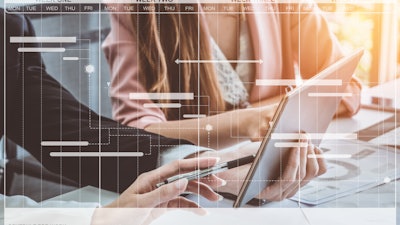
The Boldt Co., which performed more than $1 billion in work last year, attributes a large part of its success to the company’s commitment to adopting a continuous improvement approach. This approach includes implementing TouchPlan, an enhanced management software system that allows project managers at the company to have improved access to data that keeps projects on schedule, while reducing labor demands and increasing efficiency. The software aims to provide project transparency to improve team communication and allows teams to manage projects from one place.
“Our focus has been on executing projects more successfully; by making our plans visible to more project stakeholders, problems come to the surface faster and help our teams focus on what will make the project better and improve every day,” said Nick Loughrin, group manager of project delivery services at Boldt.
Boldt
Technology Supports Standardization, Improvement
Boldt has been a member of the Lean Construction Institute since that organization’s early days. The company’s focus on improving production led to merging its experience with Lean principles to create The Boldt Production System with its roots in the Last Planner System.
“The Boldt Production System starts with a master schedule and progresses to the development of production strategies per phase. Each phase will then have a make-work-ready plan that leads to the weekly, daily and production tracking levels of project execution,” Loughrin said.
The contractor’s efforts for improvement are, as they say, continuous.
“One of our main strategic initiatives within our growing company is to develop better standards based on our best practices within our company. We know we will have successful outcomes if we are rigorous and disciplined in our approach to implementing the Boldt Production System. We see TouchPlan as a technology to help us with that.”
At the end of 2021, TouchPlan officially became a part of the standard technology used within the Boldt Production System, the company’s process for planning and managing projects. Boldt has about 30 projects already using TouchPlan, and the company has ample knowledge of its value. Loughrin relayed how applying the software to an ongoing Wisconsin project corrected schedule-drift.
“The team would have probably found a way to finish on time, but it would have cost exponentially more by working overtime and adding resources. Working with the team to develop a production strategy based on flow, we were able to capture the plan in TouchPlan to further analyze and level out the resources and make the plan more efficient. We finished the project on time and with a lot less hours.”
Boldt
A Step to Smarter Data and Efficiencies
Boldt’s commitment to TouchPlan is a step toward smarter project management data—not just “are we ahead or behind schedule,” but also production and performance data that brings the project to the current schedule status.
“What we've traditionally done is taken our master schedule, captured in P6 or Microsoft Project, and added layers of detail per phase that is hard for the team to follow and understand, or we create a separate Excel file that can become disconnected from the master schedule,” Loughrin said. “Then, we manage constraints in a separate file or board as they are identified by the team. All of these different platforms to manage the schedule and constraints creates a cumbersome process and adds non-productive time to the project teams' already busy days.”
It's a process that works on any given project, but each project is its own silo of stand-alone data and inefficiencies.
“Now, using TouchPlan, we are able to tie our master schedule and the production strategy together in a clear and visual way that the team understands, and constraints identified are able to be captured and tied right to the plan. It takes less time to manipulate the schedule for updates and changes. Another benefit we are starting to realize is the performance data we are able to see across all of our projects. TouchPlan makes it easier and faster for us to share best practices and problems from one project to another.”