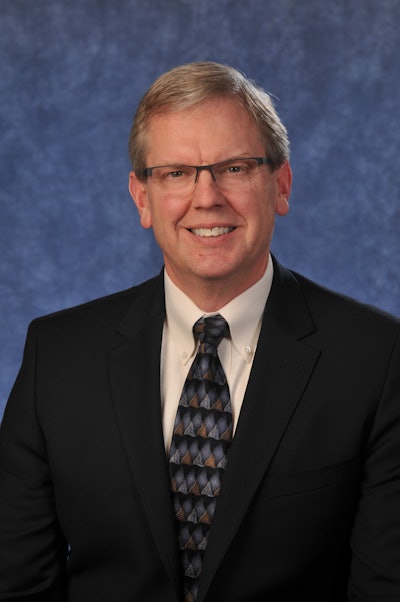
Safety for those working at height depends most heavily on operator training and a culture of caution, but what if the machines themselves could actively protect the operator? Sure, today's machines already incorporate numerous passive features that make them safer, such as pothole protection and load-sensing technology, but what is the next level of safety for tomorrow's machines?
This was the subject of a presentation delivered by Frank Nerenhausen, president of JLG Industries Inc., to attendees at the IPAF Summit held last March in Washington D.C. The intention, he says, was to get people in the industry to think about what's possible if all stakeholders make it their common goal to enhance safety and productivity for the people who use aerial equipment.
"I often tell my employees we have a very noble purpose as OEMs in this industry," Nerenhausen says. "We put men and women safely to work at height. As part of that responsibility, we need to find new ways to make the workplace safer, to make machines smarter, and to really stimulate the thought around advancing our concepts, our investments and our thinking toward that end. We want to spur critical thinking around what the next big thing is going to be in the aerial business. It's not about any individual manufacturer, but what the industry needs to grow and to prosper in this marketplace."
In his speech, Nerenhausen mentioned some technological advancements that could be seen on aerial equipment in the future. Some of it is already in use in other industries, such as collision avoidance systems in automobiles and augmented reality in training simulators, and some is more theoretical, such as the use of robotics and virtual reality to completely remove the operator from the machine.
"What we're really trying to do is take these machines and integrate ambient surroundings to make them even smarter," he says. "Augmented reality, for example, can be used in the workplace, or in the training environment. It creates that connectivity between the operator and a lot of complex things going around him in the ambient condition."
For those not familiar with the term, augmented reality is a live direct or indirect view of a physical, real-world environment whose elements are augmented (or supplemented) by computer-generated sensory input such as sound, video, graphics or GPS data.
"Augmented reality can help an operator stay in tune with what's happening with the machine itself. The capabilities of augmented reality include making the operator aware of jobsite issues, such as wind speed... all these things you need to stay aware of when you're performing your work. Augmented reality can create that integration with the machine, ambient conditions and the operator that would otherwise be pretty difficult to do if you're just alone in that basket. This is the next step."
Robotics, on the other hand, is really on the farthest reaches of what's possible with aerial equipment. Removing the operator from the machine and leaving him on the ground is perhaps the safest way possible to operate aerial equipment. Whether or not it's possible has not been determined yet, however, robotics are already being used in construction in the form of concrete breakers. Compaction equipment is another area where technology has made it possible for the operator to be far removed from the path of the machine he or she is operating.
"It's most conceivable to take technology that already exists in a different industry and apply it to ours," Nerenhausen says. "The industry has done some great things over the last 30 years and we've made some very extraordinary improvements in safety. Going forward, more refined obstacle protection will be within our grasp. Augmented reality is already being used in training, and we'll continue to push that forward. Robotics is out there on that continuum... it's not on the near horizon but we need to continue to work toward ideas like that for the long term."
He continues, "We'll look to any industry that has advanced itself in the aspect of safety, whether through scale or investment capability that our industry might not have. We'll be more than proud to borrow those technologies and integrate them into our machines to achieve that next level of safety for our customers and our operators. The automotive industry is a classic example, but there's also aerospace and military."
Ideas are exciting to think about, but cost is always top of mind when designing equipment.
"This is just the way technology matures. What we do now would have looked crazy to us 10 years ago, but we have to continue leaning forward and challenging ourselves with advanced prototypes," Nerenhausen says. "Ultimately, technology needs to be feasible economically, so we'll keep looking to other industries and borrowing for economies of scale. You can never say never. It just puts a cap on our ingenuity in the business, so we have to continue to challenge ourselves. Ultimately, some ideas will find a path to feasibility and others won't."
Service and maintenance are another concern when designing equipment. What effect would some of these advanced technologies have on the people who service the machinery? Will the industry need a different caliber of technician?
"Technology and durability don't necessary have to have an inverse relationship," Nerenhausen says. "When designed appropriately, the two will complement each other, just as safety and productivity can. Technology doesn't necessarily detract from life cycle cost. Technicians might have a different set of training requirements, or a different set of tools, but sophisticated advancements shouldn't dramatically affect the durability or serviceability of the machine, if designed properly."
Nerenhausen says he'd like to see the industry push all OEMs to think more broadly about technology that is currently out there and its applications in the aerial industry. "Safety is paramount. It's number one. And it's got to be an industry-wide initiative.
"The intent of the discussion about smart technology was to stimulate, stretch and encourage the entire industry to think about the integration of technology into our products. It is absolutely paramount for our industry to grow and flourish in the long term. We need to support that noble purpose we all share of putting men and women safely to work at height. When we do that, we'll see innovation come into the marketplace from all different angles."