as much oil."
Oil quality is also very important in oil drain optimization. "The use of a synthetic or premium oil will certainly help in extending drains, but they cannot replace good maintenance practices," says Papacek. "Proper storage and handling procedures must be in place and steps should be taken to minimize contamination. If you are using a rusty pail to transport hydraulic fluid from a storage receptacle to your equipment, a premium or synthetic product is going to be just as susceptible to contamination. If fluid storage is unprotected from the elements, water is going to be just as damaging to a premium product as it is to a lesser product."
Silveira adds, "Full synthetic oils do offer some advantages in wear performance, deposit control and cleanliness of the engine. But then you also have to look at the conditions they are operating in. Even synthetic oil will not handle dirt or water. Coolant, fuel and other contaminants ? a full synthetic will not protect the engine from these."
Keeping the oil free of contaminants is critical to extending oil drains. "I think over time you will see bypass filters ? in other words, extra cleaning devices ? on both engines and hydraulics," says Wacaser. "I have two machines right now that are running 1,000-hour engine oil changes. The oil samples prove there is absolutely no detrimental effect to the engines on these two machines running with oil bypass filters. They are actually large loaders in a mining application."
There are some applications where extending oil drains isn't even an option. "Part of deciding if you can even do an extended oil drain program is looking at where your fleet is right now," says Nycz. "Your baseline has to show some potential."
For instance, engines operating at high altitude run hotter, generate more soot and are harder on engine oil. "So if you have a fleet of machines on a mountain top and the oil doesn't look great at standard drains, then you certainly don't want to start extending oil drains on that fleet," Nycz states.
You may even determine that a shorter drain interval is more appropriate. "You might find out that you need to reduce intervals of oil changes, but you will save money on replacing components damaged by contaminated or poor performing oil," says Navarro.
Eliminate guesswork
Technology may actually take some of the guesswork out of extending oil drain intervals. The advent of GPS equipment tracking is going to allow some significant changes.
"You can get the fuel usage off any of the new machines," says Wacaser. "I no longer have to rely solely on hours. I can look at load. The load on the engine in a diesel will determine exactly how many gallons of fuel are going through it."
He adds, "I can look at the total fuel usage and determine on a specific machine that 300 hours may be the time to change the engine oil. On another machine, it may be 500 hours. It all depends on the machine and the application. It really doesn't depend on the hours if you want to get the maximum out of everything."
For example, an excavator that runs at a 50% load factor will wear out the oil additive package faster than one that runs at 20%. "It is all related to temperature, pressure and moisture in the oil," Wacaser explains.
Ultimately, oil optimization is a risk some contractors with very good maintenance programs may want to pursue, while others may choose to maintain current intervals. There is no right answer.
"I have worked with customers at both ends of it who have had very good oil analysis programs," Silveira comments. "Some have taken the route of extending oil drains. Others felt that, depending upon their maintenance cycle ? which is a big part of this ? it is safer to take care of the oil change [when a piece of equipment is in the shop for maintenance] than possibly run into a condition where it has been out there too long."