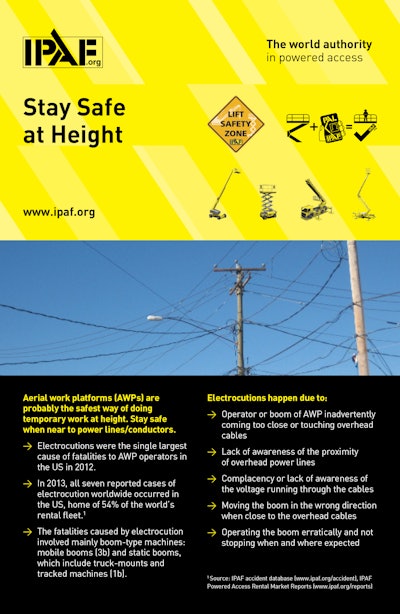
Prevention through design is a critical means to avoid hazards – just eliminate them. Pothole protection, limit switches that prevent elevation without outriggers being set or lowering travel speed over a certain height, and secondary guarding devices, are examples where designs have eliminated or mitigated hazards. Powered access equipment, including aerial work platforms (AWPs) and mast climbing work platforms (MCWPs), are a true masterpiece of design to allow personnel to safely reach temporary work at height. No climbing, no or limited assembly of many pieces – fully guard-railed platforms elevate you to the exact location of your work with ease.
But even when improved designs, enhanced options and accessories become available, there is no removing the potential hazards associated with working at height (a fall), certain tasks that must be completed (working on overhead power lines) or in the environment where the work is being performed (personnel or vehicle traffic in the work area).
Worker safety can be accomplished when a work risk assessment is completed and method statement developed to eliminate or mitigate risk and the plan is implemented, to include the proper selection of the access equipment for the site and task to be performed. The equipment should be properly maintained and repaired, the operator properly trained, familiarized and informed of the results of the risk assessment, and monitoring of compliance in place.
Every project must start with the completion of a risk assessment. IPAF partnered with several other industry trade associations to develop a best practice guide specific for AWP users (free download at the Publications section of www.ipaf.com). The guide provides information to assist users and operators in assessing the risk of potential hazards for the work to be done and implementing appropriate control measures to reduce or eliminate such risks. While this guide focuses on AWPs, it may easily be applied to other equipment.
A risk assessment must address known potential hazards. IPAF collects reports worldwide on fatalities involving AWP use. This data offers clear guidance on the potential hazards users face and must consider when choosing and using an AWP or similar equipment for their work. Some common hazards identified that should be addressed in all risk assessments are:
- Electrocution – proximity to energized power
- Tip-over – unstable ground conditions/overloading
- Crushing – caught between platform and exterior structure or object
- Struck-by – MEWP being hit by another vehicle/crane load/etc.
- Ejection – Not wearing required personal fall protection
As electrocutions have been identified as a leading cause of fatalities associated with the operation of AWPs, IPAF developed a easy-to-follow guidance for the typical operator who does not know what voltage may be in overhead wires: Stay at least 30 feet PLUS the extended structure of the aerial device (elevated scissor or extended boom) from power line supported by a wood pole and 50 feet PLUS the extended structure on lines supported by a steel tower. A demonstration of this best practice can be seen at www.ipaf.org/aLive
When selecting the proper equipment to safely perform the task, all aspects of the work must be considered. Ladders require carrying and placing the equipment in the right location to reach the work, climbing up and down. There are limitations of carrying tools or materials for the task, and limited area of work with each placement. If the ladder is not placed in the correct location, the risk of overreaching that can result in a fall can occur. Equipment selection must consider the added hazards that may arise from their use and operation (falls, trips, tip overs, dropping materials, etc.). Owning a particular AWP is not the only reason that it should be considered to complete a task either. All equipment must meet the needs of the workplace and task to be performed. The right equipment for the worksite and task is a critical decision for safety on the project that assists in the elimination or avoidance of hazards.
Even the best equipment selected for the job cannot prevent the risk from site hazards if personnel, both operators and their supervisors, are not trained. Understanding the regulations, standards and safe rules of operation recommended by the manufacturer are required, to include the site-specific risk assessment.
Safety is not complicated, but it does require an investment of time up front to ensure that proper planning and execution of the plan occur, and that workers are both effective and safe when performing their required task.